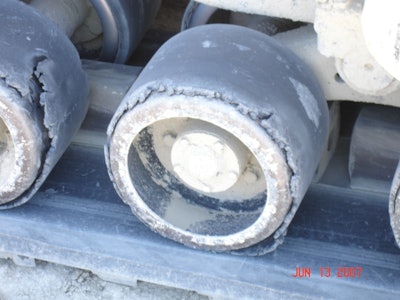
Superior Tire & Rubber Corp. has been supplying urethane undercarriage wheels to the rubber tracked tractor market since 2002. Beginning in 2008, Superior has been an OEM production supplier of these wheels. Superior’s undercarriage wheels are targeted specifically for heavy-duty applications. Over 20,000 wheels have been supplied with zero warranty. Urethane wheels have proven to not debond and maximize track life and lower operating costs.
What is wheel caused track damage versus normal wear?
Track damage is not minor cosmetic cuts, chipping and splits caused by abrasive debris. This damage is minor and part of normal wear due to surface conditions. Tracks with the inside surface damaged and tracks with excessive guide lug damage are not normal wear. The most common and severe track damage is broken or protruding track cables and heat related damage caused by friction. Due to excessive heating and cooling over time the rubber material of the track breaks down allowing the cables to pull to the inside of the track. Also the friction, caused by the friction between the rubber wheel and the track guide lug, on the inner track surface can cause the track to have excessive heat buildup and melt the track rubber.
How do wheels cause track damage?
Loose debris between the track and the wheel over time embeds into the wheel material as the rubber on the wheels becomes fatigued. Broken or chunked tire material, torn rubber due to debris or track misalignment and bond failure due to heat buildup. Other damage to the track can occur when a bearing seizes which then in turn causes the wheel to not turn properly. Typically this will build up excessive heat in the track and cause a failure. Other causes for wheel damage to the track are insufficient clearance between the wheels and the guide lugs which causes excessive rubbing of the lugs and wheels not matching the guide lug configuration. This interference causes extreme heat build-up, rubber compound break down and wheel failure.
Typical OEM rubber bogie wheel interaction with the rubber track
Due to the high coefficient of friction of the rubber wheels they tend to build up heat during operation and the longer the run time of the tractor the longer they run at this elevated heat. This often happens when roading the tractor. Over time the rubber weakens due to the heating up and cooling down process. Once the rubber weakens it loses what cut and tear resistance it has and becomes susceptible to debris such as gravel getting stuck to the wheels which in turn scores the inner track surface.
Also as this heating up and cooling off occurs over time the adhesive bond between the steel wheel and the rubber will give way and fail. This is typically first evident on the outside edge of the wheels and then comes across to the inside causing a total failure. If the wheel becomes completely de-bonded and is left on the machine debris will cause the steel to develop flat spots or become sharp causing further track damage.
Xtreme Urethane bogie wheel interaction with the rubber track
Due to the low coefficient of friction for urethanes the heat buildup that happens with the rubber wheels does not occur. The urethane will run much cooler and does not experience the heat and cool cycles like the rubber does and does not break down and weaken. Due to not weakening the debris issues do not exist. Also with the lower coefficient of friction the urethane wheels do not cause the track to heat up.
The high cut and tear properties and the lower heat operating environment allows the urethane wheels to wear evenly and to maximize both wheel and track life.
Will Xtreme Urethane’s increased hardness damage the Track?
A common scare tactic used by rubber wheel competitors is that with the urethane material being harder it will cause damage to the interior surface of the track. Let’s first look at 20 Rockwell hardness steel. Steel only wheels will damage tracks for a couple of reasons. The first being that there is no flex between the wheel and track which can cause debris to embed in the track causing both tearing of the track surface and damage to the steel due to trapped debris not allowing the wheel to turn. The second cause for damage is that over time and duty cycles the steel rusts and that rust damage causes pitting in the steel surface which in turn becomes abrasive and damages the track.
The Xtreme urethane does flex and has a hardness of 90A durometer compared to 72A for the OEM rubber. The rubber wheels are only 20% softer and urethane has shown no damage to rubber tracks in over three years of intensive side by side testing with the OEM rubber. In not one test case was the rubber track damaged due to the urethane wheels and in every case the tracks that had the urethane midrollers were either equal or looked better than those running the rubber wheels.
Comparing the hardness of the urethane wheels to the hardness of the track rubber you find that the guide lugs are actually about the same hardness in durometer 91A for the guide lug and 90A for the urethane wheel. Also the surface that the wheel rides on is 80-81A in hardness.
The urethane wheels do not cause damage primarily due the fact that the surface of the urethane wheels is not only harder but slicker than the OEM rubber which in turn does not allow for debris to stick to the wheels and cause track damage. Another observation was that with rocks and gravel the urethane tended to impede them from scoring the track as due to the rebound of the urethane the debris bounced out of the track to the ground surface.
The major cause of track damage is the buildup of excessive heat which initially causes wheel failure which then in turn causes damage to the track. With Xtreme urethane wheels the need to be constantly checking wheels for damage is eliminated and productivity is increased.
Finite Element Analysis
To determine the actual difference in the hardness of the urethane and rubber on the rubber track we performed a finite element analysis and as a comparison also included bare steel. In illustration 1 you can see that we utilized the load of the wheel and the width of the contact area on the track for this comparison.
We then drew models of the track with each the poly wheel (illustration 2), the rubber wheel (illustration 3) and the steel wheel (illustration 4).
We then loaded the wheels in increments of 500 lbs. up to 4,000 lbs. and plotted the wheel and track deflection (illustration 5) on the same utilizing the rubber and urethane wheels. For the rubber at 4,000 lbs. the track deflection measured .078 inches and for the urethane the measurement was .081 inches. This extrapolates to a urethane wheel deflection increase of 3.8% over the rubber wheel track deflection. This is a very minimal difference and the graph is shown below in the Load vs. Track Deflection Plot graph (illustration 6).
If you then graph the contact region of the wheel to the track for each material (illustration 8) at 4,000 you get 2.5 inches of contact for the rubber wheels, 2.45 inches for the poly wheels and 2.3 inches for the steel wheels. The rubber wheel has a 2% larger contact region than the urethane wheel and an 8.7% larger contact region than the steel wheel.
From this analysis it is quite clear that the slightly harder urethane wheels have very little effect on the rubber track.
Urethane Worklife History
Superior Xtreme wheels have a track record with a major Tractor OEM with over 20,000 wheels shipped in the last three years and many that were used in the initial OEM tests and the warranty rate is 0 percent. We have been producing Xtreme wheels for the aftermarket since 2003 and due to no bond failures instituted our no bond failure guarantee in 2008 which simply means that if one of our Xtreme wheels ever de-bonds we will replace it.
A competitive advantage stemming from Xtreme Wheel technical excellence is that with our Xtreme Wheels the major manufacturer was able to increase their track undercarriage warranty from 2,000 to 3,000 hours in Agricultural applications and doubled from 1,000 to 2,000 in Construction applications. These industry leading wheel warranty values of 2,000 and 4,000 hours exceed by 100% the common track warranty periods of 1,000 and 2,000 hours.
There are currently many Xtreme wheels running in heavy duty applications in the field with over 5,000 hours and they still exhibit no signs of failure.
Current OEM data does not show an estimated worklife for the Xtreme wheels because there have been no failures to date but the number is well past the rubber worklife average of 1,150 hours.