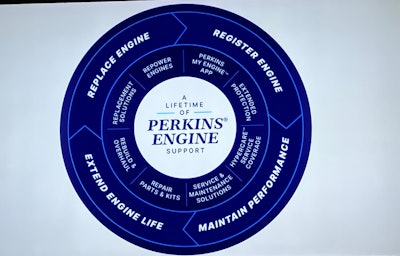
Condition monitoring and lifecycle management were two major topics of discussion at the Perkins press conference at The Design Studio in London. Understanding what’s happening with engines in the off-highway industries is critical and it’s even more important to get ahead of the curve whenever possible.
Jessica Langley, EAME marketing consultant at Perkins, described improved connectivity for condition monitoring as a new era in equipment management for original equipment manufacturers (OEMs).
“It’s not just a desire. They’re a necessity,” she said, highlighting how they’re developing a comprehensive solution that reduces downtime and costs while improving efficiency.
“We have several key OEMs including material handling and the construction industries who have it in their machines and are seeing the benefits,” Langley said.
The benefits include catching minor issues and challenges before the user knows it. Langley described an end-to-end solution that helps find the fault on the engine and get it to the OEM and get it up and running.
The result is it saves OEM dealers a lot of time and allows them to plan more efficiently. It also helps them avoid major breakdowns and faster resolutions. For any industry that utilizes off-highway vehicles, this is critical.
Kevin Walsh, digital business development manager for Perkins, described a six-step process for how they use condition monitoring to generate and provide insights for users:
- An engine anomaly is identified and a fault code is triggered.
- The fault code, along with any other transmitted data, is sent via an application programming interface (API) or interlink.
- The data is ingested and segregated into enterprise data storage and an advanced analytics ecosystem.
- Analysts or automated algorithms analyze the data and identify anomalies and potential causes.
- The OEM receives a recommendation for service or product support.
- The customer is then contacted for engine service.
Jessica Langley and Richard Bates discussed lifecycle management for engines at the Perkins press conference in London.Chris Vavra
The cycle continues this way and artificial intelligence (AI) helps improve the process, Walsh said, through the feedback and response loop to provide more efficient and accurate insights.
Improving lifecycle management in aftermarket
Langley described their approach to the aftermarket as about evolving and innovating solutions regardless of industry. She said they all have their challenges and needs, but they also have commonalities. Those can serve as a good starting point for future success.
Langley and Richard Bates, category growth manager at Perkins, described their emphasis on engine support with a wheel that consists of four pillars and eight key aspects to keep OEMs running despite challenges (see image).
Engine support for lifecycle management depends on four key pillars: Registering the engine, maintaining performance, extending its life and replacing the engine, which starts the cycle again.Chris Vavra
“Maintaining the product is key,” Bates said. “You want to avoid unplanned downtime by getting access to the information you need.”
He admitted the process can be tricky with so many options for different fleets, but they have worked to simplify the process within their product lines as well as parts management.
Even with condition monitoring and lifecycle management, not everything goes to plan. The off-highway industry often deals in treacherous and unpredictable environments. Sometimes, Bates said, a repair job isn’t the best option. Replacing the engine is sometimes the quickest solution to get the machine up and running. It also can be quite expensive and that can stay an OEM’s hand because they are trying to keep costs down.
Langley said the end goal is: “We want to support customers to operate to the best of their abilities.”