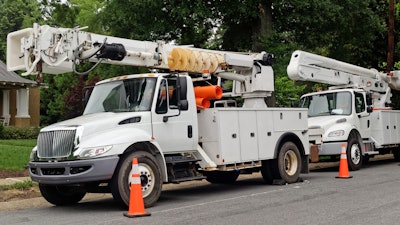
The growing demand for electric work trucks has kept manufacturers on their toes. Emissions mandates, cost-saving strategies, and performance expectations are pushing the work truck industry to invest substantial resources into the development of electric vehicles.
For manufacturers, it’s crucial to remain at the forefront of these new demands without sacrificing quality and service. In a previous article, we discussed how manufacturers new to the electric market can start the process of designing and building electric work trucks. From finding the right OEM to developing electric-capable cabs, manufacturers can create a solid foundation for electric vehicle production. Here, we will explore the process for completing vocational upfitting on electric chassis.
What are the goals?
When starting the process of upfitting on electric chassis, one must first understand the common mission of all the stakeholders involved in the initiative. The adoption of electric trucks and their implementation into fleets is more complicated than many realize, and everyone has to be on the same page for how these trucks are being built and why they are being built. important step in electric work truck manufacturing and fleet adoption.
For this to happen, meetings should be coordinated by the electric chassis (OEM) project leads to bring together the end user, fleet managers and operators, body builders, upfitters, and all other parties that will have a say in the final product. You must discover early on if the goals of these stakeholders are feasible and align with the capabilities of your manufacturing teams. The goals must align with specific state and government mandates. Once this is done and everyone agrees on the goals, you can begin to discuss what duties the truck has to accomplish.
Understanding the goals of all stakeholders is the most important step in electric work truck manufacturing and fleet adoption.Marion Body Works
What is your application?
Electric chassis can be applied to trucks for a number of applications. Flatbeds, service trucks, streetsweepers, and dump trucks have been the most prevalent so far, with utility boom and peripheral vocational trucks also gaining attention.
Determining how an electric truck will be utilized is important for implementing an electric chassis. Power requirements, frame strength, and additional customization requirements for the application determine how the chassis is modified to satisfy the truck work functions.
Additionally, emissions standards like the California Air Resource Board (CARB) Regulations can be challenging to achieve if a holistic solution to the electric work truck application is not implemented. A chassis designed to meet all of the emissions certifications for one application may not meet the requirements for another application. It’s essential to know the truck’s application upfront to ensure your end product is CARB compliant.
When an application is chosen, you can get into the technical aspects of the truck.
Power requirements
Creating a power profile for the truck’s application will help you determine the number of batteries needed for the appropriate amount of kilowatt hours (KWh) for your chassis system. The number of batteries is equivalent to the number of pull hours and the truck’s duty cycle time. A typical profile can be created using variables such as average miles driven per day, load, terrain, and understanding duty cycle of all auxiliary functions.
Knowing your application’s power profile also helps you know the truck’s charging cycle, which can be applied to an entire fleet to optimize operational efficiency and load (power) management.
Connecting your chassis
For the most part, electric truck chassis can be kitted mechanically so that 80% of their makeup stays the same when upfitting, while the remaining 20% is customized to equip the truck for its intended body and application. The primary changes occur on the frame rails and the alignment of the holes for the mounting brackets for the body and additional batteries on the chassis platform. With an electric chassis platform, end users can choose the specific body and cab they want for their truck.
Another challenge on an electric vehicle chassis is converting battery power to hydraulic power for work functions. Since there is no PTO to drive the hydraulic pump, the chassis manufacturer will need to understand how to size an electric motor-driven hydraulic pump system for the specific function. Additionally, electronic controls and telematics should be integrated into the chassis and body for all work functions and communicated on a CANbus network. This allows the telematics system to provide diagnostics, remote troubleshooting, and performance data of the complete vehicle to a fleet manager or service technician. Knowing battery life and overall vehicle health saves time and resources once that truck hits the road.
If manufacturing a chassis for a boom on a truck, for example, the loading profile for the hydraulic system is needed to understand the worst-case analysis for pressure and pull, in addition to engineering the appropriate resistance bending moment (RBM) frame strength for the application for which the boom is being installed.
Manage what you can
While the implementation of electric work trucks can be complicated, the actual upfitting and building of the truck is fairly straightforward once the goals, application, and technical components have all been determined. Many of the challenges with electric vehicles occur beyond the scope of your influence as a manufacturer. A fleet manager may be separate from the service that operates the vehicle, the maintenance shop may be different from the operating service, and the battery service may also be a separate operation. With so many different people and entities playing a part in managing fleets, the adoption of electric trucks can change the entire operational dynamic and make the transition difficult for some or many.
Your role as a manufacturer is to equip the necessary stakeholders with the information and solutions they need to fulfill their electric vehicle goals while remaining an ongoing partner in vehicle and fleet optimization. By supplying your customers with vehicles on the proper electric chassis and managing your areas of expertise well, your upfitting jobs will be successful.