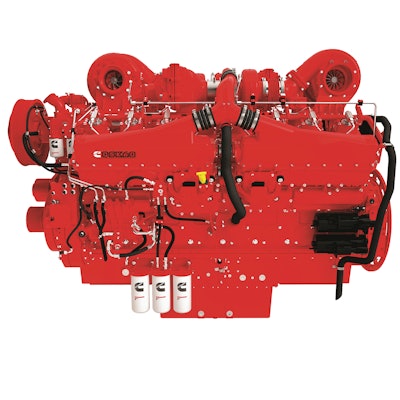
Cummins has announced it will outline its new bridge technology strategy and display advanced internal combustion products for mining applications on Booth 8991 in the Central Hall at MINExpo 2024.
Taking place Sept 24-29 in Las Vegas, Nevada, Cummins will be discussing the role of bridge technologies, such as hybrid solutions, in reducing mining emissions and total cost of ownership (TCO) for miners. Displayed at its booth, Cummins will also be showcasing its latest generation QSK60 and QSK95 engines.
An overview of PrevenTech digital solutions and a virtual tour of Cummins’ Master Rebuild Centre (MRC) will also be available to visitors at the MINExpo 2024 Cummins booth.
Molly Puga, executive director of strategy, product planning and digital at Cummins, said: “MINExpo 2024 is a great opportunity for us to discuss our strategy for helping miners achieve their carbon reduction goals — both in the short- and long-term. We’re keen to communicate the role emerging bridge technologies can play today alongside internal combustion engines in a diverse portfolio of power solutions for mining. We look forward to talking to customers about how we intend to achieve carbon neutrality in a way that supports TCO and the rigorous day-to-day demands of mining, highlighting how we can make immediate impacts, whilst progressing towards a zero emissions future.”
Hybrid Capabilities
Cummins hybrid capabilities will be discussed in its booth at MINExpo as an example of Cummins’ bridge technology strategy launch for the sector. Cummins will highlight its core, modular hybrid architecture alongside plans for both first-fit and retrofit applications for miners. Cummins believes hybrid solutions offer an affordable way to reduce emissions compared to alternatives like trolley assist and can be used in cohesion with HVO-ready internal combustion engines to generate additional emissions benefits.
Advanced ICE
Leading the showcase of internal combustion engine technology will be the Tier 4 Final/Stage V compliant Cummins QSK60, which delivers a maximum of 2850hp (2125kW) and a maximum torque of 8274lb-ft (11,218Nm). Equipped with advanced diagnostics and serviced by Cummins global distribution network, the QSK60 provides over 20,000 hours of operation before requiring an engine overhaul. This engine can then be rebuilt over three times throughout its lifetime, significantly reducing the potential total cost of ownership (TCO) for miners.
In addition, Cummins will be displaying its QSK95. This EPA Tier 2 emissions equivalent is the most powerful mining engine available and features an output of over 4400hp (3281kW) and a peak torque of 17802lb-ft (24136Nm). The 16-cylinder QSK95 is a clean sheet engine platform, designed with optimum power-to-weight ratio for 400T haul trucks, with engine ratings to maximize fuel efficiency and productivity. The engine also utilizes four single-stage turbos, alongside external oil and lube coolers, to improve engine serviceability.
PrevenTech
Visitors to the Cummins booth at MINExpo will also see the company’s latest developments in advanced diagnostics and prognostics with PrevenTech. The technology detects potential equipment health issues before they occur, informing operators of potential performance issues and recommended service ahead of failure and subsequent downtime. Cummins PrevenTech® is a system that can be installed on Cummins engines to reduce TCO from unexpected servicing for miners.
Cummins Global Support
At MINExpo Cummins will be discussing how choosing its engines leads to low cost of production thanks to its extensive aftermarket service and support. At its booth, Cummins ambassadors will be on hand to talk through a range of offerings, such as its PowerCare service contracts, genuine parts and more.
A virtual tour will also be available of the recently opened Cummins Master Rebuild Centre (MRC) in Krakow, Poland, the first of its kind in Europe. This tour will provide insight into how employees at the 4,600m2 MRC in Krakow rebuild Cummins high horsepower engines with displacements of 19 to 78 litres, and in the 450hp to 3500hp range, including renowned Cummins engines such as the QSK19, QSK38 and QSK60.
Cummins engine rebuilds go through a six-stage remanufacturing process that sees the engine disassembled, cleaned, inspected, re-machined, reassembled with Genuine Cummins parts and tested. As a result, the engine’s life is extended, its performance is enhanced and TCO is reduced due to greater engine uptime.