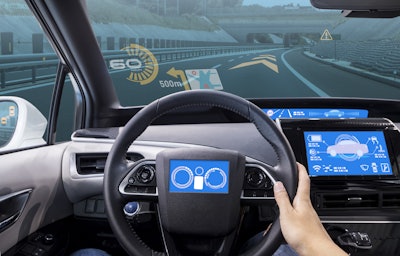
This article is sponsored by STW Technic, LP.
If you've driven a passenger vehicle made within the last decade, chances are you've utilized some form of artificial intelligence (AI) technology on the road. Parking assist, lane detection and adaptive cruise control are just some of the AI-enabled features that provide drivers with increased efficiency and safety.
The automotive industry has long been leveraging AI and machine learning technologies. Fleet managers of on-highway vehicles — those in the transit, logistics and service sectors — are currently taking advantage of the latest automotive technologies to reduce vehicle-related costs and mitigate safety risks.
Additionally, the off-highway construction industry can benefit from the automotive industry's application of intelligent solutions as well. While original equipment manufacturers (OEMs) continue to make strides in the development of new intelligent solutions for heavy machines, advancements have come at a slower pace. This is largely due to the vast range of complexities and differences each construction jobsite experiences. However, the automotive industry can serve as an informative example.
Here are several ways the construction industry can leverage intelligent solutions to mitigate safety risks and optimize operations.
Mitigating Safety Risks With Optimized Visibility
The operator in the cab needs all the tools possible to create a full picture of the machine's surroundings. Heavy equipment, being as large as it is, inherently comes with blind spots.
Operators must be vigilant to maintain awareness and visibility of fellow crew members working on the ground around their machine, as well as other equipment and materials in proximity. To aid operators, most equipment will be outfitted with traditional side and rearview mirrors to aid in this and often additional cameras.
Some OEMs now offer multicamera systems to provide a full 360-degree view around the machine. Such systems utilize a camera on each side of the vehicle and stitch the images together with software to create this view. As most equipment operates in environments with the potential for hazards on all sides, operators must be able to see clearly around their machinery at all times.
But all those cameras are virtually useless without a destination to send their output. Devices like inSIGHT Displays support up to four camera feeds for precisely this purpose. Easy access to camera output, as well as informative alerts that immediately notify operators about system irregularities are crucial to machine safety — preventing costly accidents.
The Potential of Sensors & Object Recognition
Equipment camera systems can be further supplemented with proximity sensors that utilize a combination of cameras, radar and/or ultrasonic technology. Such technology, which has become commonplace in the automotive industry, can alert the operator if the machine moves within several feet of another machine, object or person.
While such alerts can be helpful, said Clayton Dean, senior electrical engineer collision avoidance systems, Rosco Vision, sensors that rely on radar will generate false positives. These are alerts of nearby objects that don't pose an obstacle to the vehicle, such as a pedestrian warning initiated for a nearby fire hydrant.
This is where AI can be helpful, according to Dean, who works primarily with on-highway transit markets.
"There are some advanced radar systems where they're getting more intelligent," he said. "They can start to do something similar to object recognition."
In the automotive industry, object recognition primarily involves the detection of pedestrians and other vehicles, though, in more recent years, AI is also being used to identify speed limit signs, traffic signs and streetlights. Dean anticipates the detection of moving personnel or vehicles will be most beneficial for construction.
However, construction worksites and applications may be too complex for AI as it exists today.
“When you're in a car, there's only a finite number of things you can do, right? You go forward, you go back, you stop, you go, you turn left, you turn right, change lanes,” said John Somers, vice president, construction and utility sector at Association of Equipment Manufacturers (AEM).
Implementing object recognition will be more challenging for construction. Not only may there be a multitude of operations a machine must do, but there is often infinite moving pieces around the machine. Moreover, the applications and environments can vastly differ from worksite to worksite.
“I think this is absolutely something that's coming to construction,” said Somers. “I just don't think it's going to be as straightforward as it was with automotive.”
As sensor and object recognition technology must progress for construction worksites, Sara Feuling, PE, senior director of construction at AEM, insists a variety of tools is necessary for construction sites today.
"Putting all those pieces together, using that mirror, using the sensors, using the camera where you don't have access to a mirror, will very much help remedy some of those visibility issues and blind spots," she said.
Optimizing Operations Through Machine Learning
Many in the automotive and construction industries would agree one of resources becoming increasingly vital for business growth is data. Through machine learning, data becomes more and more valuable to the business owner, who can use analytics to identify and reduce inefficiencies, cut costs and more.
In construction, machine-generated data is not new. OEMs, dealers, technicians and construction firms alike have been able to learn about their machine through telematics since the late 20th century.
"Back then it was just, where's my equipment?" Somers said. "And then the data evolves, the sensors and the machine evolve, and those will probably continue to evolve for the rest of our lives."
Data insights typically offer two major potential benefits:
- Prescriptive maintenance — Most equipment OEMs offer telematics packages that include remote diagnostic troubleshooting, primarily through fault codes informing fleet managers or technicians when and how to react to a situation. “With some telematics systems, your machine could send an alert message in essentially real time to the fleet manager,” said Somers. “So, they could tell their operator to shut the machine down or take steps to make sure something bad doesn't happen.”
- Predictive or proactive problem solving — With the advancement of AI, some industries are already enjoying predictive analytics that allow them to make projections and devise strategies to optimize vehicle performance for maximum efficiency. For example, a contractor monitoring the speed operators are driving may think driving faster will be the most efficient course of action. However, complete data insights may help them forecast that driving faster may put more wear on their tires and ultimately cost them more.
“The more data that's coming in, the easier it gets to transition into that predictive space,” said Somers, who expects construction is “on the fridge of this.”
Maximize Your ROI With Machine Learning
While technology has evolved, according to Somers, the construction industry’s awareness and adoption of the technology has lagged. For example, ISO only started to put a framework in place for intelligent transport systems to provide end users with data in 2017, decades after telematics became available.
“Adoption of data insights is not to the level that I think it can be. You got some contractors and dealers that have been doing this for years and you have some that aren't,” said Somers. “I think we can always do better.”
Whether equipment OEM, dealer/technician or end user, Somers believes machine learning can deliver a worthwhile ROI. Here are three examples:
- OEM — Build a better machine. If a certain machine in the lineup experiences more performance issues, the engineering team can utilize and monitor data to determine necessary improvements for a future model.
- Dealers and their technicians — Avoid unscheduled downtime. While monitoring a customer’s equipment, predictive insights can show technicians when to anticipate brake replacements. They can then schedule the maintenance for a more convenient time.
- End users — Find cost savings. Fleet managers can monitor their operators to identify common occurrences of idle fuel burn. With additional training, operators can work more efficiently and save gallons of diesel fuel each year.
With the increasing amount of data available today, Somers thinks some in construction may be hesitant to take advantage of machine insights because they’re unsure where to start. His advice is to start small.
“I always kind of really encourage everybody to pick something in your business that you know you can get better at,” he said. “Then figure out what technology you can implement to achieve that.”
For those looking to get started in telematics technology, a device like TCG-4lite may be the perfect fit. With its low cost of entry, this device can get any number of mobile machines connected to global networks, whether a small set or a large vehicle fleet. With telematics on board, machines can be accessed remotely for real-time status updates, troubleshooting, software updates and more.