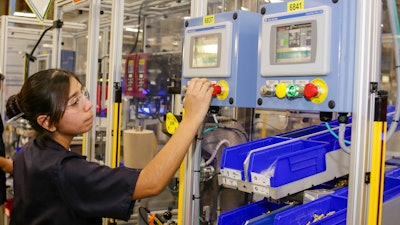
To support increasing customer demand for its high-performing solenoid valves and assembled manifolds, Bendix has doubled manufacturing capabilities of the components through production line expansion and improvement at its Acuña, Mexico, manufacturing campus.
With a $1.5 million investment bridging 2015 and 2016, Bendix added a new low-flow solenoid production line and a new manifold line to its high-tech assembly facilities, increasing capacity as well as offering custom ordering and just-in-time delivery.
Bendix Commercial Vehicle Systems LLC pioneered cutting-edge solenoid development beginning with the North American commercial vehicle market’s first antilock braking system in the 1970s. In 2015, production of the Bendix SMS-9700 Accessory Solenoid Valve and the Bendix FCS-9700 Fan Clutch Solenoid Valve – both manufactured in Acuña – surpassed 1 million units, just three years after their introduction.
Today’s commercial vehicle air systems are busier than ever, helping operate everything from brakes to air bag transfer systems to automated manual transmissions – and high-performing solenoid valves and assembled manifolds are crucial to keeping the air system simplified.
“Modern solenoids are capable of managing more than a dozen pneumatic accessories – we’re talking fifth wheel slide locks, lift axles, air horns, and wheel differential locks, in addition to others,” says Rebecca Carter, Bendix Product Manager – Specialty Valves. “Fleets and original equipment manufacturers are looking to Bendix for custom, advanced, low-flow solenoid solutions to meet a practically limitless range of vehicle needs, and these new lines in Acuña enable us to meet a growing demand with increased flexibility.”
Innovative Components and Advanced Manufacturing
Near the end of 2015, Bendix expanded its existing solenoid production line in Acuña and added a second line to support new customer launches and accommodate increased orders of the Bendix FCS-9700 and Bendix SMS-9700. These solenoids feature a streamlined package design that makes them approximately 30% lighter and 20% smaller than comparable models, allowing for more efficient air systems control by taking up less mounting space and reducing overall vehicle weight. Both are offered in 12or 24V designs, and in Normally Open, Normally Closed, and Latching configurations.
Additionally, the manifold interlocking design of the SMS-9700 enables the valve to be customized for management of as many pneumatic accessories as the OE deems necessary, and its design flexibility with stackable build capability allows body builders to manage their own unique accessory requirements. It can also handle latching solenoid configurations for special situations requiring a vehicle to maintain an accessory’s state during an electrical power loss.
In 2016, Bendix continued its investment in Acuña by expanding its manifold production area, where individual solenoids are combined into the manifolds that manage a vehicle’s air accessories.
“With these additions, Bendix can now produce nearly 1.2 million individual solenoids annually, and more than 350,000 manifolds,” Carter says. “We have essentially doubled our solenoid and manifold operations across the board in terms of manufacturing floor space, equipment, and employees, with no sacrifice to the performance and reliability that our customers expect Bendix to deliver.”
Production of manifolds is designed to meet customer demand for just-in-time delivery and line-sequenced ordering, with up to eight solenoid valves assembled into each manifold, configured to support specific air accessory features.
Among the truck manufacturers equipping Bendix solenoid valves are PACCAR, Volvo, Mack, and Daimler Trucks North America.
High-Tech Home
The solenoid and manifold production improvements further Bendix’s development of the high-tech production capabilities of its Acuña facility, following up on a $4.6 million investment and the October 2016 launch of an advanced driver control module (DCM) assembly line. Other manufacturing operations at the campus include antilock braking systems, air dryers, compressors, actuators, and remanufactured components.
Bendix’s Acuña manufacturing operation was established in 1988 as part of the company’s North American presence in the United States, Mexico, and Canada. The campus’ three state-of-the-art facilities constitute one of Bendix’s fastest-growing manufacturing sites, encompassing 412,000 square feet and employing nearly 1,400 workers.
The Knorr-Bremse Group, Bendix’s parent company, honored the Acuña operation as its top-ranked plant worldwide in 2011, and continues to consider it a model manufacturing facility.