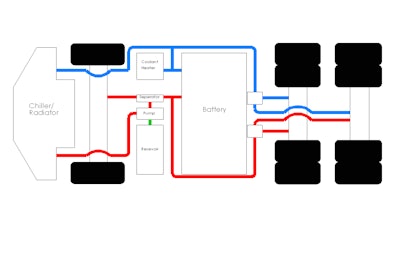
The electrification of commercial vehicles creates new challenges in thermal management of battery packs, drive motors, and high voltage electronics. In some configurations, more than 20 separate line assemblies are required per vehicle. Clearly, the conveyance of coolants to e-drive components relies on robust yet efficient circuits.
Aluminum tubes and piping offer an optimal solution for e-mobility thermal management compared to plated steel, rubber or plastic.
Benefits of aluminum for thermal conveyance
Aluminum can better withstand a commercial vehicles’ extreme duty cycles and allow for longer mileage/service life, while minimizing downtime for line replacements compared to the useful life of plastic or rubber alternatives.
Aluminum is also favored over steel for its inherent corrosion resistance and does not require toxic and environmentally hazardous surface treatment as required for carbon steel. When compared to the surface treatment requirements for steel, aluminum is on par in terms of total production costs by eliminating the plating process which reduces production cycle time; plating is often a bottleneck due to the limited supply base in North America. Designing aluminum lines for e-drive thermal management reduces supply chain risks to commercial vehicle OEMs as compared to steel.
The table below compare the benefits of aluminum versus other material options.
Criteria | Aluminum | C. Steel | SST | Rubber | Plastic |
Useful Life/Reliability | High | Moderate | High | Moderate | Low |
Environmental Impact | Low | Moderate | Moderate | High | High |
Weight | Low | High | High | High | Low |
Durability | High | High | High | Moderate | Low |
Corrosion | Low | High | Low | N/A | N/A |
Formability | High | High | Moderate | N/A | N/A |
The inherent corrosion resistance of aluminum can be equivalent to rubber or plastic but has other unique advantages. Aluminum has at least a 50% tighter bending radius over rubber depending on hose reinforcement. Likewise, plastic’s bend radius is 10 times the diameter to prevent kinking unless a thermo-form process is incorporated. On the other hand, aluminum has a 1:1 bending radius versus diameter which allows OEM design engineers more routing flexibility to address tight spaces typically found in BEV (battery electric vehicle) packaging. Aluminum also withstands higher radiant or convective heat conditions whereas plastic and rubber otherwise requires thermal shielding. Other advantages which promote aluminum over polymers or organic rubber is ozone and UV resistance, as well as stronger mechanical properties.
One-third lighter than steel, use of aluminum can contribute to incremental gross vehicle weight savings which translates to increased payload. A higher revenue-generating payload results in cost savings per mile of energy consumed, and more cash put to the bottom line. Aluminum: cradle-to-cradle²Stark Manufacturing
Aluminum is environmentally friendly, with global recycling rates around 90% in transportation applications1. Used aluminum is more valuable than virgin material by being easily and endlessly recycled without affecting material properties. And energy required to process recycled aluminum is 95% of the energy needed to produce the primary alloy. Recycled aluminum has a high value through-out the life cycle by being self-supported; a unique material benefiting society overall. Lastly, carbon and stainless-steel alloys will soon require additional processing costs to meet Europe’s new lead-free standards, which could become a U.S. standard in the future, as well.