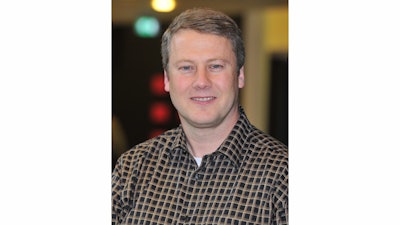
[GLOBAL] What are the economies you are looking at for future expansion and growth? Has the current conditions in Russia/Ukraine or other international situations affected your current or future business plans? If yes, how?
Danfoss has specific growth and investment strategies associated with China, India, Brazil, and Russia. Danfoss will be reviewing the economies of the MINT (Mexico, Indonesia, Nigeria, Turkey) countries to understand potential for investment and growth.
The current conditions in Russia/Ukraine are contributing to an overall slowing in the demand for a variety of mobile equipment, including agricultural machinery. We of course continue to align with the sanctions against Russia as required, and we continue to monitor the business development in Russia to align our investment plans with the market requirements.
[POLITICS] What political/government regulation/standard/bill was passed in the past year that most affected the way you do business and go to market?
Tier IV Diesel Engine Emission regulatory standards, and the safety regulations in Europe.
[POLITICS] How do you foresee this effect continuing into next year and in years to come?
The Tier IV Diesel Engine Emission standard has required companies to direct their engineering resources on integrating new engine packages in off-highway equipment. By many accounts, this activity is only 60% complete and will require the next eight years to fully complete. Equipment manufacturers will be seeking solutions that allow them to manage power more effectively, improve fuel efficiency, add new machine capabilities, and offset the costs associated with the Tier IV engine implementation. Due to the Tier IV effort, minimal investments in machine innovation and technology development have been made over the past six years. Now that engineering resources are being freed up, equipment manufacturers will invest in technology development and new types of innovation. Similarly, the safety regulations in Europe have and will continue to drive new product development to help our customers meet the safety requirements.
[CONSOLIDATION] Have you seen an increase in industry consolidation through mergers and acquisitions this year over previous years? If yes, to what do you attribute this trend?
No, not at this time (the strength of the global economy has supported company growth and profits). The potential for consolidation exists in specific areas of slower growth and lower profits.
[CONSOLIDATION] What positive or negative effect has the industry’s trend toward consolidation and system co-development had on your business model and how you evaluate new projects and opportunities?
We are seeing more opportunities for integrated solutions where customers are seeking ready-to-go subsystems that can be easily and quickly integrated into vehicle designs. These opportunities also bring challenges to manage many parallel paths of co-development with our customers. We have invested in vehicle-level capabilities that allow us to test and optimize subsystems onsite by partnering with our OEM’s design teams. Our focus is on risk reduction and configuring solutions that exactly meet the needs.
[CONSOLIDATION] Now that Tier 4 Final is underway, many companies’ engineering resources have been freed up to refocus on developing new products instead of refining existing products to meet regulatory expectations. Have you seen this refocusing? What does this mean for future engine development?
Yes. Equipment manufacturers will invest in technology development and new types of innovation to differentiate themselves from their competitors and increase the value to the end customer.
We see equipment manufacturers are very interested in energy saving solutions, turn-key solutions addressing functional safety, and solutions that improve machine function but at a lower cost than today’s. For future engine development, there will be focus on cost reduction and reducing the machine space claim currently required with T4f engine systems.
[TECH OF THE FUTURE] Where is the heavy-duty vehicle industry lagging (technologically and/or manufacturing process)?
Technology development, particularly in the areas of electric drives and telematics. There are also opportunities for improvement on design processes that leverage modern, digital tools to accelerate design, development and release of complex vehicle systems. One example is vehicle systems simulation and linking development to manufacturing through digital collaboration and automation.
[TECH OF THE FUTURE] What technology breakthroughs are necessary to propel the mobile off-road industry forward?
The development of electric drive capabilities, including power source. Hydraulic energy storage technology in compact, cost-effective designs. Sensor integration.
[TECH OF THE FUTURE] What current ideas and new technologies have the most potential for future gain?
The availability and usage of machine data (duty cycle, diagnostics, etc.) to optimize the productivity and service life of the machine.
[CHALLENGES] What new challenges have arisen that effect the way you design or manufacture your product? How you do business? How you go to market?
Developing products with similar configurations, but with varying degrees of component technologies (high performance versus economy performance) that match the performance requirements of the vehicle and the market the machine is being used in, for example, Europe verses India.
How does Danfoss’ new application center in Ames, IA (and other locations) fit in with the company’s current and future business goals?
Mobile equipment manufacturers are faced with the challenge of maximizing the utilization of their engineering resources (working on Tier IV, development, and innovation) and reducing the time to market. The Application Development Center assists mobile equipment manufacturers in addressing both of these challenges. The pre-work completed by Danfoss allows the manufacturer to more quickly and efficiently evaluate solution alternatives and select the solution that best addresses the needs of their business and customers. This allows the equipment manufacturer to place more engineering focus on areas of core competency for their business.