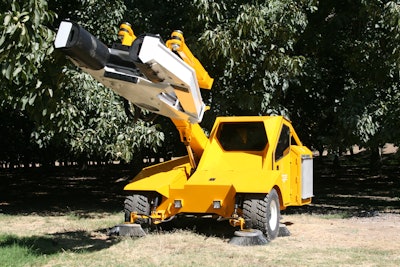
The COE M7 mono boom shaker is one of several pieces of specialty agricultural equipment designed by Coe Orchard Equipment (COE). Developed to ease nut harvesting, the mono boom shakes both tree trunks and limbs to remove walnuts, pecans and almonds from the trees on which they grow. It is capable of reaching the highest points on larger trees to ensure the most efficient nut removal.
The heart of the mono boom is the COE-designed TH7X shaker head. Once hydraulically clamped onto a tree, a hydraulic motor drives the shaker head’s internal components to create a shake pattern that will remove nuts from the tree. This shake pattern is adjustable in order to adapt to different harvest conditions.
According to Dave Short, responsible for working with COE’s dealer network and administering its warranty department, the shaker head’s energy wheels and hydraulic motor are the key components for creating the energy necessary to remove the crops. The energy wheels consist of two different diameter belt-driven wheels which rotate in opposite directions from one another and have varying amounts of weight placed on them to create the shaking pattern. “These two wheels are turning in opposite directions; one rotates clockwise, the other counterclockwise,” explains Short. “They’re slinging the weights as they rotate and this is what creates that pattern.”
Weights can be physically added or removed from the energy wheels to adjust the shaking pattern. This may be necessary if a farmer is going from harvesting a walnut to a pecan tree as the differing characteristics between the two trees and the ways in which their nuts are released require different shaking patterns.
Building it all in-house
COE builds the shaker head and its internal components in-house. Short says the company tries to build as much of the componentry and systems in-house as it can to better control the quality of the products put into its machinery. Hydraulic cylinders, hub mounts and doors are among the components built by COE, which includes forming them from sheet metal.
In addition, the company builds the chassis of the mono boom itself. COE developed the chassis in such a way that it acts as a counterweight to the very heavy shaker head. “The chassis is designed to balance the machine out so it’ll maneuver and perform better in the confines of an orchard,” explains Short.
Also unique to the mono boom is COE’s dual cool system. It is a stand-alone cooling system designed to cool the super-heated charge air delivered by the engine’s turbocharger. Cooling the charge air provides better performance and a reduction in harmful exhaust emissions. The system in turn enables the engine fan to efficiently cool the radiator, oil cooler and air conditioning condenser. “It’s a matter of efficiency and performance,” says Short. “We want to be able to cool those three components yet still achieve cooling for our engine charge air.” The dual cool system features its own fan and radiator to keep it running cool.
Protection from falling objects
Durability, as well as optimal crop collection were key drivers for the structural design of the mono boom. Eliminating all flat surfaces enables nuts to roll right off the machine, reducing the chances of farmers losing any of their crop. “Everything is angled so the nuts won’t be trapped in the machine,” says Short. “All of those different facets and angles are by design.”
To better protect the machine and its components from the falling nuts, Short says the company powder coats instead of paints the mono boom. Powder coating creates a more durable surface capable of resisting abrasion while paint would get chipped away each time a nut fell onto the mono boom from a tree. “The powder coat is a lot more resistant to being chipped and scratched, and basically worn off.”
COE’s mono boom shaker has been available on the market for several years now. And like many OEMs, Short says the company is always making subtle improvements to the machine such as optimizing the way hoses are routed. Recent improvements have included switching to LED lights and using a larger engine. “The basic machine is really a sound, efficient unit,” says Short, but making small changes when possible ensures overall performance continues to be improved.