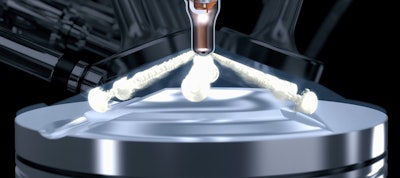
MAHLE Powertrain’s latest development of its passive MAHLE Jet Ignition (MJI) technology can now be easily added into existing engine designs with only minimal changes to the final machining process. Continued work throughout the lockdown period means that passive MJI can now be installed as a press-in unit into engines utilizing an M12 sparkplug, or larger. MPT will present the latest developments at Aachen Kolloquium being held the week of October 5, 2020.
“As the automotive industry seeks ways to unlock incremental efficiency and performance benefits from the internal combustion engine, jet – or pre-chamber – ignition technology is rising to the fore,” explains MAHLE Powertrain’s head of new technology and data management, Adrian Cooper. “We are beginning to see jet ignition being adopted into high-end production powertrains, such as Maserati’s recent Nettuno V6.”
MAHLE Powertrain has over 10 years’ experience developing its novel MJI pre-chamber ignition technology, which enables a highly efficient combustion process using either a passive or active system, suitable for use with either port or direct fuel injection systems. “We have worked with manufacturers and pinnacle motorsport such as F1 on the integration of this technology for close to ten years,” says Cooper. “However, our recent work on passive MJI makes the technology more accessible for adoption by mass-produced engines even as a retro-fit to existing designs, as part of a highly efficient powertrain.”
The passive MJI system features a small pre-chamber, which when ignited discharges extremely fast-moving, heated jets through a series of nozzles. This provides multiple ignition sites within the main combustion chamber, which leads to rapid, highly stable combustion and significantly improved knock mitigation characteristics. This enables the use of a higher compression ratio and in testing, up to a 10% reduction in fuel consumption has been measured.
MAHLE Powertrain
“We have also used the opportunity during the pandemic to further develop the cold-start and emissions performance,” continues Cooper. “Through careful development, we’ve been able to engineer a system that operates under these conditions without requiring a second ignition source, enabling the system to be applied to existing cylinder heads without the requirement for costly re-engineering. We have adapted an MJI-equipped production engine to start, run and perform reliably at -8 degrees C with equivalent catalyst light-off capability to conventional spark ignition. This is very encouraging, and we’ll be continuing development to lower this figure substantially.”
Cooper stresses that the key to maximizing the benefits of MJI is to understand the vehicle manufacturer’s requirements and develop the correct combustion strategy accordingly. “Our experience of integrating these systems means we can tailor MJI to many different applications, from low cost hybrid ICE to down-sized, high specific power engines or even to heavy-duty gas engines. While the engineering effort to integrate the MJI system has been simplified, other engine systems need to be further optimised in order to gain the largest benefits, which might include higher compression ratio, revised inlet camshaft profile and re-matching of the boosting system. A whole system engineering approach is the way to get the best from MJI.”
MAHLE Powertrain is now working on the development of a demonstrator engine to showcase the technology’s potential in applications between 80 and 120 kW.