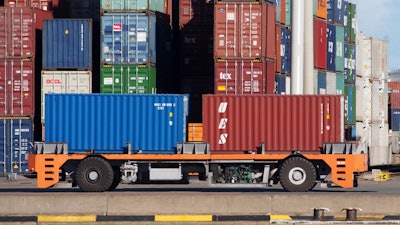
As world leader in the manufacture and supply of wheels to the container-handling sector, GKN Wheels & Structures has been supplying container-handling equipment manufacturers and operators worldwide for more than 30 years and is recognized for the quality, reliability and performance of its wheel solutions. Now, following major advances in its manufacturing technology, the company’s product range for this sector has been enhanced, with the company’s latest wheels delivering a number of significant benefits for the original equipment manufacturer, operator and maintainer.
This new approach, with the wheels manufactured through a hot induction forming (HIF) process, has enabled GKN’s engineers to produce wheels specifically for automated guided vehicles (AGVs), which are 50% stronger and have a lifespan 50% longer than conventionally manufactured, multi-piece wheels.
The process achieves greater manufacturing accuracy, allowing material to be placed where it is needed (and taken out where it is not), leading to an increase in rim strength. And with all contact areas machined at the end of the process, a 100% round wheel with perfect stress distribution is guaranteed. The process also means that the contact points between the wheel and tire are perfectly smooth, with the rim design featuring extended flanges to further protect the tire.
John Madsen, GKN Wheels & Structures Director of Engineering, says, “This wheel delivers outstanding performance, with its special design having been developed to meet the very exacting requirements of one of the most demanding commercial environments. As part of the development process, we subjected the wheel to rigorous testing, both off-site and on-site, with the AGV operating laden and unladen over extensive periods of time.
“Capable of withstanding high loads and with improved life expectancy, we believe the wheel is a great solution for container ports worldwide, with its benefits translating directly into increased durability and therefore vehicle up-time.”
Given the harsh coastal environment that AGVs operate in, the company’s engineers also paid close attention to the surface of the wheel, with each product finished with a powder coat surface finish, applied through an electro-coat process to guarantee complete coverage of every part of the surface.
Madsen continues, “These AGVs operate under extremely heavy load conditions in a people-free environment, with each vehicle’s movements fully integrated into a carefully choreographed program which is designed to maximize efficiency and reduce vessel turn-around times to a minimum. We have already supplied wheels to AVGs operating in the Port of Rotterdam and have been delighted with their performance.”
The Port of Rotterdam is Europe’s largest and most dynamic sea port and one of the earliest ports to introduce AGVs. Handling over 460 million tonnes of freight and nearly 130,000 vessel movements a year, the port sets the benchmark for the design and operation of deep-sea freight terminals and at its heart is a fleet of 300 AGVs. The vehicles operate 24 hours a day, 7 days a week to keep the port operating smoothly and efficiently, moving freight containers between ships and the maze of storage areas.
“Given such a demanding operating environment, a vehicle breakdown of any description can severely affect both operational and financial performance,” says Madsen, “but with tire-pressures of 10 bar, a failure of the wheel or tire could have catastrophic consequences. We have developed a product that not only delivers technically, but also provides a reassurance of quality and safety, major considerations when the consequences of failure are so severe.”