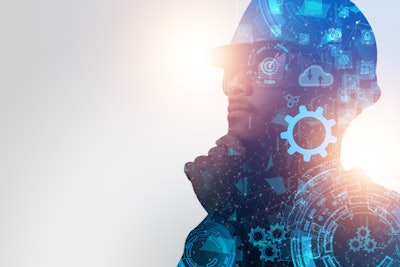
As mobile hydraulics continues its transition to electrification, companies are asking about and investing in connected machines that provide valuable, real-time performance data.
To address questions on the topic, OEM Off-Highway sat down with Dr. Enrique Busquets (EB), engineering director at Bosch Rexroth. Busquets is the mobile hydraulics engineering director responsible for regional product and business development for electronics, software, telematics and electrification at Bosch Rexroth North America.
He holds a bachelor’s degree from the University of Texas at El Paso and both a master’s and doctorate degree in mechanical engineering from Purdue University — with emphasis on hydraulic and electronic controls.
Read on for his key insights into market trends and learn what today’s executives need to consider when evaluating this evolving technology.
As operators & executives consider investing in electric solutions, what role should connectivity play in the decision?
EB: Connectivity plays a crucial role in monitoring all systems. With the advent of electrics, this becomes even more important for additional layers of safety and control. Moreover, the implementation of electric systems in off-highway equipment eliminates all barriers for automation, which is fully complemented by connectivity. Connectivity should be viewed as a lens through which all machines can be seen and with which more value can be added for the end user.
How can companies incorporate real-time data in their connected solutions?
EB: The use of real-time data is already incorporated into the daily usage of machines in the field. The difference is whether this real-time data is used on the edge or transmitted to a remote location to either add value or make on-the-fly decisions. One of the biggest benefits of our platform is that it allows you to do both and manage the electronic resources freely to optimize each component’s bandwidth.
What role does automation play in mobile hydraulics? How are managers are monitoring these solutions remotely?
EB: Automation has been in mobile hydraulics for many years. From mining to agriculture, automated machine solutions have provided a significant amount of value in not only optimizing costs, but entire fleet operations. The challenge is for automation to become more versatile to address the unstructured nature of the environments in which mobile equipment operates. However, we already see several use cases in the field where automation is starting to push the boundaries. For instance, solar filed panel installations have gone autonomous in areas where the sites are remote. In this example, the combination of autonomy and remote monitoring is a key for the success of the entire operation.
What has been the learning curve or shift in training for operators with electric machines?
EB: This is still yet to be seen. Different from automotive, mobile applications are usually designed to meet a set of criteria that matches the work to be accomplished. In such cases, the advantages of electrics will become apparent on a case-by-case level, where each application will find the instantaneous torque capability of electric motors, or the higher efficiency and productivity of those systems advantages at different levels. One aspect that will certainly be an instant impact is the lower serviceable systems and therefore service costs.
How has connectivity improved maintenance & addressed issues faster?
EB: Connectivity in the field usually leads to faster or even remote debugging of errors or service claims. In mobile applications, the complexity of service providers and the inconvenience of a fleet being at a standstill, not to mention the sometimes-exorbitant costs behind such scenarios, makes connectivity a no-brainer. In many mobile applications, we experience small OEMs that do not have a network of dealers or service providers, which are forced to fly personnel all over the country to address field issues. Connectivity will not entirely resolve these issues, but it addresses a portion of them and facilitates service by knowing in advance what is wrong with a particular piece of equipment.
What’s the right balance of implementing hardware, software & the internet to manage mobile machines?
EB: For the field of mobile applications, there is no one-size-fits-all, nor a magic number. Differing again from automotive, mobile applications are extremely diverse. Experience has shown us that anything related to the operator assistance or controls should be handled at the machine level to avoid disruptions by poor network or lack of infrastructure. And any decisions that have to do with a fleet, or decisions that can be implemented over the course of the machine operation, can be moved to the cloud.
Is performance impacted in remote locations where internet capabilities are limited?
EB: Yes, clearly. In some instances, portable devices that provide satellite connection or personal hotspots can alleviate these issues. In other areas, some providers, such as Starlink, will address the challenges of connecting even in the most remote areas.
How will IoT continue to evolve with the increased adoption of electric machinery?
EB: The benefits of connecting a machine have been in several instances proven with numerous use-cases. Machines which have been electrified, or that are primarily electronically controlled, are the best candidates to fulfill these use-cases and add value to the OEMs or end users. Therefore, we at Bosch Rexroth believe that the vast majority of mobile electrified equipment will be as well connected.
___________________________________________________________________________________________
Kathy Wells is editor of OEM Off-Highway magazine.