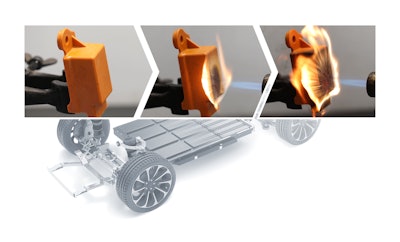
Freudenberg Sealing Technologies is offering a new class of materials aimed at improving fire protection in electric vehicle drives. The material, Quantix ULTRA, resists melting, even at extreme temperatures of up to 2,192 degrees Fahrenheit. The first series application is now underway as a flame protection barrier for cooling system parts in an electric car’s lithium-ion battery. Some advantages of the new material include:
- Processing the material in injection molding is both versatile and economical
- Lower density compared to metallic materials
According to the company:
Electric cars with lithium-ion batteries have a range that is suitable for everyday use and require a high degree of safety. Various safety measures are being implemented to make sure that any thermal runaway of the battery is prevented or delayed. So far, plastic components used for this purpose have generally failed to meet the automotive industry’s strict test standards for electric drives. This is different with Quantix ULTRA from Freudenberg Sealing Technologies: The new material class can withstand very high temperatures. It does not melt or ignite. In laboratory tests, a two-millimeter-thick material sample can even resist an applied flame with a temperature of 1,200 degrees Celsius for over 25 minutes.
Further tests simulate the emission of hot particles under high pressure, which can occur if the gases in battery cells are abruptly discharged. Quantix ULTRA withstands the stress test for 20 seconds. A two-millimeter-thick aluminum sample only takes two or three seconds to be destroyed.
Freudenberg Sealing Technologies uses this innovative material to produce flame protection barriers for the cooling system of lithium-ion batteries, for example. As of February 2024, these will be used for the first time by a car manufacturer in series production vehicles.
Quantix ULTRA is suitable for all applications with high requirements for fire protection and lightweight construction. Moreover, it is not limited to specific geometric shapes. The material can be processed into films, for example, to be implemented in battery-electric drives. Other areas of use include enclosures for power supply units, media-carrying lines, cable insulation, battery housing covers and components for electric motors.