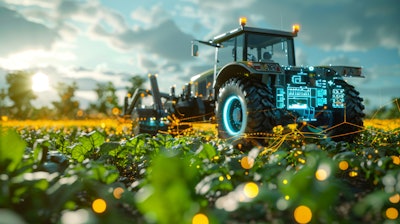
In the industrial and commercial transportation industry, OEMs are hard at work to make their products safer, more sustainable and more connected. The pace of innovation has undoubtedly accelerated, which is both exciting and challenging, especially as vehicles and equipment with greater autonomy hit the market. In fact, the global autonomous off-road vehicle and machinery market is projected to reach $62.9 billion by 2031.
However, the trend of autonomy is nothing new. Just as passenger cars have become smarter over the years, so too have those in the off-highway industry. Currently, the industrial and commercial transportation industry is at level 2 — partial automation. In the next five years, the market is expected to be at level 4, with a high level of automated function in most new vehicles. This means functional safety must be integrated not only into the design but also as part of the development and quality management process to meet ISO 26262 as well as future standards.
Commercial vehicles of tomorrow will have a much deeper understanding of their surroundings and the routes they travel thanks to innovative functionalities. Advancements in driver assistance and automation, infotainment options, 360-degree camera systems, high speed V2V and V2I communications and a wide range of essential safety features will bring many advantages. Not only will they increase satisfaction and safety for drivers, but they will also help to grow the productivity and performance for operators and lower the total cost of ownership for vehicle owners. From a sustainability standpoint, new features are likely to significantly reduce fuel consumption, decreasing a vehicle’s overall environmental impact.
Harsh Environments Require Durable and Robust Connectivity
Agricultural, construction and heavy-duty vehicles are designed to withstand years of rigorous use in extremely harsh environments, battling elements like gravel, dust, wind, water and more. With such long lifespans, manufacturers must design vehicles that not only meet not the current demands of the market but also that are ready for future technological advancements.
In the construction and mining industries, vehicle safety and productivity are paramount. These vehicles often face hazardous conditions, such as uneven terrain or confined spaces, which can lead to accidents like rollovers or collisions. Today’s 360-degree camera systems are essential to help the driver maneuver safely over varied terrain and create a safer worksite. The challenge within these industries is to add connectivity that enables the intake of key information from the environment for a real-time response, while at the same time being durable enough to withstand dirt, chemicals, water, high vibration and thermal shock. In the future, construction and mining equipment will use this data connectivity to become smarter and more automated, with the goal of enabling operators to work remotely in complete safety. Additionally, thanks to sensors and connectivity, predictive diagnostics have and will continue to become more advanced, allowing operators to anticipate equipment failures before they occur, which minimizes downtime and reduces repair costs.
For the agricultural sector, sustainability and productivity are a critical challenge. Farmers face increasing pressure to reduce their environmental impact while maximizing crop yields. To help address these challenges, advances in connectivity and automation can enable and improve precision and smart farming. By implementing sensors and data connectivity, agricultural machinery can respond quickly to environmental changes, optimizing processes like seeding, irrigation and pesticide application to increase efficiency and minimize waste. What’s more, these systems have the power to allow agricultural vehicles to monitor soil conditions and weather patterns, and make real-time decisions on planting, watering and harvesting to maximize both sustainability and productivity.
More Sophisticated Networks are Needed as Technology Advances
The connected systems and devices of off-highway vehicles cannot work properly without a sophisticated network for the transmission of high-speed data with low latency throughout the vehicle, enabling all information gathered by the devices to be processed through one or more on-board electronic control units (ECUs) to create a complete model of the vehicle and its environment. By leveraging connectivity, these vehicles then send real-time performance data to central systems, further enabling improved productivity and efficiency.
As demand increases for automated functionality, data connectivity and advanced features, the limitations of existing systems, such as CAN bus protocol, are becoming evident. While more CAN networks can be added to create additional bandwidth within an existing system, this is only possible for so long. As data communications requirements increase, completely new architectures will be needed. This is where Ethernet comes into play. Ethernet is rapidly replacing CAN in key areas where higher bandwidth and performance are necessary. In fact, the automotive industry has been developing new Ethernet standards tailored to meet the harsh requirements in industrial automotive communication networks, using 100BASE-T1 physical layer communication protocols based on the OPEN Alliance.
Overall, Ethernet is much faster than CAN. The 100 BASE-T1 and 1000 BASE-T1 Ethernet protocols can transmit 1 GB/s via UTP (Unshielded Twisted Pair), compared to only 500 kB with CAN and 1 MB/s with CAN-FD. Additionally, Ethernet allows for a significant increase in the number of devices that can be supported in the network while enabling much higher speeds. Thanks to the technical work being done on Ethernet protocols for autonomous driving in passenger cars, the commercial vehicles space can use this as a basis to address their own new trends.
There is not much difference from an electrical standpoint between passenger cars and industrial and commercial vehicles. However, application-wise, Ethernet must comply with two key performance needs for off-highway vehicles: mechanical resilience and higher vibration. Within extreme environments, mechanical resilience and higher vibration require larger component parts and larger pins. The larger the component, the more features can be put in to ensure high reliability. Larger components are also required for serviceability as service teams do not want to handle smaller and sometimes more fragile parts.
Connectors and Cables Must Meet the Demands of the Future
As vehicle designs evolve so too must the connectors and cables that facilitate these advanced networks. Connectivity systems with Ethernet in off-highway vehicles must be extremely advanced and designed to ensure high corrosion, temperature, dirt and vibration robustness as well as high speed performance. Not only do products need to meet Ethernet protocol for increased bandwidth and increased speed, but they also need to maintain a high level of reliability. For example, some Ethernet connectors are ruggedized and sealed for operation and field maintenance in heavy-duty environments, while at the same time providing robust full duplex, wire-to-wire connections for multifunction displays, telematics, telemetry units, infotainment modules and media access controllers. To secure contact retention, connectors for new systems should feature a built-in secondary locking and modular applicability for multiple panel thickness.
Moving forward, it will be essential for OEMs to incorporate Ethernet into their vehicle and equipment designs to meet the growing demands of safety, productivity and sustainability. By consulting with engineering experts, OEMs can better understand the intricacies of network topology and technology to ensure they are building vehicles that can support advanced automation, increased connectivity and robust data transmission — all while ensuring long-term durability and performance.