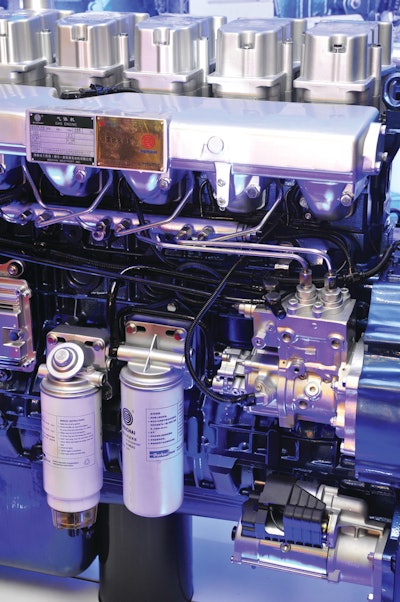
Large U.S. reserves and the ability to use existing engine technology make natural gas attractive. In fact, natural gas price projections are significantly lower than historical averages as more information becomes available on massive shale gas reserves.
Engine and fuel availability continue to expand. “We are in the stage of investment in both infrastructure build-out and product development,” says Paul Blomerus, Senior Director, High Horsepower Corporate Development, Westport Innovations Inc., Vancouver, BC, Canada. “Where those two meet is a perfect storm of new products to meet demand and available cheap fuel. Then we will see an inflection point.”
In the push to transition from petroleum-based vehicles to an affordable domestic alternative, natural gas is quickly gaining favor. Any vehicle traditionally powered by gasoline or diesel can be converted to natural gas. Although natural gas does produce greenhouse gases, it is much cleaner than either gasoline or diesel. It is an odorless, nontoxic, gaseous mixture of hydrocarbons—predominantly methane (CH4) and it possesses the lowest carbon content of any hydrocarbon fuel. A side benefit is that compressed natural gas (CNG) fuel systems are completely sealed, so there are no evaporative emissions.
But the economic business case remains strong. “There are so many different angles and they are all predicated on economics,” says Richard Kolodziej, President of Natural Gas Vehicles for America (NGVAmerica). "The more fuel you burn, the greater the potential savings.”
There is also customer familiarity. Natural gas already accounts for a quarter of the energy used in the U.S. But a couple of hurdles need to be overcome. First is development of the distribution channel. “There are two million miles of natural gas pipeline delivering gas to almost every city and town,” says Kolodziej. “You have to get it from the underground pipeline to the vehicle, so fueling stations need to be built."
There are about 1,100 CNG fueling stations around the country with 20 to 25 new stations coming online every month. But they are not equally distributed around the country, with most stations popping up in heavily populated areas. “The four counties around L.A., for example, have 100 stations,” says Kolodziej. Salt Lake City has quite a few stations and growth is now occurring in Oklahoma City, Tulsa and other key cities. "The industry’s strategy has been to go after return-to-home fleets first, where one public station can serve several fleets in an industrial park. Once there are enough stations you can go after other fleets, the ones that don’t return to a depot every night. After these natural gas fueling communities (the hubs) develop, the next step is to place fueling stations along the interstate highways that connect them (the spokes). Through this hub-and-spoke approach, a national CNG fueling network is being created."
Fuel availability is critical to the speed of growth. “A number of options can be employed in key market segments, from on-site delivery in the case of liquefied natural gas (LNG) for key machines, or strategic fueling locations nationwide in the case of rail,” says Scott Fiveland, GAS New Technology Manager, Caterpillar Inc., Peoria, IL. “The successful deployment of LNG solutions will require the economics through the value stream from fuel to infrastructure to fuel use. We expect the economics to look attractive through this business value stream.”
The other hurdle is the availability of the engines. Finding the perfect size engine for many applications can be difficult. There are gaps in the natural gas engine range – including a critical gap between 9 and 15 liters. Numerous companies use the 9-liter natural gas engine on a Class 8 truck. “That only works if you are working on flat terrain. Even there you are working that engine pretty hard,” says Kolodziej.
He explains, “That is why the 12-liter Cummins Westport engine that is supposed to come out in April is exciting for so many people. In many cases the 8.9-liter is too small and the 15-liter is too big.” A 12-liter natural gas engine hits a sweet spot for many in the Class 8 truck market.
Currently there is a 9-liter engine with the Cummins Westport Inc., Vancouver, BC, Canada, or there is the 15-liter Westport HD engine. More choices will be coming in the future that will help further fill in the gaps.
Actually, engine manufacturing capacity isn’t as much of an issue. “Our business model has always been to leverage existing manufacturing capacity wherever possible,” says Blomerus. “We will utilize engine manufacturers or existing supply chains. We really don’t see supply or capacity as an issue. If anything, as the share of gas increases the capacity will switch from supporting diesel fuel to supporting gas fuel.”
Engine types and use
Three types of engine technologies are currently employed for natural gas engines used on mobile equipment – spark ignited, dual fuel and high pressure direct injection (HPDI). The technology deployed depends on the application. “But [for] the largest and most demanding engines where efficiency and power response are core requirements, the HPDI is more suitable,” says Blomerus.
Natural gas needs an ignition source to make it work. It will not ignite by compression alone like diesel fuel. This ignition source is usually a spark plug in a spark-ignited engine or a small mixture of diesel in a compression-ignited engine. But you do lose a little torque and cooling requirements are increased.
Think of a spark-ignited engine more like a gasoline engine. “It has a more peak-shaped torque curve,” explains Blomerus. "You need to rev it up to get the power whereas a diesel cycle engine has a flatter torque curve which gives that nice low-end response.”
Westport uses spark ignition on light-duty (1- to 5-liter) and Cummins Westport currently uses SI on medium-duty (5.9- to 9-liter) engines. Many light-duty engines used on passenger cars and light-duty trucks are configured for bi-fuel operation. In medium-duty vehicles natural gas can also be cost effective with a spark-ignited engine.
An upside of the spark-ignited engine is that it is much quieter than a diesel compression-ignition engine. The downside of a spark-ignited natural gas engine is it typically provides 85 to 90% of the power of a diesel and 80% of the torque of a diesel.
But the spark-ignited engines also have emissions benefits. “On the Cummins Westport engines you don’t have a particulate filter and you don’t need urea to control the NOx,” says Kolodziej. Instead the engine relies on a three-way catalyst.
But many industries need diesel engine efficiency. Dual-fuel and HPDI technology provide the solution. In a diesel/CNG dual fuel engine the diesel acts as an ignitor to get the explosion going. These engines can be run on diesel or a combination of diesel and gas. The engines are started as a pure diesel engine and as the inlet air temperature rises natural gas is injected into the cylinder from an additional intake valve. As the natural gas is injected, the amount of diesel being injected is reduced. The average substitution in medium- and heavy-duty truck applications is often 50%.
This requires the engine to be certified as both a diesel and a gas engine and it lengthens the payback period since the engine is still consuming 50% diesel. But it is an attractive solution since the engine can run on 100% diesel when natural gas is not available. “A dual-fuel engine has all of the same emissions reduction technologies because there are certain conditions where a dual-fuel engine is going to be running 100% on diesel,” says Blomerus.
Caterpillar offers a unique dual-fuel technology with its dynamic gas blending technology, which has already penetrated the petroleum drilling market. “We are going to be moving that technology into mobile machinery,” says Fiveland. It continuously optimizes gas substitution up to 70% while maintaining diesel performance levels.
“The advantages of the technology are it retrofits to the engine,” explains Fiveland. “This can retrofit to any of the large Cat engines as long as you continue to meet the emissions standards.” The technology uses existing Cat gas engine hardware along with no change to core diesel engine components. “With dynamic gas blending you are putting gas in at a low pressure. Then you are injecting the diesel fuel in a very conventional way.”
Unlike gasoline or diesel fuel, there can be variability in its composition. “Very simply, the quantity of methane, ethane, propane, butane, etc. may vary with geographic location and season,” says Fiveland. The methane number (MN) is an index that quantifies the reactivity of the fuel. Low methane numbers (MN 30) contain higher-order hydrocarbons while fuels that contain mostly methane and ethane may exceed MNs of 80.”
Dynamic Gas Blending utilizes sophisticated control software that accommodates fuel quality changes. “So if you go to a lower methane number fuel the engine picks that up and dynamically adjusts the amount of gas or the amount of diesel fuel,” says Fiveland. It automatically detects gas presence, gas quality and gas pressure to optimize fuel savings while maintaining performance. Like any solution it has advantages in certain markets and segments. “We are going to continue to look at the customer payback. Dynamic gas blending is going to be applied where it makes sense to the customer.”
With HPDI technology, gas is introduced at high pressure directly into the combustion chamber. These engines run on 90 to 95% natural gas. A small amount of diesel is still needed as this technology utilizes diesel pilot injection. “An HPDI engine uses a small amount of diesel as an ignition source,” says Blomerus. “Typically it is such a small amount that you can still get the benefit of the clean burning gas, allowing you to reduce the cost and complexity of the emissions reduction equipment.” Again, this could be critical to industries such as railroads where new emissions requirements for diesel locomotives that take effect in 2015 will increase the initial cost.
“Direct injection is directly comparable to diesel engine performance,” says Blomerus. If an application requires low-end torque and responsiveness, then a diesel cycle with direct-injection gas technology is the best solution.
Fiveland agrees, “Power density is defined appropriately as power/engine displacement. Engines burning on natural gas can match equivalent continuous or variable speed diesel power requirements, within the same engine envelope.”
As publicly announced, Caterpillar is partnering with Westport to develop the HPDI technology for both rail and mobile off-highway markets. This engine solution is expected to provide the customer unsurpassed value with a substitution rate at the 95% level. The application of Caterpillar various dual-fuel options (DGB and HPDI) will be driven by the customer value they provide in a given market segment/application.
Natural gas storage considerations
Natural gas can be stored as a compressed gas or a liquefied gas for use on mobile vehicles. The main difference is that CNG is stored as a gas at 2,900 to 3,600 psi pressure while LNG is stored as a liquid at a very low temperature. The natural gas storage tanks and more complex fuel delivery systems will add cost to the initial purchase price of the vehicle.
But natural gas engines don’t care whether gas is being supplied by a CNG or LNG tank. “The gas that it receives is regulated to the temperature and pressure [required by the engine, typically 110 to 150 psi],” explains Blomerus. “The customer will pick an appropriate tank solution. There are advantages and disadvantages to all of the filling technologies.” One safety advantage for all natural gas vehicles is the gas is lighter than air and disperses quickly into the atmosphere when spilled. It is also worth noting that natural gas has a narrow flammability range which makes it a relatively safe fuel.
The storage volume required per unit of energy is larger for both fuels. “LNG requires a volume of about 1.7 times that of diesel to store an equivalent amount of energy,” says Fiveland. “CNG systems, depending upon the degree of pressurization (usually 3,600 psi), require upwards of four times relative to diesel and 2.5 times relative to LNG. In key industries, LNG fuel systems will be designed to continue to meet key customer requirements while not sacrificing payload, etc.”
“Up until now it has been more CNG than LNG, but that is changing very rapidly,” says Blomerus. Many recent announcements tout additional capacity being added for LNG. “CNG is very popular on return to base vehicles.” This is because trickle compression filling is a very efficient way to fill up a CNG tank. You plug in the compressor and you fill up the tank overnight when the electricity is cheap. “On an over-the-road haul truck the LNG is going to be a better choice for fuel – better range, faster filling.”
Caterpillar works with customers to match fuel system storage requirements with customer needs and executes the appropriate packaging on an application basis. “CNG does have some energy density storage challenges, but in some cases where CNG is directly available at a cheap cost, it can be utilized,” says Fiveland. “In this case, the appropriate storage technology and cycle times, derived via customer needs, will be designed into the products to maximize the customer value.”
A CNG vehicle usually gets less range than a conventional gasoline engine. Gas mileage for a CNG vehicle is similar to a gasoline engine, however, CNG tanks are quite bulky so integrating them into the vehicle can be a challenge. This compressed gas travels through a series of highly pressurized stainless steel lines until it reaches the regulator where the pressure is reduced to around 115 psi to match the amount needed by the fuel injection system.
There are also challenges with rapid fill on CNG. “If you want to get more gas into it quickly you need a big store of it at a high pressure,” says Blomerus. “It takes energy and if you compress gas it produces heat, so that is a challenge.”
This heat of compression can be overcome by using a time fill. “You plug it in and then you leave,” notes Kolodziej. “It is for fleets that have vehicles that come back to a common depot and they are not used overnight."
But LNG has two big advantages. “One is that you can put more fuel on board than you can with CNG with the same weight and the same space,” says Kolodziej. “If you have a weight problem, then LNG is more effective. If you cannot put enough cylinders in the back of the tractor or on the side rails of the tractor, then LNG is more attractive. If you want to get 500 or 600 miles of range you are going to have to go with LNG.”
The second big advantage for LNG is that it is not compressed. The heat of compression makes it difficult to rapidly fill a CNG tank to capacity. “If you pull up to a pump and try to put in 100 to 120 gallons of CNG equivalent, you only get about 70% of the capacity,” says Kolodziej. “It will read full, but an hour later the pressure will drop as the heat dissipates. You don’t have that problem with LNG.”
LNG tanks store natural gas in a liquefied state. Natural gas is liquefied by cooling to -260 F at atmospheric pressure. At this temperature LNG occupies one six hundredth the volume of natural gas at atmospheric temperature and pressure. It is stored in double-walled vacuum insulated stainless steel tanks. There is -200 F liquid in a thermos on the side of the vehicle. To use this fuel it is vaporized in a heat exchanger and gets to the engine at about 110 to 150 psi.
When the engine is not running the LNG fuel in the tank will slowly return to the gaseous form as the fuel warms, increasing pressure inside the tank. LNG inside the tank is stored up to 230 psi. If the vehicle is used on a regular basis, pressure inside the LNG tanks will be managed by the system. However, if the vehicle is parked for an extended period of time the pressure in the tank may increase to a point to cause the tank to vent gaseous fuel and reduce tank pressure. For this reason, LNG should not typically be used on vehicles that are parked for weeks at a time.