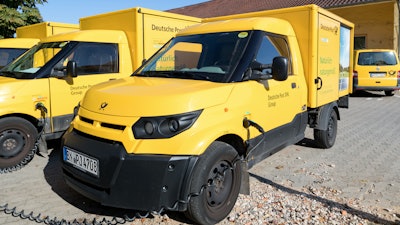
When it comes to adopting electric work trucks for a fleet, it is not just a buy, plug in, charge, and go process. As we examined in previous articles on this topic, there are a number of factors to consider when building and purchasing electric vehicles.
Finding the right OEM partners and designing electric-capable cabs lays the foundation for electric truck building, while vocational upfitting on electric chassis requires careful teamwork to determine the common mission of the stakeholders and the truck’s application. To continue our conversation on implementing electric work trucks, we will explore the importance of a proper charging infrastructure and how it can improve a fleet’s overall efficiency.
Existing Infrastructure
Assessing an operation’s existing infrastructure tells you a lot about its charging requirements (existing capabilities) and the upgrades that may be necessary to achieve electric fleet goals. The number of trucks, type, and their application will all help determine what is needed at the depot for efficient charging. For example, if a fleet has 50 trucks but only 30 are frontline vehicles that are charged daily, it may not be necessary for the fleet to purchase 50 chargers. As long as the 20 backline trucks are in proximity to a charging station, they can share that station with the frontline trucks when they need to be charged.
The size of a fleet’s facility and lot are also factors. If there is limited space for the vehicles, a fleet may require wall-mounted chargers as opposed to floor-mounted, and if the vehicles are parked close together, a dual charger may be a more appropriate choice to reduce the number of chargers needed. From a chassis manufacturing standpoint, the type of charger selected and its location in the depot can even determine where the charging port is positioned on a custom-built truck, as the port must be conveniently within range of the charger. This kind of customization may in turn require alterations to other equipment located on the truck, so everything must be accounted for and properly designed to avoid potential issues with charging and the overall operation of the trucks.
Duty Cycle Determines Charging Profiles
Once a fleet’s infrastructure is mapped out, you can begin to look at the specific charging needs of the electric trucks. Vehicle duty cycles will determine the number of batteries needed for appropriate kilowatt hours (kWh), which will allow the appropriate charging cycle to be created for a given fleet.
While duty cycles may vary among different trucks in a fleet, the specific missions of each truck generally don’t deviate from day to day, so charging profiles can remain consistent and be applied to all vehicles with the same duty cycle. For example, some trucks may average 60 mi. (96.6 km) per day and require 10 hours for charging every other day, while other trucks may average 100 mi. (160.9 km) and need to be charged 8 hours daily.
When you know how often your trucks need to be charged based on their daily mileage, you can coordinate exactly when to charge them with the correct amount of power.
Generally, electric trucks should be operated at no less than 30% SoC, but that figure can vary depending on a truck’s duty cycle and fleet preferences.Marion Body Works
The Charging Sweet Spot
Just because batteries can have a 95% state of charge (SoC) to roughly 20% SoC empty doesn’t mean you should operate within that full range. Think about driving a gas vehicle to and from work. The car still runs as the fuel gauge nears empty and the warning light blinks on, but do you really want to tempt fate, or would you rather fill up at a quarter of a tank to avoid getting stranded?
A general rule of thumb for when to charge electric trucks is at 60-70% DoD (depth of discharge), or with 30% SoC of battery power remaining. However, unlike your gas car, you don’t necessarily have to charge your battery to full power. The key is understanding the battery power range in which the vehicle can complete its duty cycle efficiently. If a truck can perform its duties between 95 and 20% SoC, then you don’t have to spend money on a high-capacity charger to reach 100% in a shorter-than-needed time frame, and the operator will still be able to drive farther than the typical duty cycle if the need arises.
The charging sweet spot can vary depending on battery specifications and fleet preferences. For example, if a fleet manager wants to make the batteries last 20 years, the vehicle may have to operate between 95 and 35% battery power to extend its life.
Ultimately, no matter what is required for battery power, selecting the correct charger will enable fleet operators to hit the sweet spot for their specific needs every time.
Smart Chargers
Another important part of charging infrastructure is equipping a fleet with smart chargers that are programmed to efficiently satisfy the specific charging profiles of the trucks. This means that charging stations can be programmed based on average power consumption, charging rate, best power rates (often off-peak/overnight), and depot time to optimize charging efficiency and load power. If you have a number of trucks all performing the same duty cycle, the charging profile can be applied to all of their chargers.
Smart chargers also help control a fleet’s power consumption by charging vehicles to a predetermined level in a specific timeframe. For example, if a truck requires 10 hours to charge but the available depot time overlaps with your operation’s peak power consumption hours, you can set the charger for a slower charge until peak hours have passed. After peak hours, the charger will begin charging at a faster rate. This allows for the appropriate amount of charging time without wasting energy and money during peak hours.
There are a lot of chargers to choose from, and they come in various sizes. The chargers you purchase should be sized to the specific vehicles of your fleet. Many work trucks may use a level 2 charger, which is roughly 7-15.4 kW+ and larger capacity DC fast chargers (upward of 350 kW). The challenge is matching the chargers to the charging profile of the truck. For example, if you have a truck operating at 105 kW, you don’t need 350 kW charger. You would spend more up front than you need to for a charger that is not used efficiently.
Smart chargers can be specifically programmed to charge electric trucks within a certain duration and to the appropriate power level for consistent charging.Marion Body Works
Charging Away from the Depot
Sometimes operators will need to charge their trucks on the road, regardless of the efficiency of the charging infrastructure. Luckily, there is a large number of charging stations available for commercial use, and new stations are constantly coming online. Keep in mind, however, that these chargers are not smart like those at the depot. They are not programmed for the truck’s specific needs, so they simply pump power into the battery without considering duty cycle and the charging sweet spot.
Avoid Downtime Down the Road
Whether driven by emissions-mandates, the need for cost-savings, minimizing maintenance and downtime, or environmental goals, many fleets are eager to get electric vehicles on the road. However, determining if they have the capacity and resources necessary for a smooth transition is an important step that cannot be overlooked. An electric plan might look good on paper today, but if there is no plan in place for smart charging and charging infrastructure when it comes time to incorporate the new trucks, fleet managers could be faced with a partial solution to fleet adoption, including truck downtime, stranded drivers, and lost revenue.
To avoid these types of potential issues, the stakeholders involved in the initiative must determine what is required for a charging infrastructure and what it must accomplish for a given fleet. Investing the time to address questions including charger type and placement, peak hours, and charging duration may not seem overly important, but it will make a big difference in terms of a smooth conversion to an electric fleet.