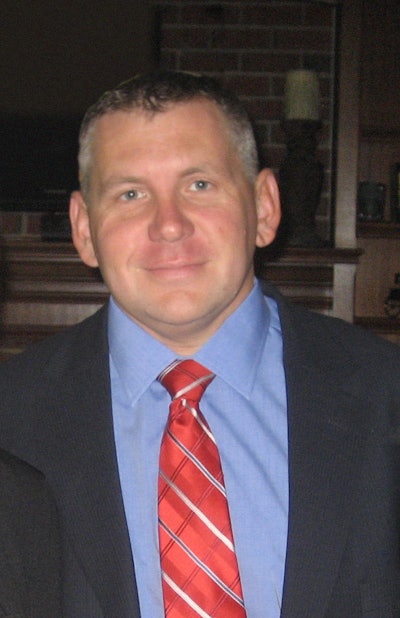
Responses from Keith C. Weiss, Senior Vice President, Industrial Sales, SKF USA Inc.
Technologies of the Future: Hybrids, Electrification and Smart Systems
Has there been any recent advancement in hybrid technology which will help, or have the potential to further increase their prevalence in the heavy-duty equipment industry?
Heavy equipment manufacturers designed and released hybrid power systems to improve the fuel economy and operating performance. Hybrid technology and its application vary with the OEM. Hybrid powertrain technology achieved high success in automotive field. However, due to high load, low speed and periodic operation, hybrid technology cannot be directly applied in heavy-duty equipment (construction machinery, wheel loaders, excavators, mining trucks, and others). This brings the attention back to hybrid powertrain technology. Recent advancements have been made in the construction machinery space, specifically in the wheel loaders and the excavators, and these solutions offer a unique strategy for energy conservation.
In regards to hybrids, what technological limitations currently exist that are impeding the ability to harness the full potential of hybrid power?
Current challenges in hybrids for heavy equipment are around powertrain configurations. There is a lot of work being done by the OEMs in this area. Compared with traditional heavy equipment, an additional energy storage device is required, which increases the initial cost of the equipment.
What progress is being made by SKF and/or the industry in regards to developing fully optimized systems as opposed to individual components [e.g. overall powertrain optimization versus optimizing the drivetrain and engine separately]?
SKF is not involved in making and delivering systems; we focus our efforts on [a] component level, SKF focused efforts in improving power density of the components, improvised sealing solutions, reduced friction, and application specific designs, and these directly tie into powertrain optimization. SKF’s state of the art analytical tools play a major role in the development of application specific bearing and seals designs and further play a major role in the overall efficiency of the drive train.
What role is electrification and smart systems playing within your company’s product designs?
Electrification and smart systems bring the mechanical and electrical regimes together. The impact of VFD’s (Variable Frequency Drives) and direct driven motors on bearings and mechanical components is very heavily investigated at SKF. SKF’s experience with railway electrical systems, electric motor testing and predictive analytics puts us in the forefront in the design and development of compatible products. Miniaturization and application of technology are becoming more and more critical, and SKF is also on the forefront for this development.
How has or will the use of prognostics and predictive technologies continue to progress within your product designs, and the industry as a whole?
Machinery prognostics and predictive analytics continue to progress at a high rate. There is a lot of interest for these technologies in the marketplace. However, the definition of predictive analytics and requirements varies with each customer and there are no industry regulations for heavy equipment. With the advent of big data and IoT (Internet of Things), the landscape for predictive analytics is changing rapidly. SKF has vast and unparalleled experience with traditional predictive analytics and machinery health services. We are focusing on miniaturizing the technology to fit and adapt to the needs of our customers.
One such example is SKF Insight for bearings. Miniature electronic circuits, powered by the motion of the bearing itself, transmit process data via a wireless link. There is no need to supply external power. This makes the technology supremely unobtrusive, because there are no wires ‘in’ to provide power, or wires ‘out’ to deliver the signal. This means it will work in places that would previously have been impossible. Just imagine trying to take signals out of a rotating gearbox, for example: it would be a complete mess, with entangled wires everywhere. With SKF Insight, signals can be taken from anywhere, and we are already developing solutions in challenging applications in wind turbines, mobile equipment and steel manufacturing.
What’s next on the technology horizon? Are there emerging technologies which will affect your products or the industry as a whole? How will hybridization, electrification and smart systems continue to progress within the next year and on into the future?
Total cost of ownership, emission requirements, energy conservation, and fuel efficiency are driving heavy equipment manufacturers towards developing more sustainable hybrid solutions in the marketplace. It is clear that there are uncertainties around the approach and the final solution (based on equipment and the upfront costs). However, the benefits outweigh the hurdles and OEMs are increasingly bringing hybrids into the spotlight.
At SKF we are focusing on fine tuning the products to bring better and higher value to the customers and make them more competitive. This will help in reducing the total cost of ownership to our customers. There is also a renewed focus in miniaturizing the technology and applying it to asset and life cycle management of the heavy equipment.