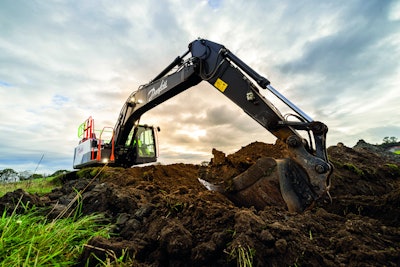
Among the usual suspects at this year’s Consumer Electronic Show (CES) were a few unusual names: Caterpillar, Doosan, John Deere, Kubota and HD Hyundai. Caterpillar’s booth was focused on electrification, while Doosan showcased its all-electric Bobcat skid steer loader.
Such high-profile demonstrations and the increasing frequency of electric machine launches might lead some to think the electrified off-highway machine industry is mature. The reality is a vast majority of OEMs developing electric machines are only in the first phase of the electrification journey. A great amount of uncertainty exists, with many OEMs questioning what and how to electrify; they don’t know what they need to know, what they should care about, and how they can get to the same stage as their CES-exhibiting counterparts. This article is for those OEMs.
We’ll look at the phases of the electrification journey, why hydraulic optimization is a key part of the journey, and levers for efficiency improvements in open-circuit hydraulic systems.
The Electrification Journey
Machine electrification is a complex journey that can be simplified into four phases. Advancing from one phase to the next increases machine efficiency, but also complexity, cost and risk.
Phase 1: It’s Electric
Most OEMs start the electrification journey by replacing the internal combustion engine with an electric motor and batteries. Coupled to that motor is a hydraulic pump with fixed or variable pump control. There’s little change to the system hydraulics and control algorithms.
Machine electrification is a complex journey that can be simplified into four phases. Advancing from one phase to the next increases machine efficiency, but also complexity, cost, and risk.Danfoss Power Solutions
This low-risk method enables OEMs to dip their toes into electrification and understand the associated complexities and challenges. For the end user, there’s not a significant number of changes, which can be both an advantage and a disadvantage. The major downside is that these machines today are not very efficient, hydraulically speaking, so runtime is often inadequate. Cost is another downside: they can be double the price of diesel equivalents.
As with many things surrounding electrification, runtime and cost comparisons are application specific. Take a mini excavator, for example. With no changes to the hydraulics, current runtimes are about 3 to 4 hours. OEMs want 6 to 8 hours, but they don't want to add more batteries, which is the major cost driver. Some customers can justify the 2x cost based on total-cost-of-ownership calculations, but they won’t pay much more. Aerial work platforms, on the other hand, have a much smaller cost difference between conventional and electric — so much so that in some countries, a significant majority of new machines are electric.
Phase 2: Optimize Hydraulics
An OEM could stop at phase 1 and wait for the price of batteries to come down — and that might make sense for lower-cost platforms. While battery costs are declining, pricing is still multiples of on-highway battery costs, driven by the packaging and ruggedness required for off-highway use.
Another option is to optimize the system hydraulics to improve machine runtime without increasing battery costs. This is Phase 2 of the electrification journey. Optimization levers include changes to the hydraulic architecture and technologies such as gravity lowering, independent metering, and zonal systems, which focus on driving out the inefficiencies of hydraulics.
OEMs are generally open to spending more on the hydraulics to save on the batteries, but there’s a delicate balance of upfront cost versus total cost of ownership many suppliers are trying to understand and, conversely, demonstrate to OEMs. The technologies necessary for optimization are more than just metal bits — it’s software, sensors, and associated costs, such as homologating the software to be functionally safe.
Phase 3: Let’s Recover
In Phase 3 of the electrification journey, we introduce energy recuperation, which captures and stores recoverable energy to further increase machine runtime. This phase can be a step change in complexity, depending on the application. Energy recovery is easiest in machines that often operate with one function at a time, such as boom lifts. In machines doing multifunction operation — think telehandlers, wheel loaders and excavators — the complexity of capturing energy while making the process smooth and imperceptible for the operator is much greater.
Phase 4: Fully Electric
The fourth phase of the electrification journey transitions into fully electric systems, meaning no or substantially reduced hydraulic systems. The benefit of fully electric machines is maximum efficiency, quieter operation, fewer components and less maintenance.
This phase of electrification is currently feasible and makes sense for more compact, lighter duty applications requiring lower actuation power. The feasibility of this phase for larger, higher-power machinery is currently limited, with power-dense hydraulics often the best solution.
The electrification journey is not universal; it’s highly dependent on application and OEM. Certain platforms will stop at Phase 2 or 3, while others are more conducive to Phase 4 electrification. The industry as a whole is still very much in Phase 1 of the journey. Even the leading OEMs in machine electrification are just starting to look at Phase 2, but this will quickly accelerate.
Why Hydraulics Are Inefficient
Hydraulic systems today work well. However, efficiency has often not been a priority for OEMs. The typical hydraulic excavator, for example, wastes up to 70% of the useful power delivered by the engine. In a conventional architecture, a single pump delivers flow to a control valve, which meters that flow to different services on the machine. While this architecture works well and provides good machine feel, it’s inherently inefficient because the pump supplies all the services at the same pressure demanded by the highest-pressure service. When digging, for example, an excavator arm might require 250 bar of pressure, while the boom requires 140 bar, and the bucket requires only 100 bar. The pump supplies all the services at 250 bar, and the valve meters that pressure down for the boom and bucket, which burns energy across the spools and generates heat. This is known as a meter-in or flow-sharing loss.
Additional losses in the system include meter-out losses, used to control overrunning or lowering functions on a machine. There are also pumping losses, which are associated with converting prime mover power to hydraulic fluid flow. Valve inefficiencies increase pressure upstream, which drives greater losses throughout the hydraulic system. By making the valve more efficient, it’s possible to make the whole system — including the pump — more efficient. This is the focus of Phase 2 of the electrification journey, and it’s a critical step to increase the feasibility of large machine electrification.
Danfoss Power Solutions
How to Improve Hydraulic Efficiency
There are several actions that can be taken to improve hydraulic system efficiency, from considering different architectures to implementing advanced technologies. The first requirement, however, is a change in mindset. Most of today’s machine control systems are linear in nature, meaning they are reactive to inputs and operational conditions. The operator moves the joystick, sending a signal to the controller. The controller commands the valve, the valve sends a message to the pump, and the pump demands a torque from the engine. This can lead to siloed component selection with limited focus on function and performance synergies.
Electrification and trends such as autonomy and intelligent controls demand more integrated solutions. To act efficiently and perform correctly, more intelligence and communication between components is required, which makes it critical to select components that work well together. Integrated systems that combine valves, pumps, and electric motors can maximize performance and efficiency. Suppliers know where their products run most efficiently and can generate control algorithms to operate at those peak points. Ultimately, many efficiency optimizations involve much more than swapping out a component.
Regeneration & Gravity Lowering
The first area for optimization is regeneration, which means reusing flow and pressure that's already in the system. Boom gravity lowering is the prime example. Platforms such as telehandlers today require pump flow to the rod side of cylinder to open a counterbalance valve to lower the boom. Electronic load-lowering valves provide direct lowering control and the ability to recycle head side flow back to the rod side, requiring no additional pump flow. This saves energy, mitigates many stability challenges with traditional counterbalance valves, and meets load control requirements.
Independent Metering
With conventional metering valves, a single joystick/spool controls acceleration and braking of a function simultaneously. In a car, this would be akin to braking while still applying the throttle when going downhill, then applying more throttle but still braking while climbing a hill. For independent metering valves, each work port can operate independent of the other, enabling more efficient and better control of services that transition between passive and overrunning states. Returning to our car analogy, independent metering valves operate more like a traditional car, only braking or accelerating when needed. This increases energy efficiency and frees horsepower to do other functions.
Variable Margin Control
Additional pump pressure, typically called margin pressure, is required to push flow through the valves and hoses out to the various machine functions. In conventional systems, this margin pressure is fixed. However, the actual pressure required to achieve the desired flow is variable based on flow demand and other factors. If a pump is providing 20 bar margin pressure when only 11 bar is needed to achieve the desired flow, this wastes energy.
Electronic load sensing or variable margin control enable the pump to dynamically adjust how much margin pressure is provided. These technologies tailor the pump pressure to the flow demand in the circuit. While this might only be a reduction of 5 to 9 bar here and there, it adds up in efficiency when managing large flows over a long day.
Energy Recuperation
Energy recovery, or recuperation, means using existing overrunning energy in the system to back drive an electric motor for battery charging. This is Phase 3 of the electrification journey, but it’s important to distinguish between regeneration and recuperation as the terms are sometimes used synonymously. It’s possible today to recover energy quite easily on single-motor/single-actuator applications. In fact, scissor lifts have demonstrated significant energy savings by using such technology.
For multi-function machines, recuperation is more challenging. While it is possible, there are not many examples of implementation because of the complexity, cost, and potential impact on operational feel. For these reasons, many OEMs see bigger benefits in and are currently more focused on regeneration.
Alternative Architectures
Much higher efficiency improvements are possible with alternative architectures, such as distributed, multi-pump, and flow summation systems.
In both distributed and multi-pump systems, the central control valve is often eliminated in favor of distributed controls (i.e., a valve applied to each actuator). This offers improved control, more efficient regeneration/recuperation, and provides load holding/hose burst mitigation without the traditional counterbalance inefficiencies. Additionally, the distributed valve arrangement reduces the number of fluid conveyance lines to just two: a pump supply and a tank rail. This enables the use of larger hoses, which improves efficiency by reducing hose friction losses.
Distributed architectures often have a single motor and pump, while multi-pump architectures feature a pump and motor per service. A multi-pump architecture can further reduce meter-in losses from a single pump flow sharing between services and enables energy recuperation without impacting other services. The trade-off is the power cannot be shared between services and each pump/motor must be sized for full function performance. This will increase system hardware capability, cost, and size.
Finally, flow summation is a variation on the multi-pump architecture that maintains the central control valve to provide selectable flow sharing. This enables many of the benefits of the multi-pump architecture and the ability to combine flow when using higher flow/power functions. It could support multiple motors and pumps, or a digital displacement pump with independently controllable outlets.
Danfoss Power Solutions
Operational Efficiency
Beyond hydraulic system efficiency, there are other ways to increase machine efficiency. General operational efficiency can be improved by automating certain functionalities. It can take operators several years to master the controls of a heavy machine. A new operator may hit the end stop more frequently, which dumps flow over a relief valve and generates heat. By giving operators automated functionality that enables them to leverage best practices right away, they not only become more productive, but it also makes the whole system more efficient. Rather than watch a machine’s bucket come down to ensure it doesn’t hit the ground, for example, the operator can press a button to bring that bucket down to the correct point every time. Meanwhile, the operator can focus on his or her surroundings or getting the machine elsewhere.
Now, Next, Future
In short, hydraulic optimization for electric machines goes beyond selecting more efficient components. This is the reason there's going to be — and OEMs will gain more value from — validated system solutions ready for machine integration. The future of hydraulics is application-specific optimized solutions for each phase of the electrification journey.
What’s important to keep in mind now is that off-highway electrification is in its early days. There is no magic bullet, but technology will evolve and advance at an increasing pace. In the last century we’ve gone from pure mechanical controls to manual hydraulics followed by analog then digital electrohydraulics. Electrification is the next step in machine transformation, and although it will look different, hydraulics will continue to play a major role in off-highway machinery.