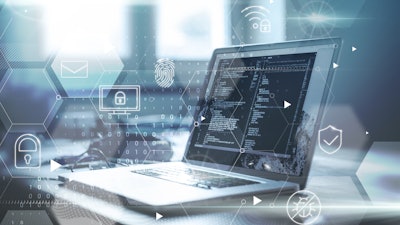
The COVID-19 crisis has confronted companies with many challenges in maintaining productivity and momentum in new product development. However, Stark Manufacturing (Stark) has quickly adapted by building upon its remote applications engineering capabilities. Stark already had the infrastructure and tools in place for remote engineering collaboration prior to the current pandemic and is now realizing their full potential. Regardless of whether working from the office or from home, the engineers at Stark can centrally manage projects through a secured network, central document database, and other software tools designed with flexibility and mobility in mind. Employees at Stark receive specific training to remain organized and productive while working remotely to ensure efficient navigation and changes to tight timelines necessary during new application or product development.
Stark believes that it is critical to continue supporting projects regardless of the ability to be hands-on at the customer’s site. Stark’s technical team combines its design and simulation software with 3D scanning of physical mock ups to seamlessly transition between conceptual designs and physical trial builds. Using customer generated data, Stark’s application engineers can scan surfaces between points to identify optimal routing of lines with consideration to costs, design reliability, and serviceability.
Stark’s customers are currently transmitting data for real-time collaboration or using email/FTP for raw data conversion to CAD. Stark’s 3D system will clean up and manipulate scans, then fuse a mesh of the scanned surfaces, converting the scan from a visual data cloud into usable CAD data. After data refinement, the export is available for use in any number of CAD packages. In addition to allowing for quick development iterations by transitioning between physical and digital information, the resulting CAD file can be used by the quality assurance teams at both locations to verify the accuracy of prototypes or first-off parts. Scanned measurements are compared against CAD data by either setting datums or best fit with statistical analysis of multiple parts to tolerances as precise as ± 0.1 mm depending on part feature and size.
Regardless of customers’ access to physical layouts due to COVID-19, Stark Engineers are supporting complex projects through fast and effective web-based meetings such as Teams and Skype, providing the ability to complete projects from the safety of their homes. Stark’s engineering team provides real-time point-to-point communications and multicast of communication across geographically diverse locations, and welcomes all web conferencing applications that contribute to the continued development of applications and products that address customer or market needs. In one customer’s words: “Stark supported building refrigerant line routing solutions, met delivery times on parts, provided inputs based on experience – all of this remotely. Stark maintained an excellent channel of communication during these challenging times!”
The power for companies to communicate and collaborate remotely is critical - Stark’s Engineering team is structured and ready to facilitate their customer design projects, regardless of where they are located.