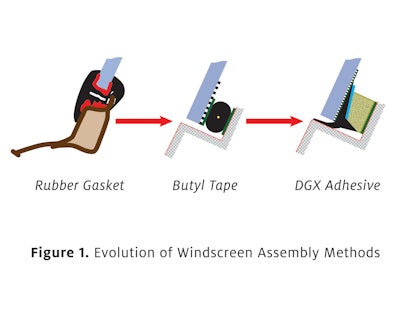
Windscreen bonding and sealing on heavy equipment and specialty vehicles has evolved over the last century. Although traditional rubber mounted gaskets and sticky butyl tapes can still be found in the field on older style tractors and vehicles, liquid adhesives called direct glazing compounds (DGX) are now the method of choice for both original equipment manufacturers (OEMs) and repair and maintenance professionals to fasten stationary windows and windscreens onto vehicle cabs.
DGX adhesives are usually single-component moisture-cure polyurethanes (PUR) that offer superior performance in torsional stiffness, cohesive strength, initial holding strength (also known as green strength) and sealing ability. These materials have improved vehicle aesthetics and safety, lowered manufacturing costs and simplified assembly processes. DGX products eliminate mechanical fastening methods, reduce inventory requirements and costs, improve operator safety and enhance vehicle performance. But as cab designs and manufacturing processes have changed over the years, product development and design engineers have demanded faster, safer, more consistent and convenient adhesive solutions.
Despite their many advantages for bonding windscreens, traditional PUR-based DGX compounds have significant limitations that restrict their use in vehicle assembly processes. To ensure good adhesion to glass, plastic and paint, DGX adhesives rely upon solvent-based glass and paint primers that add steps to the assembly process and contain hazardous isocyanates, affecting worker safety. Since the adhesive itself requires ambient humidity to cure, cure times can vary greatly depending on temperature and humidity levels in the manufacturing environment, causing potential bottle necks in vehicle assembly processes.
Recent advances in primerless windscreen adhesives and booster technology have minimized these limitations and helped vehicle manufactures increase line speeds, reduce work in process, eliminate hazardous solvent-based primers and climate control chambers and implement a more consistent and controlled assembly process.
Windscreen assembly methods using traditional DGX adhesives
Fastening a windscreen onto a vehicle using DGX technology is much more complicated than attaching a sheet of glass on a painted cab using a gasket or adhesive tape. There is a critical scientific process involved in properly selecting, specifying and applying direct glazing adhesives.
Since the 1960s, manufacturers and repair professionals have followed the same time-honored assembly steps to install windscreens on heavy equipment and specialty vehicles. Typical windscreens are made of either float, laminated or tempered glass or a plastic material like polycarbonate. In the bond line area, the windscreen usually includes some type of ceramic frit coating that is applied and cured by the glass supplier. The frit coating improves adhesion, protects the adhesive from damaging UV radiation, and provides an aesthetically-pleasing finish. The base structure of the cab is usually treated steel coated with some type of cured paint system (Figure 2).
In order for a traditional one-part, isocyanate-based PUR DGX product to achieve good adhesion to glass, plastic or painted metal, manufacturers should apply solvent/isocyanate-based glass and paint primers to each substrate and allow them to cure prior to applying the adhesive. Primer dry times vary based on room conditions and solvent type, concentration and base chemistry, but typically require 10 to 15 minutes to dry.
Once the primers are dry, application of the DGX adhesive can be completed either manually or automatically/robotically using a cartridge or bulk equipment dispenser. As most products are too thick to dispense at room temperature, they must be preheated up to 60 C, a process that will also increase the cure speed of the adhesive. Once assembled, most manufacturers will apply tape and/or clamps to hold the glass in place during cure.
Traditional one-part PUR DGX products cure from the outside inward upon exposure to moisture in the surrounding air. As shown in Figure 3, their drive-away—the time it takes for a windscreen to survive a 30 mph frontal crash according to FMVSS 208—will vary based on the room’s temperature and humidity. Depending on gap size (typically between 3 to 6 mm), drive-away time can range from less than one hour to several hours or days. Full cure/strength can take two weeks or more to develop depending on the climate. Some manufacturers will store their bonded cab assemblies in a humidity oven to accelerate cure time, increase process control and improve cycle time and capacity. Use of humidity ovens can be quite expensive and require a substantial amount of floor space.
Windscreen bonding methods with primerless DGX adhesives
Primerless DGX products can either be PUR-based or silyl modified polymer (SMP)-based. SMPs are less common as they tend to be more expensive and have lower tensile strength/torsional stiffness than PUR-based products.
The process methodology and reaction chemistry of primerless DGX products is basically the same as that of traditional PUR DGX products with one important exception. Primerless DGX products feature adhesion promoters that relax the requirement for secondary primers on base substrates. With primerless DGX products, the two primer layers illustrated in Figure 2 can be eliminated from the assembly process.
While primerless DGX products are typically more expensive than traditional PUR products, they can reduce the total cost of the overall windscreen assembly process by eliminating material costs for primers and disposable primer applicator swabs, and time and manpower spent applying and drying primers. Primerless products also eliminate the significant potential cost of operator sensitization to solvents and isocyanates. All these factors add up, especially if the operator improperly applies primer prior to using a traditional DGX, a situation that could result in a disastrous field failure of the windscreen.
Primerless products will not provide higher strength bonds than traditional DGX products and, on some substrates, may not provide sufficient strength without use of a primer. While they may not be a cost effective option for all applications, primerless DGXs should always be considered when selecting the right adhesive for windscreen bonding.
Boosted windscreen bonding systems
Because cure of one-part DGX systems and primerless systems rely on ambient moisture, cure times in non-climate-controlled facilities can vary significantly depending on the time of day, the season, and the geographic location of the facility. Typical drive-away times reported by DGX manufacturers of between 15 minutes and four hours is only enough time for a thin skin to form on the exposed ends of the adhesive bead at 22 C and 50% RH.
This cure rate and skin formation time vary significantly as the humidity and/or temperature changes, factors that control the water content in the air as illustrated in Figure 5. It can take days or even weeks for the adhesive to cure through to the middle of an inch-wide bead at an average rate of only 3 to 4 mm per day depending on the gap.
With a boosted or accelerated DGX adhesive system, a static mix nozzle is used to mix a moisture-containing paste, the booster, into the bulk adhesive. This booster allows the adhesive to cure rapidly and homogenously through the bond line independent of surrounding humidity conditions, even in dry climates.
Booster materials are compatible with most one-part PUR-based DGX adhesives including primerless DGX products, and are formulated so that only a small concentration, 1 to 3% by volume, is needed to achieve very fast cure as shown in Figure 4. Most adhesive systems achieve drive-away conditions in 15 minutes or less. While some cartridge formats of boosted DGX systems are available for repair applications in the field, these materials are typically applied using bulk equipment capable of metering very thick materials at very wide mix ratios. The capital expense of such equipment can range from $50 to $100 thousand, making production rates and cycle times critical factors in the cost analysis.
Selecting and qualifying value-added DGX alternatives
When selecting a DGX adhesive, manufacturers must remember that windscreen bonding is not a simple gasketing/sealing or even bonding application, but a combination of the two referred to as elastic bonding. OEMs are now relying on the adhesive to seal and bond the joint between the windscreen and cab structure while providing structural integrity and vibration resistance/dampening.
Because of this, many variables are involved when selecting and specifying the right DGX system for a given windscreen application. By consulting the adhesive supplier’s application engineers and asking them to design an appropriate test matrix, manufacturers can easily validate the suitability of a new adhesive for a specific windscreen assembly application.
Some considerations when selecting a DGX adhesive include production rates, cycle times, drive-away times, substrate types, plant/storage conditions, bond line gap/width, joint design, capital budget, plant regulations, adhesive bulk properties and adhesive performance.
Bulk properties of the cured adhesive including durometer, elongation and tensile strength, are as important to the application’s success as adhesion to the bonded substrates under heavy torsional strain, constant vibration and potential extreme climate changes like UV light exposure and fluctuations in humidity and temperature. Premature failure of the bond or substrate can be caused by DGX materials that are too stiff and hard or too flexible and soft.
The adhesive’s rheology is also very important to windscreen assembly. A thin material can sag, requiring gap spacers or other fixturing during cure, while an excessively thick material may require powerful pumps and/or heat to dispense and high compressive forces while mating the windscreen to the cab.
The temperature and humidity in the assembly area and the manufacturer’s desired cycle/drive-away times can affect adhesive selection and assembly process controls. Substrates to be bonded are also very critical in adhesive selection as certain adhesives and primers are specifically engineered for use on ceramic fritted glass, glass, metal, plastic or paint. To complicate things even further, the type of glass, metal, paint or frit and how it is applied, treated or cured can also affect the long term adhesion of DGX products. The best answer is to test adhesion on several lots of substrates.
Primerless and boosted DGX adhesive systems can be very effective alternative cost savings solutions for many windscreen bonding applications. But traditional DGX adhesives still have their place in the industry, especially where production volume does not justify the capital expended for booster equipment or where primerless products cannot achieve sufficient adhesion without primer. Adhesive suppliers can provide critical information and engineering support on traditional, primerless and boosted DGX adhesive solutions and can assist in the adhesive selection process.