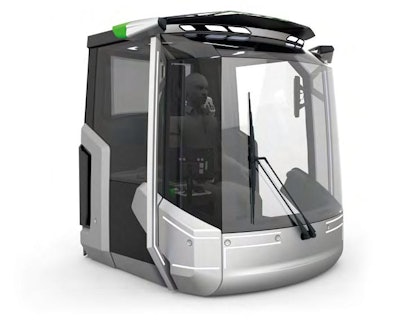
What would you design if you had no performance parameters to match, no client expectations to meet, no design restrictions, and a team of system experts willing to collaborate and create the best integrated product possible? These were the questions posed by the CAB Concept Cluster (CCC), a consortium of 13 established OEM suppliers and industry experts that united in 2014 to create an OEM-independent, innovation-driven, fully integrated and optimized cab system—the Genius CAB.
The Genius CAB concept was developed and led by the Technical University (TU, Technische Universität) of Dresden which has one of only two tenured chairs of Construction Vehicle Development in the world (the other residing in Japan). This wealth of industry research on technology trends and the future of construction vehicles was incorporated into the design concepts that were vetted by construction firm Max Bögl and presented to the cluster partners.
“As the project was led by the Technical University (TU) of Dresden, all business decisions were made by a neutral organization. TU Dresden’s experts always tried to keep negotiations equitable and make decisions that did not favor any one OEM. The management structure was very lean, and tasks were distributed between all the cluster partners according to their capabilities,” says Dr. Johannes-Jörg Rüger, President of Bosch’s Commercial Vehicle & Off-Road unit
The prize-winning overall design was the work of Prof. Dr.-Ing. Jens Krzywinski of the TU Dresden, and Wanja S. Steinmaier from the design agency Lumod. The concept cab was launched officially at bauma 2016 in Munich, Germany where the cab design received the bauma Innovation Award in the design category, as well as the VDBUM special award.
“We didn’t want the design to be something so futuristic that it was unlikely to come to fruition for another 10-15 years,” says Dr. Thomas Hiebaum, Corporate Vice President - Global Off-Highway, HELLA. “We instead focused on creating a cab system that leveraged advanced but available technology that could be implemented into the next generation of cabs in the construction industry.
“We have worked hard to create the workplace of the future for an operator in our industry, and to create a workplace for multi-machine operation, to drive automation forward, to enable cloud-based management, and productivity improvement. We have let creativity flourish, involving young apprentices, fully accredited universities and operators, and have asked fleet managers to question our ideas to give us new insights,” he says.
“The future trend in off-highway vehicles is for maximal efficient system integration accompanied by an increasing digitalization of equipment and cabs. We are all intensely concerned with our customers’ needs, with how the market of tomorrow will look and with how we can begin developing and implementing that today,” says Fritz Schadeck, Vice President of Fritzmeier Cabs. “The Genius CAB is our response to the challenges of the industry.”
The CCC set out to demonstrate what would theoretically be possible if it were able to co-design and develop system integrated solutions at an earlier stage of the development process and thereby generate interest with OEM customers to pursue such solutions.
“We are not trying to tell an OEM that we are better at designing or developing a vehicle or cab,” Hiebaum says. “What we are trying to convey is that integrating the systems together intelligently at the beginning of the design and development process, and by thinking about what you want to achieve with system integration, you can reduce the overall cost of the cab while including functions that would otherwise be impossible to realize with the current vehicle design process of designing the vehicle first and then sending out RFQs for components to comply with the design.”
By exploiting existing synergies, the cluster partners were able to develop and implement the Genius CAB as a customer-neutral innovation platform in the space of only 18 months. The team highlights group communication at such an early development phase as the key to what was a smooth and easy design process. “There were no big hurdles,” says Schadeck. “A couple of times there was product overlap between partners which required some discussion as to which would handle the component or system’s development, but once a decision was made, the design was able to move forward without a problem. It was extremely simple.”
Design challenges arise when system developers are brought in at the end of a vehicle’s design process and asked to make a part fit into a design that didn’t necessarily take the part’s features into consideration. One such example is as simple as the work lamps, which HELLA supplied to the Genius Cab design.
“The work lamps are fully integrated into the cab structure,” says Hiebaum. “They didn’t have to be mounted onto the vehicle using specially designed brackets; they didn’t have to be protected with cages; there was no need for cooling fins for heat dissipation.” By working with Fritzmeier directly through the entire cab design phase, the lamp was incorporated into the structural design of the cab, including a joint thermal simulation to define how the lamp would be fitted into the aluminum frame to create a safe-to-the-touch heat dissipation away from the lamp. “Normally we would have to create heat sinks with powder-coated aluminum die cast parts that would be mounted to the work lamps in order to cool them, which were completely eliminated through the collaboration with Fritzmeier,” Hiebaum says.
Furthermore, the lamp design was able to employ an intelligent dimming feature to allow the brightness to change based on the bucket location to avoid glare-back from the backside of the shovel. The Matrix Beam work lights from HELLA are able to refrain from illuminating specific areas in order to avoid dazzling drivers. For example, while the bucket of a wheel loader is raised, it is not illuminated and the light is routed past it.
“With just the work lamp alone, we were able to enhance three functionalities (mounting, heat, glare) that dramatically reduced part production, simplified the overall system, and saved on production time and overall cost, which can be passed along to the OEM customer,” says Hiebaum. “At the same time, we added a wealth of functionality that could never have happened if the lamps were added at the end of a vehicle’s design phase.”
Design breakdown
The technical innovations were able to be developed simultaneously with a consistent and agreed upon styling concept which created a cohesive and unified cab design. Systems and technologies that were integrated into the Genius CAB were able to exceed global market standards of safety, intuitive operation, operator comfort, maintenance and design.
A key benefit to the collaboration between these system experts is the precision tailoring of every component to not only function optimally on its own, but to add value to the other components as well, all while keeping the machine operator and owner in mind. “It is the bringing together of the individual component innovations and the functional links of a large supplier network,” says Rüger.
According to Rüger, the CCC's key objective was to increase safety in construction environments, especially by improving visibility and awareness of surroundings for machinery operators. “A safer construction environment is also one that is more efficient and cost-effective. Bosch’s sensors and displays detect impending collisions and warn of potentially dangerous situations, benefiting both machinery operators and other site workers. State-of-the-art lighting concepts help to reduce reflection and glare. Innovative air-conditioning systems and ergonomic controls make the operator environment more comfortable as well. And all these sub-systems need to be connected in an intelligent way, which is done by [Bosch’s] body computer module.”
The exterior
The exterior alone, designed to resemble a cut diamond, exemplifies the robust system integration and functional capabilities of the collaborative engineering effort of the CAB Concept Cluster partners.
The most significant innovations contributed by Fritzmeier Systems were its integrated SoftCab hybrid structure solution made of welded special aluminum profiles, which led to a weight reduction of 30%, and the form-compliant EXO-ROPS steel elements that are mounted additively on the cab and can be configured for weight classes from 10-50 T.
“All of the interior cladding that is integrated into the cab structure and the window elements leads to significant cost advantages in series production for the OEMs,” says Schadeck. Other features from Fritzmeier Systems are the cab’s newly developed details such as the ergonomic door handle and the electrically movable sunshade. The interior space is improved through removal of the steering column.
The windows provide plenty of visibility and, being aligned at specific angles, reduce unwanted distortion. The protection rails positioned in the blind spot of the A-posts are not only part of the rollover protection cage, they also serve as handrails, cable conduits and—with LED lights—as signature elements. SignaturLight by HELLA consists of flexible LED light strips encased in an impact-resistant silicon element and modules integrated into the ROPS structure.
Ultrasonic sensors from Bosch are integrated into the exterior to provide additional visualization of the surroundings. The sensors detect dangerous situations by displaying relative positions and nearby obstacles, and do not depend on light, thus significantly increasing the standard of safety. The Bosch body computer enabled a programmable centralized network architecture to be implemented which lowered the number of supply cables, relays and fuses while allowing for customized control of the onboard sensors and actuators via CAN (J1939), LIN or directly.
Instead of mirrors, there is a camera system combined with a variable view reversing camera from MEKRA Lang – used for the first time in a cab for an off-highway vehicle – which provides better surround visibility, especially in the dark. It can also be used to display hard-to-see areas at the rear of the vehicle on the mirror-replacement displays from Bosch located inside the cab.
The interior
Inside the Genius CAB, suppliers focused on the ergonomic features of the driver’s workplace including clear information management, the latest in HMI features, as well as the physical layout of the cab’s interior. RAMSIS, a 3D model of a human in the form of ergonomic analysis software for CAD designs, aided in the development of operator conditions like ingress, visibility, ease of access to functions and seat position.
“Our part within the CCC project was a complete system consisting of an innovative, ergonomically optimized driver seat with electrically adjustable features, plus a multifunctional armrest and 12-in. multi-touch display for controlling all vehicle and seat comfort functions,” says Hubert Wittmann, Off-Road Product Manager, GRAMMER AG.
The seat is linked to the vehicle's CANbus system and includes a driver detection system for immediate and completely automatic adjustment to each operator. A force-feedback joystick combined with physical buttons is fully-integrated into the armrest. This means that all the functions and machine characteristics that the driver can control are centrally visible and can be modified at any time, even under adverse working and lighting conditions.
Numerous electrically powered functions are present on the seat, including adjustment of the seat's fore/aft position, height, backrest and seat cushion angles, giving the driver optimal comfort for everyday work. All of these features are controlled by the multi-touch display, eliminating the need for conventional, manual seat controls. It also opens new possibilities for customizing the cab's interior design, since the ambient lights of the cabin and seat are coupled to one another. This enables extras such as illuminated logo on the backrest or illuminated piping which is coordinated with the overall cabin design to evoke a special cab atmosphere.
GRAMMER AG was also in charge of developing the architecture of the graphical user interface (GUI). “The goal was to develop an innovative, user-friendly interface for the multi-touch display. In cooperation with the Dresden University of Technology, [we] designed an intuitive, well-organized, touch-sensitive panel that maximizes workplace ergonomics,” says Wittmann.
The aforementioned central body computer supplied by Bosch operates on a complex modular CAN matrix that links and controls all of the CAN-enabled components and their functions, as well as processes the incoming and outgoing signals.
Smart cloud technology from SAVVY Telematic Systems uses RFID tags to record the working and operating times of the operator and the equipment, register the equipment status and log possible damage. For example, the scene-based lighting control satisfies customers’ increasing demand for convenience and comfort, and the active access control system from HELLA and SAVVY Telematic Systems fulfills the demand for increased safety and security in all areas. By means of appropriate key codes, it is possible to flexibly broaden or restrict the range of functions available to the operator.
The air-conditioner from AURORA can be conveniently controlled by the machine operator via the central touchscreen panel. The set of new-style air vents have been optimally arranged for individual, tailored ventilation together with the heater and air-conditioner.
The quality of maintenance inside the cab is significantly enhanced by the use of RFID-chipped air filters from HYDAC. The service life and usage state of the filters are continuously monitored. There is no longer any need to replace filters ‘just in case.’ The cab interior takes into account the space required for air ducts, and particularly the need for easy access to the filter system. This is especially important for the particular requirements of the construction and agriculture industries.
The CAB Concept Cluster’s collaboration and unified mission to develop a technologically advanced operator cabin successfully demonstrated the massive potential of more efficient and effective system integration earlier in a vehicle’s design phase. “We continually pushed the envelope of the integration concept and have created a unique project that carries considerable weight in the international markets,” concludes Georg Fritzmeier, owner of the Fritzmeier Group.
The CCC’s next project has already begun: An optimized and integrated cab system for the agricultural equipment industry is to be ready and presented at Agritechnica 2017 in Hanover, Germany.