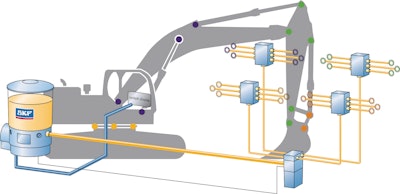
The reliability of off-highway machinery is constantly put to the test, especially in the construction, mining, and similar industries where equipment often must operate in harsh or extreme conditions. Mechanical components are threatened by friction and other elements, which can cause wear or damage, leading to a potential failure. As a first line of defense, proper lubrication of rolling bearings and all the connected points on machinery can help optimize performance, productivity, and longevity in service. How, when, and how much lubricant is applied, however, can become causes for concern.
In the case of lubricating points manually, pitfalls loom. Points can become over- or under-lubricated (unacceptable either way), the application of lubricant may be sporadic or inappropriately timed, and the inaccessibility of lubrication points can become an issue. From there, operations may slide downhill due to premature failure of equipment.
As an alternative to manual lubrication, automatic lube-delivery technologies have been introduced specifically for machinery in the off-highway marketplace. In particular, automatic centralized lubrication systems in different configurations have gained significant ground by enabling the right lubricant to be supplied at the right time and at the right lubrication point -- without manual intervention.
Choosing the right system
The size of a machine, type of required lubricant, number of lubrication points, and other factors will guide initially in choosing the most viable centralized lubrication system for an application. Among the more commonly specified systems that can be evaluated and then specified as appropriate:
• Single-line lubrication systems for semi-fluid grease (typically NLGI grades 000 to 0) are primarily designed for small- to medium-sized construction equipment. Lubricant volumes from 0.01 cc to 2.5 cc are dispensed to the individual lubrication points on each lube pulse. The right amount of lubricant is delivered, regardless of back pressure.
• Dual-line lubrication systems for semi-fluid grease and hard grease (NLGI grades 1 to 2) provide solutions for medium-sized and larger machines with many lubrication points, long lines, and operating in harsh conditions, such as equipment used in the mining industry.
• Progressive lubrication systems for semi-fluid grease and hard grease (NLGI grades 000 to 2) ideally suit construction machinery, such as hydraulic excavators.
For OEMs, such systems can add value and sharpen the competitive edge.
Progressive systems at work
In the construction and other rugged industries, progressive centralized lubrication systems have particularly evolved as highly innovative and practical solutions to feed lubricant from a central source to the points on a machine where friction occurs – while the machine is running. Progressive systems additionally equipped with CAN bus technology represent next-generation solutions to control, deliver, and monitor lubricant in real time.
A progressive centralized lubrication system incorporates a piston pump, main and secondary lines, master and secondary progressive feeders, lines leading to the lube points, and cycle switches (sensors). The overarching purpose is to supply lubrication points continuously with metered lubricant while the machinery is in operation and all the bearings are moving.
In a progressive system, control electronics integrated into the piston pump unit switch the pump on after a preset interval time. The pump then automatically delivers lubricant to the feeders through the main lines for the duration of the contact time. The system’s progressive feeders serve to precisely and consecutively allocate the lubricant delivered by the pump according to a planned ratio and, in this way each lubrication point on the machine receives the exact amount of required lubricant.
Technology innovations in response to application-driven challenges have expanded system performance and potential. In the case of hydraulic excavators, the slewing ring, boom, arm, and bucket must each necessarily be supplied differently with lubricant, depending on the operating conditions, and the lubrication must be divided into multiple independent zones. The conventional path has been to use primary and secondary valves to apportion lubricant volumes for different sections and individual lubrication points.
In a newly developed solution, a 5/4 directional control valve controls the lubricant volume to various areas of the machine. The 5/4 directional control valve features an inlet that can be switched to one of the four outlets at a time, allowing up to four independent zones to be supplied with the proper lubricant when and where needed.
Carrying this technology to the next level, a centralized lubrication system with 5/4 directional control valve can be integrated into a machine’s onboard communication system over CAN bus. This allows separate control and monitoring of the lubrication in each machine section to help prevent unwanted stops, extend service intervals, and increase equipment durability and reliability. The integrated CAN bus control unit allows lubricant quantities to be adjusted to correspond with actual demands -- as little as possible and as much as necessary. This saves lubricant costs and promotes best environmental practices.
Using the CAN bus technology, a single pump unit feeds lubricant from one to four independent zones in the machine. The individual zones are controlled using electronic valves and functional monitoring is performed using cycle switches. These switches, or sensors, have been engineered to detect and signal possible problems immediately and before any lack of lubricant can cause damage to components.
Electronic control and monitoring functions communicate with the machine’s onboard computer to fully integrate lubrication in the onboard service and status monitoring system. Comprehensive system sensor monitoring additionally offers greater operational safety, because even small errors in the lubrication system will be detected early and remedial action can be taken before problems escalate.
Advanced systems will incorporate a malfunction diagnosis memory, which stores information on whether and how long a machine has continued to be operated, despite displayed error notification (such as an empty lubricant container). A log identifies date, time, and type of error. A practical benefit: If equipment is leased, the system’s memory can provide evidence of negligence either in maintenance or during operation (and responsibility for possible subsequent damages can be clearly determined).
In the hydraulic excavator example, all sections (slewing ring, boom, arm, and bucket) will only be lubricated by a CAN bus system to the extent required by the specific operating conditions. When working in water (as one scenario), the arm and bucket would be supplied with two to three times as much lubricant to counteract the conditions. The machine operator simply would tap the respective command on the onboard computer’s display screen.
Installation tips
As general rules of thumb when installing a progressive centralized system for off-highway equipment, these tips can help maximize both performance and reliability in service:
• Installation of the lubricant pump, safety valve, and integrated control unit should be secure and easily accessible on the machinery.
• Lines and feeders in high-risk operating areas of a machine will require additional protection.
Ultimately, the type of equipment will point the way toward the design and specification of an effective automatic centralized lubrication system, and every machine will present its own set of challenges. Hydraulic hammers, for example, require a different lubricant than other lubrication points on an excavator, and they are often disconnected and used on other machines. When a hydraulic hammer fails due to inadequate lubrication, the outcome is always costly in lost time and money. In this context, the best practice will be to equip each hammer with its own compact chisel-paste lubrication system, which remains with the hammer when it is moved from one machine to another.
Regardless of application, when centralized lubrication systems are installed properly consistent with off-highway machinery requirements, benefits will flow. Advantages can include higher operational readiness for the machinery, longer service life for mechanical components, lower costs of maintenance and repair, reduction in unscheduled downtime and risk of failure, and optimized lubricant consumption. Partnering with an experienced developer of lubrication systems can help guide the decision-making and selection process with an eye toward maximizing system performance and potential.
Roberta Reynolds is mobile applications engineer for SKF USA Inc.