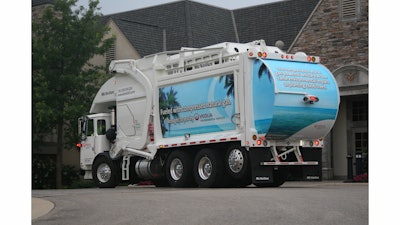
The trucking business has consistently been characterized by reliability, long life and small margins. Fleet managers track the smallest details looking for any opportunity to reduce costs. For those driving a lot of miles, fuel costs are a major concern and each political or weather event seems to increase the price. Unfortunately, the end customer doesn’t see this as a good reason to pay more for product transportation, so the trucker needs to make up the difference. The new fuel on the block is natural gas, and with the onslaught of fracking technology, natural gas is abundant in the U.S. It burns cleaner than gasoline or diesel, and the economics are impressive.
The cost of CNG is listed in gasoline gallon equivalent (GGE) or diesel gallon equivalent (DGE). The math is pretty simple. The delta in fuel costs multiplied by the number of gallons used per year is the savings. The upfront costs are needed to cover the conversion to a dedicated or a bi-fuel or a dual fuel system, and if there isn’t convenient access to a station like Kwik Trip or Clean Energy, there is the additional cost of a compressor station.
Natural gas is not as volumetrically efficient as diesel, so it is compressed under high pressure to store more gas in a vessel. In Europe, the operational pressure is 3,000 psi, yet in the U.S., the operational pressure of compressed natural gas is 3,600 psi. Nature’s shape for high-pressure storage is a sphere, yet that isn’t practical for transportation vehicles, so the next closest shape is a cylinder. Cylinders come in many sizes and in many materials which are designated in the following categories:
- Type 1 – Metallic, steel or aluminum
- Type 2 – Metal with fiber hoop wrap
- Type 3 – Metal liner with complete fiber wrap
- Type 4 – Plastic liner with complete composite wrap
The worse the mileage, the better the payback with CNG. Type 1 is the lowest cost and by far the most produced worldwide. Type 4 cylinders are the lightest, and the highest cost. Type 1 cylinders are used in a number of applications where cost is the highest priority and/or weight is not a major factor. Fork trucks, which normally add weight for ballast, will use the heavier Type 1 tanks when powered by CNG.
In countries like India, the tanks are largely metallic primarily due to cost, yet there is concern on safety of the Type 4 tanks. Type 4’s are banned in India according to Prashant Banerjee of Tata Motors.
In heavy trucks, most tanks are Type 4, mounted ‘back-of-cab’ directly over the frame rails, yet hidden behind the cab to prevent aerodynamic inefficiencies.
As in any alternative fuel, there’s a certain amount of range anxiety, and in CNG, this motivates truck owners to request as much gas as they can fit. Engineers are working to improve the packaging to maximize the volume of CNG; the premier system from Agility Fuel Systems can carry as much as 275 DGE, combining the back-of-cab storage with side-saddle tanks. Agility Fuel Systems accomplishes this while maintaining aerodynamics, aesthetics, durability and a lightweight design.
In consideration of an alternative fuel or alternative powertrain, the most important factor is the duty cycle, and with fuels like natural gas, it’s critical to understand the fueling infrastructure. Are there public stations nearby, or must the trucking company install its own fueling station?
In terms of drive cycle or duty cycle, refuse trucks are particularly attractive because of the inefficient start-stop duty cycle. These trucks drive every day, and when they aren’t hauling trash, the small owner/operator units are hauling construction site refuse. Refuse trucks are prime candidates to benefit from CNG considering their heavy weight, frequent usage and high fuel consumption. They represent the single largest growth area in CNG with 50 to 60% of the new refuse trucks coming off the line as dedicated CNG fuel engines. Much of the natural gas is stored either behind the cab, or on the roof-top mounted cylinders. There are instances where a customer wants more natural gas capacity, but there isn’t room for another cylinder. This situation has prompted additional natural gas storage vessel designs that can package CNG more efficiently than a cylinder.
The U.S. Department of Energy’s (DOE) Advanced Research Project Agency (ARPA-e) recognized that there were two major hurdles preventing mass acceptance of CNG – access to fuel and the inconvenient storage of the fuel. To address the accessibility challenge, home fueling has been developed to take advantage of the fact that 60 million homes already use natural gas.
ARPA-e is funding teams to develop non-cylindrical vessels to store high pressure CNG to tackle the fuel storage issue. There are multiple metrics for success including the shape, the cost (lower than Type 4 composites), the energy density and the weight. A leading team is REL Inc. (company information, 10797192), a technology development company who is developing an innovative cast aluminum tank. REL is trying to replicate the natural structural surface of a sea urchin, which is represented mathematically as the Schwarz P-surface. This is a volumetrically and structurally efficient shape, which makes it a great candidate for high-pressure gas storage. The cross section shows the cast tank with the P-surface internal structure.
This technology disrupts the norms of CNG storage. A tank can be shaped much like today’s gasoline tanks, yet still able to store a considerable amount of CNG. Integrating these tanks in a rectangluar box on a large truck would store 20 to 35% more CNG than the cylinders used today. The non-cylindrical design also makes it easier to place tanks in more areas of the truck, such as between the frame rails. All of this results in more fuel on the truck. Truckers want more CNG to ensure they will reach their destination (due to the lack of fueling sites currently available), and so they spend less time at the pump.
More CNG on the vehicles in storage locations that don’t hinder normal operation will lead to more consumer confidence and growth in natural gas in the U.S. Truckers will be able to reduce their fuel costs. The air quality will improve, and the U.S. will reduce its dependence on foreign oil. We all win.