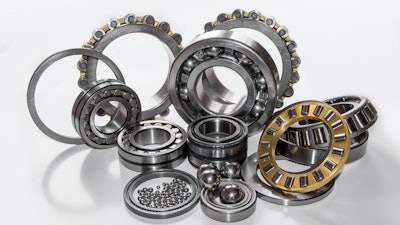
If a design engineer wanted to choose any four bearing components from a group of 20 design options, the possible number of combinations would be a whopping 4,845. Suddenly, choice overload stunts any kind of decision-making process, when purchasing bearings.
Chris Johnson, Managing Director at specialist bearing supplier SMB Bearings, explains how to navigate the seemingly endless choices in the bearing design process.
An exploded view of a standard bearing clearly shows its main physical components: the closure, the inner and outer raceway, the balls and the optional retainer. But with four important physical design decisions to make and an increasing number of innovative possibilities, how do design engineers choose the best options for their application?
The best place to start is to consider the environment and specific conditions the bearing will be operating in. A bearing’s inner and outer raceway, balls, retainer and closures may be fabricated from different materials, yet must function effectively in unison. For example, a food and beverage grade bearing may have acetal resin (POM-C) rings, a nylon (PA66) retainer, balls made from 316 stainless steel or glass and a contact seal consisting of nitrile/BUNA-N rubber bonded to a metal washer. This combination would provide good contamination protection and corrosion resistance.
Are retainers necessary?
Often a crucial feature in bearing design, retainer options are often an afterthought when purchasing bearings. But they shouldn’t be. Retainers or cages perform a fundamental job. They are designed to keep the balls evenly spaced around the raceway and help retain grease around these elements.
They aren’t always required though. Bearings without a retainer have more balls and are called full complement bearings. This increased number of balls allows these bearings to withstand heavier loads and cope with impact or shock, as the load can be distributed more evenly around the raceway. However, full complement bearings experience additional friction and are generally not suitable for high speed applications or axial loads. Once the more popular design option, full complement bearings are now less common thanks to the advancements in steel technology.
Choosing your retainer
Metal retainers are the most common type and suit most applications. They can be manufactured from carbon steel or stainless steel and come in either a crown or ribbon form. A riveted steel ribbon retainer should be used for high vibration applications due to its greater strength. Crown metal cages are used primarily on smaller miniature bearings and thin-section bearings, where space is more limited. Whereas a crown type is guided by the inner ring, a ribbon type retainer is mainly ball guided.
Certain applications, such as MRI scanners, where non-magnetic properties are required, call for an entirely non-metal bearing with a non-metal retainer. While these may be more costly, non-metal retainers are often necessary and can increase a bearing’s lifespan in the long run.
Applications where retainer selection must be carefully considered are those involving temperature extremes. A nylon or polyethylene retainer will not cope with temperatures above 100-120 C. In applications that exceed these temperatures, the retainer will lose strength and lead to early bearing failure. A stainless-steel retainer can be used up to 300 C and will equally maintain its strength under -40 C as will PEEK and PTFE retainers. At extremely low temperatures, a nylon or polyethylene retainer will not perform well and will become brittle so 316 stainless steel and PTFE are favored.
Similarly, a nylon or polyethylene retainer will be affected by certain chemicals and corrosive environments. These materials will cope better than stainless steel with some chemicals, but not as well with others, so this must be assessed on an individual basis. These synthetic retainers do however offer better resistance to water and salt water than stainless steel retainers, making them the best choice in marine environments.
Polyether ether ketone (PEEK) and polytetrafluorethylene (PTFE) retainers are often used in corrosion resistant bearings used in aggressive environments as these materials are highly corrosion resistant. This is an essential consideration for bearings in chemical or pharmaceutical environments.
Reinforced nylon retainers have good sliding characteristics and will cope better than metal retainers at very high speeds. They also produce fewer fluctuations in running torque and can increase maximum speeds by up to 60%.
In many instances, retainer material choice will be led by the raceway material choice. To prevent non-useful friction, increased wear and premature equipment failure, it is important that the bearing retainer doesn’t have too much radial movement, so it needs to be guided by either the balls or one of the rings. Plastic bearings usually have nylon retainers and full ceramic bearings normally have PEEK retainers, PTFE retainers or have no retainer at all.
While having 4,845 design options may initially seem like an impossible number, by asking the right questions and considering your environmental conditions carefully, it quickly becomes manageable to eliminate unsuitable design combinations and deduce the best matches for each individual bearing design.