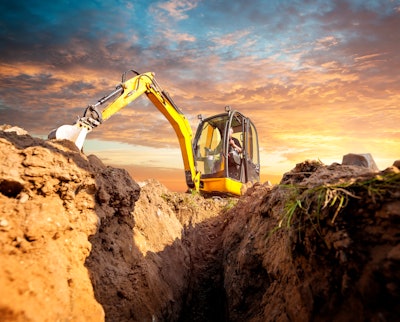
The movement toward electrification of construction equipment — once just a concept — is now occurring at a rapid pace. Stricter emissions regulations in the U.S., Europe and China, an increasing number of municipal noise ordinances, and the higher cost of diesel fuel are driving increased demand for electric construction equipment.
In addition, advances in battery electric vehicle (BEV) technology are making electric construction vehicles, especially small equipment such as small loaders and excavators, less costly to produce and more attractive to end users. Lithium-ion battery technology has allowed small construction vehicles to achieve a full day of work on a single charge, and in some cases, two full days of work. And, thanks, in part, to the lower maintenance costs associated with electrified construction equipment, owners are now able to quickly recover their investments.
The increased demand and improved technologies suggest there will be strong growth in the battery-electric and hybrid-electric off-highway equipment market for the next five to 10 years. In fact, according to MarketsandMarkets, the electric construction equipment market is forecast to grow to $24.8 billion by 2027 at a compound annual growth rate of 22%.
For OEMs, it means the race is on to capture market share. And, for design engineers, it means there is enormous time-to-market pressure. At the same time, equipment electrification presents several new design challenges that have caused delays for many manufacturers.
But are these design delays avoidable? Initially, design delays may have been inescapable due to factors outside of a design engineer’s control, such as a lag in available high-voltage (HV) circuit protection and power distribution products. However, solutions to the unique design challenges of electrifying construction equipment are becoming more readily available through partnerships with suppliers that have been able to adapt to market trends and have system-level knowledge and testing capabilities.
What’s Slowing the Design Process for Electric Construction Vehicles?
There have been a couple of factors leading to slower electric construction equipment designs. To begin with, many design engineers have not had experience with some of the special problems and requirements that come with vehicle electrification, such as the increased risk of levitation in HV DC contactor relays or the subsequent need for coordinated circuit protection.
Levitation in DC contactors can occur during an overcurrent condition when the magnetic field created by the current is so strong that it pushes the moving contact away from the stationary contact. The resulting arcing and chattering can damage the contactor to the point of catastrophic failure. Figure 2. Manufacturers are expanding their lines to suit higher voltage applications, such as the new Littelfuse contactors shown here.Littelfuse Commercial Vehicle Products
This unsafe event is a consequence of the application current going beyond the specification for the relay. This means design engineers need to know the level of current that may cause levitation and make sure the circuit will open before the current reaches that point by specifying upstream circuit protection that will operate fast enough to prevent levitation in the contactor.
Levitation is just one example of how emerging BEV technology, which has increased working voltages and currents, is presenting designers with new challenges. High-voltage DC is more dangerous and harder to interrupt, requiring innovative solutions to distribute, control, and protect application power.
Making the situation more difficult for design engineers is the fact that there are currently no standards for HV fuses or contactors used in construction equipment. And ISO and SAE processes can take three to five years to complete, so the standards simply are not going to come as quickly as they are needed.
When it comes to the electrification of construction vehicles, the lack of standards, as well as a lag in available vehicle-rated HV DC products, has created a “Wild West” scenario. Under these conditions, designers have resorted to practices that have resulted in increased testing times and slower design processes altogether, including:
- Using industrial fuses when HV automotive fuses are not available — While, at first glance, it seems like a reasonable substitution because industrial fuses meet voltage and current specification requirements, the lack of vibration testing for these fuses means no one knows how long they will last.
- Over-specifying and under-specifying — Using overrated parts is a cost drain, and using parts that are rated too low is a potential safety issue. Using low-voltage fuses in HV systems, for example, can lead to dangerous thermal events.
- Matching fuses with contactors without knowing what will happen — Because of the risk of levitation in HV DC contactors, in some cases, pyrotechnic safety modules (PSMs) may be a better choice than a standard fuse. In other cases, PSMs may be too costly. Ideally, circuit protection should be coordinated with a relay and tested to ensure a balance between nuisance tripping and excessive contact arcing.
While the standards for HV systems will eventually catch up with the industry, and the lag in available products to support electrification is beginning to dissipate, OEMs looking to capture market share will only see success if they prioritize quality and functionality. High-performance designs that win the approval and loyalty of customers beat out rushed products with major design flaws every time.
Partnering With Suppliers Speeds Time to Market & Enables High-Performance Design
One phenomenon that is beginning to arise out of the chaos is: In order to avoid delays and costly mistakes, OEMs are partnering with suppliers that have expertise in both high-voltage and automotive applications. Suppliers with system-level knowledge can help OEMs address the challenges of electrification, help them address the special problems of HV DC efficiently, and accelerate time to market by assisting with testing.
Suppliers that have been able to adapt to market trends can offer design engineers more than products that enable electrification. They can offer expertise, customizable solutions and testing capabilities that speed up the design process.
OEMs looking to partner with a supplier on the electrification of construction equipment may also want to consider suppliers that sit on the ISO and SAE committees. These suppliers will have the added advantage of being able to anticipate what the standards will be in the future — making it far easier to stay ahead of what is coming, saving both time and money.
___________________________________________________
Geoff Schwartz is the business development manager at Littelfuse Commercial Vehicle Products.