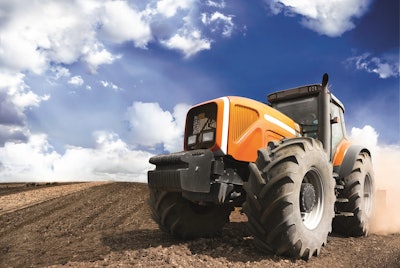
Operating off-highway vehicles has always presented unique challenges. These vehicles are required to deliver consistent performance under extremely harsh conditions. Electrical connectors, sensors, high-speed data connectors, power relays and switches must confront these adversities as part of the equipment system. Downtime resulting from electrical issues triggered by extreme temperatures, excessive dirt, dust, moisture, salt and intense vibrations, is simply not acceptable.
Yet, compounding the existing difficulties, an entirely new set of requirements and challenges have emerged. Over the past several years even more pressure has been applied to manufacturers of off-highway vehicles. They must now address evolving safety mandates and environmental regulations, overcome economic pressures to improve efficiency and productivity, meet customer demands for new features and functionality, and adapt to entirely new technologies and architectures — such as the transition from internal combustion engines to complex electric powertrains.
While these new pressures and requirements are diverse, they have one thing in common: performance and reliability have been amplified at all component levels of the equipment.
New Components Amplify the Need for Reliability
As vehicles adapt to meet these evolving demands, new components and technologies are also creating new potential points of failure. For example, off-highway vehicles are now using more sensors than ever to measure humidity, temperature, pressure, rain, fluid and oil quality. All of which either monitor external operating conditions or internal system performance. These sensors help ensure reliable performance of the machine and drive preventative maintenance to reduce downtime.
Similarly, operators are increasingly dependent on newly integrated high-speed data-enabled functions. They have proven to provide a major boost to productivity through powering adaptive braking and steering, onboard diagnostics, vehicle-to-vehicle (V2V) and vehicle-to-infrastructure (V2I) communication, cameras that provide a 360-degree view of their environment and more.
This functionality is enabling them to accomplish daily tasks more efficiently, effectively, and safely. Here again, it all relies on a handful of critical high-speed connection components that allow this communication to perform reliably in the harsh commercial environment of an off-highway vehicle.
For example, off-highway vehicle manufacturers have evolved from CAN bus to Ethernet architectures to support high-speed data transfer at rates of up to 50 gigabits a second and above. These include sealed, single-pair Ethernet connectors can transmit data from 100 Mbps to 1 Gbps and extend beyond 15-meter channel lengths to reach 40 meters while maintaining excellent signal integrity. This allows them to be used for valuable new applications that require additional cameras, sensors, enhanced network architectures, increased information and displays, and large-bandwidth backbones.
In the landscape of rapidly advancing technology, the stakes are higher than ever before. If even one of these devices fails, the negative impacts can be significant. Strict completion deadlines in construction, seasonal yield targets in agriculture, and time-sensitive operations in commercial transportation all hinge on the seamless functioning of these pieces of equipment. TE Connectivity
When equipment goes down, operators face losses including repair fees, sunk labor costs and forgone revenues until normal operations are restored. For example, it’s estimated that mining equipment downtime costs $3,000 per hour due to lost production, with an average of 60 hours of downtime created per incident for a total of $180,000.
The considerations extend beyond economic factors; health and safety also take center stage. The elevated performance requirements, particularly in the realm of new electric vehicles, necessitate high power and voltage, amplifying the potential threat not only to the vehicle but also to its operator in the event of any failure. This risk is particularly acute in the absence of dependable battery disconnects, power relays, or emergency stop switches that offer reliability and contribute to technician safety.
Moreover, battery disconnect switches should incorporate lockout, tag-out features to ensure that currents are safely disengaged before technicians commence maintenance and repair activities. Solutions explicitly designed with lockout, tag-out capabilities act as a protective measure for workers, enhancing overall safety in the operational environment.
Collaboration & Innovation Is Making a Difference
Together, component manufacturers and OEMs are rising to meet the need for increased vehicle performance, safety and sustainability. With the ever-increasing complexity in the industry, OEM engineers will want to do more than simply source solutions and consider harnessing their partner’s expertise and closely collaborate to drive innovation further and faster than before. By doing so, OEMs, component manufacturers and operators can rest assured that they’re working with electrical components that won’t quit as they execute challenging duties in the field.
Jon C. Harman is the global vice president of sales and customer care at TE Connectivity. Visit te.com.