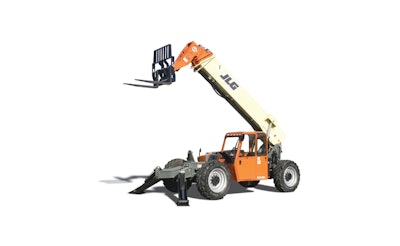
The demands of today’s global industries have drastically increased from even five years ago. Modern technologies are a must to tackle a range of challenges which historically might have seemed impossible to overcome. The off-highway vehicle sector is a prime example of where new and pioneering technologies and solutions can have a significant impact on performance, lifespan and return on investment.
Within the off-highway vehicle sector, manufacturers are certainly taking more of a holistic approach to the complete design of the vehicle. This all-encompassing focus includes wheels, which are no longer seen as a commodity product but an integral part of the vehicle design. Manufacturers want wheels that will deliver optimum performance, a long lifespan, and represent value for money whilst benefiting from higher payloads, faster vehicles and increased efficiency.
GKN Wheels has invested heavily in research and development to make this happen. The company also prides itself on working closely with its customers and industry regulators to ensure that each wheel is right for their every need, rather than simply adopting a ‘one size fits all’ approach. This leads to a greater understanding of a client’s requirements, and ensures a customized solution is developed to meet specific and often challenging environmental conditions that off-highway vehicles have to perform within.
Take for example its recent collaboration with leading equipment manufacturer JLG industries. The company wanted to ensure its products had a strong point of differentiation from competitors, which led to the development of a solution that delivered not only enhanced telehandler stability and greater tread life, but also lower operating costs and gave the customer a unique position in its market place.
GKN Wheels was approached to design and develop the new wheel, chosen for its engineering and expertise, as well as the in-house test capabilities. The new solution was developed alongside Bridgestone Americas’ Off Road Division, which ensured the wheel was designed to complement the new Firestone Duraforce MH tyre.
The unique GKN design resulted in a 28 in. diameter size, rather than a traditional 24- or 25-in. version. This new wheel fitted the tyre geometry and has a specific shape, which enables it to support the loading and durability requirements of the telehandler, while using a lighter than average 8 mm gauge steel.
While the agricultural sector does not change as rapidly as some of its off-highway counterparts, there are still improvements and developments taking place to deliver a range of benefits. Low pressure tyres are used extensively in agricultural applications to minimise the risk of soil compaction and while this addresses one issue, another one is created. As these tyres have stiffer walls, they are more difficult to fit.
It is therefore clear to see why the sector has responded well to GKN’s Profi-fit and Profi-line products, which offer easier fitting of low pressure tyres. In addition, they combine high strength with reduced weight as a result of a sophisticated rim design. This utilises a rolled over flange and a double ‘bump’ profile, which minimises stress and allows the rim gauge to be reduced with no loss of performance.
To develop this more structurally efficient rim profile, detailed research using Finite Element Analysis and acquisition of stress data by use of strained gauged wheels was carried out. This was in direct response to working with agricultural customers, looking at the issue that needed addressing, and investing time into a project which has resulted in a product with a clear advantage for the end-user.
These differing examples show how wheels should be adapted for specific environments, challenges and to meet a variety of demands. The off-highway sector is very broad, and within this industry every market will have its own individual needs and wants.
Let’s turn our attention to the defence sector. The vehicles used for military purposes call for a markedly more customized approach than the mainstream automotive industry. They require robust solutions, which can handle a range of challenging terrains and harsh environments, as well as all weather conditions.
To tackle these, sophisticated, independent suspension and advanced driveline solutions are a must. In addition, there is a shifting focus towards light-weight solutions which don’t sacrifice function, mobility or safety of the troops. Budget is also an inevitable consideration and is having a major impact on fleet availability, so upgrades and refits of existing assets are likely to become increasingly commonplace as opposed to investing in new vehicles.
Looking at all of these demands, it is clear that a specific solution for the military industry is required to address these issues. As with other industries, GKN has worked closely with key military manufacturers to find solutions to overcome these concerns, while still delivering best value for money.
A key development in this area is the Squeezeform process. This allows for the production of lightweight, high strength aluminium components, as well as accommodating cast-in inserts using other materials, which provides locally improved wear resistance.
The resilience of these wheels has been proven on tracked military vehicles, showing durability with loads of up to 40 tonnes. In addition, the wheels offer increased endurance; four times that of a typical traditional forged steel wheel.
But the major benefit of wheels produced using this technique is that they are 35% lighter than their standard counterparts. This weight reduction represents a 300kg saving across the whole of a vehicle bringing invaluable improvements in operational performance and running costs.
Of course, none of these products would be brought to market without robust testing and validation by GKN and customers. CAD analysis tools are used, alongside value engineering and competitive benchmarking to ensure performance is achieved with the minimum component weight and at optimum cost. Other sophisticated testing facilities include component, systems, axle, and full vehicle testing using multi-axis Remote Parameter Control (RPC) software.
The tests performed on prototypes are part of an integrated complete solution approach, with a particular focus on durability and correlation of results. This is all underpinned by using state of art data acquisition techniques, software simulation tools, proving ground or field trials to back up all testing assumptions.
There is no doubt that the demands of the off-highway vehicle sector are changing, albeit some industries more quickly than ever before. However, with wheel manufacturers investing in research and development to consistently bring new products to market and deliver innovative, customized solutions, this should deliver reassurance to vehicle manufacturers and end-users that these integral components are not being left behind – and, indeed, are at the cutting edge of development.