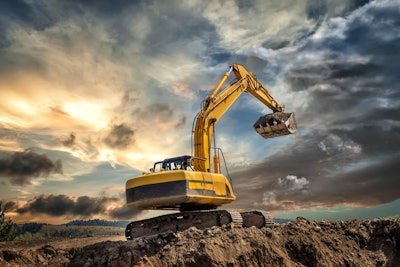
Electrification is not new to the original equipment manufacturer (OEM) world. The surge in electrification during the past decade illustrates its rising influence across multiple industries and in the global manufacturing conversation. Coupled with technological advances, such as automation and big data, electric and hybrid equipment continues to break ground among manufacturers.
Where fossil fuels were once the sole option for powering equipment, electrification is matching (and often exceeding) the performance and operational costs of combustion engine power sources. Further bolstering this trend of electrification is closing the cost of ownership gap between electric power and carbon dioxide (CO2) emitting counterparts. Increased regulatory pressure on manufacturers to reduce CO2 emissions is also requiring industries to look at alternative energy sources. With technology and affordability combining to make electrification more feasible, OEMs are looking at which electric solutions work best for their operations.
Why Should OEMs Switch to Electric and Hybrid Equipment?
International pressure on organizations, including OEMs, is growing to make the switch to electric vehicles (EVs) and hybrid vehicles to reduce greenhouse gas (GHG) emissions. Specific regulations vary from city to city and country to country, but the overwhelming strategy across all regulatory bodies is to reward manufacturers for lowering CO2 equivalents (CO2e). This reward structure is a practical response to the recent commitments that countries worldwide have made to achieving net-zero emissions by 2050. With the clock ticking toward this deadline, countries and the OEMs operating within them are becoming motivated to find energy solutions that can effectively power the industry without further contributing to GHG emissions.
Construction’s Role in GHG Emissions
Global regulatory bodies are heavily targeting the construction industry because of its position as one of the largest emitters of GHGs. However, until recently, it has been difficult for the industry to make the shift to electrification. The demands on construction equipment are rigorous and can vary drastically based on the project and site location. Previous iterations of electric equipment were often too costly or too cumbersome to warrant a switch from fuel-based models.
Advancements in lithium batteries and their charging solutions have contributed significantly to the construction industry’s movement toward electric and hybrid equipment alternatives. Several recent developments make the conversion of heavy-duty equipment a realistic option:
- The installation of onboard chargers on construction vehicles
- Offboard charging stations provide a steady supply of charged equipment
Benefits of Going Electric
The two developments that have made electrification in construction more realistic speak to one of the pivotal differences between electric and fuel-based power: adaptability. In a fuel-driven application, the solution to extending power is to increase the amount of fuel burned. For battery-operated or hybrid vehicles, the answer is more nuanced.
Consider the difference between a standard light switch and one with a dimmer setting. The former only has two modes: “on” and “off.” The dimmer setting, however, has a range of brightness levels available to the user, depending on the scenario. The lighting needed for a winter night will likely be brighter than the lighting required during a summer evening. Similarly, electric and hybrid power solutions offer a range of power to users that fuel-power sources cannot.
In addition, battery chemistries can be tailored to specific machinery and applications. The engineering of battery chemistry and charge profile takes more time on the front end, but if done correctly, the result is a charging solution that optimizes power while maintaining performance. Matching electric machinery with the appropriate voltage for an application will also go towards extending the life of the equipment itself. Electric vehicles with complimentary charging solutions are the epitome of working smarter, not harder.
Operational efficiency is not the only benefit of making the shift to electrification. Removing GHGs from a construction site can positively affect worker health. GHGs not only harm the environment, but they pose serious health concerns for personnel. Increased exposure to harmful gases puts people at increased risk for cardiovascular and respiratory illnesses. Electric construction vehicles are suited to targeting air quality safety concerns for operators. Fuel-based vehicles operating indoors require additional ventilation systems to meet safety standards for workers. With zero emissions, electric vehicles bypass the ventilation requirement.
One final benefit is to the general public. Construction can be a noisy industry. Electric equipment operates at much lower volumes than fuel-based machinery. For residential sites with noise level parameters, electric equipment is a better solution than louder gas alternatives.
With lower volume levels, site managers can extend operations into evening hours with minimal disturbance to neighbors. Reduction of pollutants, smart charging, lower noise levels and increased safety make electric and hybrid solutions attractive alternatives for the construction industry.
Preparing for Electrification
When taking the leap to electrification, OEMs need to preplan. Take the time to perform due diligence during requirements gathering. With a thorough understanding of the requirements for electrification, an experienced supplier can confidently choose the right components, topology and charge profile algorithm for the intended use.
Along with understanding what is involved in moving to electric or hybrid power is identifying what an organization needs in terms of equipment capability. By providing potential suppliers with a clear EV vision, seasoned suppliers are able to customize equipment and build component alternatives that meet specific organizational needs. This front-end planning is crucial to an electrification project’s success.
For example, the efficiencies gained by switching to an electric drive train can be undercut quickly if the incorrect battery or voltage is used in an EV because of a miscommunication between an OEM and its supplier. Time invested at the outset of the project often results in the better long-term performance of the equipment. For OEMs new to electric equipment, leaning on expert suppliers who will listen to their needs and work to find the best electric solution may be helpful.
Electrification is here to stay, and many pathways are available for OEMs seeking to switch to full or hybrid solutions. Building a network of trusted and experienced suppliers is important to select proper components and ensure the correct configuration. Experienced engineering and regulatory teams, whether internally or through suppliers, allow OEMs to keep a pulse on new technology, stay ahead of regulatory requirements and fast-track their growth ahead of competitors.
Rod Dayrit is the director of business development for Americas and Asia at Delta-Q Technologies.