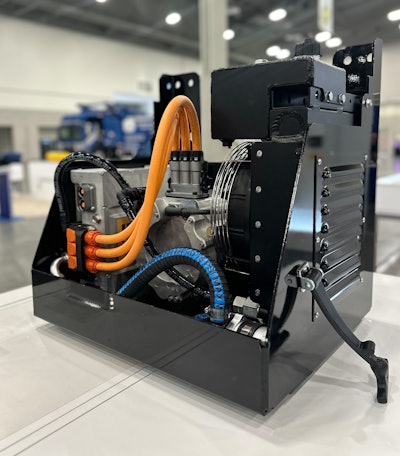
Construction sites have long been known to be major contributors of air pollution, causing the emission of particular matter, hydrocarbons and NOx (nitric oxide and nitrogen dioxide), among other harmful respiratory irritants. Construction vehicles further contribute to climate change through the release of greenhouse gases while their engines run.
Recognition of this problem is at the heart of stricter environmental regulations that are setting new precedents when it comes to monitoring air quality at and around work sites, including construction and mining sites. This is having a significant impact on what activities can be done at these sites.
The goal of this legislation is to improve local air quality which directly increases demand for zero-emission vehicles (ZEVs). The downside is that such efforts may limit the speed of completion of projects because they affect when and how long vehicles, such as dump trucks, cement mixers and material handling equipment, can have their diesel engines running.
A key challenge is that certain applications are harder to electrify than others. The level of difficulty and complexity is largely dictated by size. However, in looking back even just five years ago at what we thought was unrealistic to electrify and contrasting that to what is being accomplished today, there is no comparison. As an industry, we are electrifying components and applications that we never thought we could. And what we are seeing as far as results for the construction industry are spilling over to the mining industry, where ventilation systems ensuring air quality for workers are a primary consideration versus community air quality around construction sites. It is safe to say that nearly everything we are electrifying in construction is or will also be electrified in mining. At the heart of the electrification success story are electric power takeoffs (ePTOs), which power auxiliary functions on vehicles electrically, replacing traditional combustion engine methods.
Greater Design Flexibility
Although reduced emissions and cost savings are the most publicized benefits of ePTOs, there are others, including greater design flexibility and quieter operation.
With existing internal combustion engine (ICE) PTOs, you are constrained as to where you can put the PTO as it needs to be located where things rotate. More than 70% of PTOs on the market today are powered from the transmission. That’s a major constraint to have to take off power to rotational energy. In comparison, ePTOs have fewer constraints. With ZEVs you can take power off of the power distribution unit and send it anywhere on the chassis via cables or wires to then have ePTO power anywhere on the vehicle. This increases efficiency by putting hydraulic or rotational power very close to where it is needed.
When sourcing your ePTO, it’s important to consider your connections. A lot of people overlook the importance of considering the connectors and what you’re plugging in to. There are lots of different kinds of power connections, including quick connect and gland lug connections. Gland lug connections are very cost effective but require particular attention to detail for proper initial assembly and reassembly. Quick connect fittings offer greater mistake-proofing and speed up initial assembly and reassembly during a service event.
Today’s Modular & Integrated Options
The technology for ePTOs has been evolving for decades but, thanks to stricter emissions regulations today, the adoption of the technology has increased significantly to the point that there are now many different types of ePTOs available.
Several suppliers offer modular and integrated ePTO systems.
- Modular ePTO systems — These combine the electric motor-pump system with the necessary cabling, cooling, and fluid conveyance required into a complete mechanical package that can be mounted behind the cab or on the frame rail, allowing the user to only run the hydraulic work from the battery when needed, eliminating engine idle (if there is an engine at all).
- Integrated ePTOs — These designs allow us to simplify and increase system efficiency. Electric motors run most efficiently at 6000 RPMs and up, but there is not much on an ICE powertrain that runs at that high of speed. When you connect the motor to a pump, the motor might run most efficiently at 6000 rpms, but the pump can’t run that fast. An integrated ePTO can solve this problem. Some integrated ePTOs, like Parker’s e970, also contain internal coolant systems to prevent subcomponents from overheating. These can be configured with external coolers for higher and continuous power applications.
Future Options
New technologies are pushing the limits of what ePTOs can do on almost a daily basis to keep construction and mining sites productive and efficient while meeting stricter air quality and ventilation standards. Looking toward the future, there are three areas of emphasis that represent tremendous opportunities for these two industries: thermal management, reduced component footprints, and distributed work functions.
Thermal Management Advancements
Additional cooling options are a focus for future research with the ultimate goal of thermal management via ambient cooling. Many companies will strive for ambient cooling over the water ethylene glycol (WEG) power train cooling and auxiliary cooling options that exist today. Ambient cooling increases system efficiency by reducing the cooling system’s fan and pump loads.
Component Sizing
State-of-the-art integrated ePTO concepts are being developed by leading manufacturers like Parker to reduce the integration complexities of today. Integrated systems reduce package size while also decreasing installation time and cabling complexity.
Distributed Work Functions
One last point of interest when talking about the future of ePTOs is distributed work functions. Today, we see a lot of large centralized systems similar to ICE PTOs. These oversized systems use large motors, inverters and pumps. The challenge, beyond those related to size, is that it’s difficult to ensure you have the right amount of power where the work needs to happen. That’s where distributed work functions offer an advantage, creating the possibility for more compact system components and delivering sufficient power exactly to where it’s needed to perform individual work functions.
Electrification and decentralization of work functions enable flexible design options, making distributed work functions a possibility. Before these options were available, the design of many major pieces of equipment, such as excavators, had not changed much in the last 100 years. A key benefit of these new designs is that you relinquish restraint of the diesel powertrain which means more options for powering individual movements of machine components.
One of these newer designs is a hydraulic tilt motor, like Parker’s PowerTilt® NG, which swivels at 180֯, allowing the operator to do finer grading operations as a result of improved access control.
With an increased axis of articulation, these hydraulic tilt motors can do more detailed work using larger equipment. This significantly improves productivity by reducing the number of workers and shovels needed on the jobsite to complete finer tasks. Previously, multiple actuations like this were centrally powered where additional pump or flow capacity would need to be engineered. With distributed power through electrification, a powertilt could become an option and have its on electrified hydraulic power source.
Conclusion
Innovations continue to be developed to meet stricter environmental standards. In the process of doing more good for more lungs, construction and mining sites are discovering that they are actually increasing productivity and profitability. The ePTO is just the first step towards hybrid and all-electric vehicles which will one day be the way that work gets done.