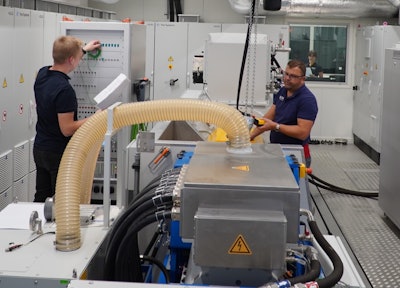
Eaton announced the completion of a major refurbishment of its test labs in Tczew, Poland. The updated facility now features advanced test equipment for internal combustion engine (ICE) and electrified vehicle (EV) powertrain technologies. A key addition to the facility is two newly installed powertrain dynamometers. The EV heavy-duty transient dynamometer is designed to support the development of cutting-edge heavy-duty (HD) eTransmission architectures. While the second electrified vehicles medium-duty dynamometer was added to facilitate both passenger vehicle and light to medium-duty truck powertrain architectures.
These dynamometers, alongside an extensive range of advanced equipment, allow Eaton to perform a wide array of in-house tests, including:
- Real-time powertrain-in-the-loop tests.
- Embedded electronics tests.
- Efficiency and thermal studies.
- Endurance and performance tests.
- Hot and cold environmental tests.
- Power electronics tests.
These capabilities enable the labs to address the demands of both traditional ICE vehicles and the evolving electrification landscape, ensuring Eaton’s readiness to deliver solutions for hybrid and fully electrified vehicles.
Modernizing a 120-year-old facility, reskilling
The refurbishment involved extensive infrastructure upgrades to the 120-year-old building. This included remodeling existing spaces, adding electrical and chilled water infrastructure, and installing specialized equipment, such as a vibration chamber and thermal shock testing systems. These enhancements support the testing of eMobility product lines, including inverters, DC/DC power converters, power distribution units, and power connections.
“The intention behind these labs was to enable us to test any eMobility product line locally and effectively,” said Dave Prange, lab manager, eMobility, Eaton’s Mobility Group in a press release. “The addition of new infrastructure and equipment gives us the flexibility and capacity to quickly meet complex customer demands, particularly for hybrid and electrified vehicles."
Eaton also has reskilled 99% of the Tczew lab workforce from traditional ICE technologies to electrified vehicle technology. Employees who previously worked on supercharger testing have transitioned to eMobility, undergoing training and self-directed learning to adapt to the demands of electrical testing, higher speeds, and more complex architectures.