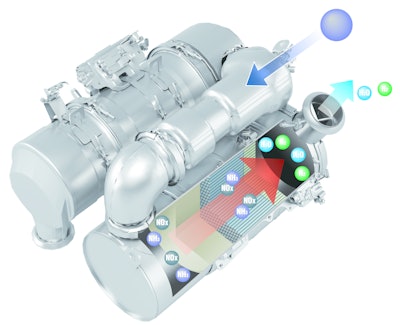
Komatsu America Corp. announces the introduction of its new EPA certified Tier 4 Final diesel engines, built on Komatsu’s progressive engineering improvements to reduce emissions. In addition, most machines will see reductions in fuel consumption below the already low levels that have long been a hallmark of the Komatsu product line. The Tier 4 Final technology will be integrated into Komatsu America’s construction and mining engines ranging in size from 3.3 to 46 liters and start commercial production in January 2014.
New regulations effective in 2014 require the reduction of NOx emissions to one tenth or below levels required by preceding regulations. Komatsu’s Tier 4 Final solution builds on the proven and reliable Komatsu technologies utilized for Tier 4 Interim engines. Examples of these Komatsu-developed technologies include: next-generation high-pressure common rail fuel injection (HPCR) system; high-efficiency exhaust gas recirculation (EGR) system; Komatsu Variable Geometry Turbocharger (KVGT); and Komatsu Diesel Particulate Filter (KDPF).
These Komatsu Tier 4 Interim technologies have been well received by customers in North America. In addition to refining these technologies through Komatsu’s continuous improvement activities, Komatsu has also developed a newly designed proprietary Selective Catalytic Reduction (SCR) device. This Tier 4 Final solution with the addition of SCR provides a high amount of passive regeneration of the KPDF with minimal impact on machine operation and production.
All Komatsu Tier 4 Final construction machines come with Komatsu CARE. Komatsu CARE provides scheduled factory maintenance for the first 2,000 hours or three years, which includes a 50 point inspection at each service, and two complimentary KDPF exchanges in the first five years.
Over the years Komatsu has consistently engaged in the research, development, manufacture and improvement of diesel engines. Komatsu will continue to leverage in-house development and manufacturing capabilities for key components, such as hydraulic devices and control systems, in order to reduce environmental impact and improve fuel economy.
Technologies applied to the new engines
Heavy-duty aftertreatment aystem
This new system combines KDPF and SCR. The SCR NOx reduction system injects the correct amount of AdBlue/DEF at the proper rate, thereby decomposing NOx into non-toxic water (H2O) and nitrogen gas (N2).
With the addition of the SCR system, a stringent design target of “fluid neutral” or better was established. In a fluid neutral situation, the volume of fuel burned plus the volume of AdBlue/DEF consumed is equal to or less than the total volume of fuel burned in the previous generation machine. This achievement lowers operating costs for the end customer as AdBlue/DEF typically costs less than diesel in North America.
To ensure product reliability and durability in demanding conditions, Komatsu developed the entire system, including the control software which is critical to the effective operation of the aftertreatment system. This control system is also integrated into the machine’s on-board diagnostics systems and KOMTRAX, Komatsu’s standard telematics system, which constantly monitors the machine’s health.
Heavy-duty Cooled Exhaust Gas Recirculation (EGR) System
The system recirculates a portion of exhaust gas into the air intake and lowers combustion temperatures to reduce NOx emissions. Incorporating a high-efficiency and compactly designed cooling system, increases EGR gas flow, which reduces NOx and helps reduce fuel consumption as an additional benefit.
Advanced electronic control system
To ensure control of equipment in all conditions, the electronic control system performs high-speed processing from sensors installed in the vehicle and engine. While maintaining the powerful and quick response of Komatsu equipment, the precise system helps greatly reduce NOx and particulate matter emissions while improving fuel consumption and noise.
The machine operator is informed of engine conditions via the on-board color monitor inside the cab. Using KOMTRAX, Komatsu’s machine health telematics system, to manage the information keeps customers apprised and informed of appropriate operational factors and required maintenance.
Komatsu Variable Geometry Turbocharger (KVGT) System
The KVGT system features Komatsu-original hydraulic technology for variable control of intake air-flow and supplies proper amounts of air according to load conditions. The machine’s control system uses the KVGT to provide precise exhaust temperature management for the regeneration process. The system achieves high efficiency combustion, further purification of exhaust gas and improved fuel economy.
Heavy-Duty High-Pressure Common Rail (HPCR) Fuel Injection System
Utilizing computerized control, the system is designed for proper injection of high-pressure fuel. Building on the technology in previous Komatsu engines, the new system uses higher-pressure injection for better fuel atomization, reducing both Particulate Matter (PM) emissions and fuel consumption under the wide range of engine-operating conditions.