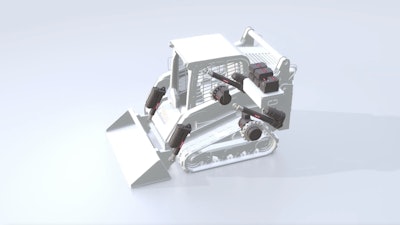
New machines arriving in construction industry rental fleets could be a harbinger of the type of off-road vehicles that construction and utility companies will increasingly operate on jobsites soon. By way of background, equipment dealers Sunbelt Rentals and United Rentals have made sizable investments in electric vehicles when each bought hundreds of Ford F-150 Lightning trucks. Last year, Sunbelt announced a strategic partnership with Doosan Bobcat to invest “in a large fleet of Bobcat T7X all-electric compact track loaders and electric compact excavators.” Last fall at bauma, Komatsu demonstrated a first-of-its-kind, all-electric compact wheel loader.
The Bobcat all-electric T7XBobcat
With all-electric actuation and power, off-highway vehicle OEMs, equipment rental companies and operators can reduce overall maintenance costs and enhance safety and sustainability (by reducing use of fuel, oil, and emissions). For this article, think of sustainability as using a resource so as not to deplete or forever damage it.Komatsu’s all-electric wheel loaderKomatsu
What Goes into All-Electric Technology?
With an all-electric construction vehicle, the powertrain gets a battery for its power source and a set of mechatronics (electric motor, battery, power electronics and electric cylinders) to control the traction and actuation needs of the machine. All-electric, off-road vehicles also have a built-in electric vehicle control module (EVCM) computer processing unit and software to control the motion, and sense and monitor the tasks they are accomplishing.
This interconnected mechatronics help the machine maneuver, control motion and send signals to safely lift, tilt, reverse and move forward. Each axis on the machine can be independently and precisely controlled. However, they are tied together with software, sensors and telemetry making it easy for the manufacturer to develop valuable functionality for their customers via minimally invasive software changes. This is similar to how Tesla and Apple introduce new features through software updates, instead of swapping hardware in and out. The all-electric system described above enables this capability in off-road vehicles. A digital software framework like this makes a construction vehicle automation-ready, enabling OEMs to build digital and software-configurable machines for users.
In the past, workers carried a series of stand-alone products and tools to get a job done. Think of a mobile phone, digital camera, GPS, and a computer, which linked you to the internet. Once these were integrated into a single product, there was new functionality, value and even new industries were born. That is not unlike the value of digitally connecting multiple machine subsystems. The connectivity creates entirely new value from construction machines, while making construction safer, more productive, autonomous, and sustainable.
The Benefits of an All-Electric Machine
The maintenance benefits of an all-electric machine are just like the ones offered by the automotive industry. All-electric systems have fewer components, sensors, connections, filters and fluids to service. The reduced number of parts equal fewer points of failure and increased use of the vehicle. The switch from hydraulic to all-electric actuators also means a machine builder eliminates leaks that may occur with hydraulic fluid. Fluids have a carrying cost and an environmental impact. All-electric propulsion and motion control also decrease (and in some cases eliminate) noise from an off-road vehicle, which reduces noise pollution and leads to a better working environment. As for safety, by eliminating large hydraulic pumps on these machines, operators and workers alongside a machine can easily speak with and hear one another.
The Challenges of All-Electric Off-Road Vehicles
One common electric deficit cited is all-electric actuation is not as powerful as conventional hydraulic systems. The opposite has been proven with compact construction equipment. All-electric machines perform as well as or better than those with hydraulic systems. For example, when a diesel engine idles, it has reduced torque, and the engine must step up to meet whatever demand the load places on the machine. But electric motors offer an operator instant, peak torque at zero speed.
A construction engineer collects data on a vehicle being tested at a facility in West Seneca, New York.Moog, Inc.
Another challenge to an all-electric fleet of construction vehicles is quickly recharging a battery in the same timeframe it takes to refuel a construction vehicle. This is a significant issue for automobiles traveling long distances, but off-road vehicles used for digging, hauling and lifting do not travel long distances. With the fast-charging capabilities available today, a construction site manager could have a transportable recharging station and recharge vehicles on a jobsite throughout the workday.
Final Thoughts
Looking forward 10 years, we will look back and see a remarkable transition from analog to intelligent digital machines. This shift enables robotic control for off-road vehicles and a wealth of machine-level data. With the right designs and manufacturing systems, OEMs can harvest this data and gain key insights that increase jobsite productivity. When an OEM combines its connected machines with advanced sensors and capabilities, these insights go beyond the bounds of traditional fleet telematics. As machines and systems get smarter, artificial intelligence can serve as a catalyst for even more advanced insights that will move the off-highway vehicle industry to widely adopt intelligent digital machines.
A possible precursor for how the construction industry’s journey to electrification might play out is flight simulation. For decades, the two-story-tall simulators pilots climbed into to earn their FAA certifications were hydraulically powered. Only hydraulic technology could survive the system requirements of these massive simulators as they tilted back and forth to mimic takeoffs, landings and other aerial maneuvers. But once the electric motion control technology matured to meet the system and lifecycle demands, all-electric simulators, which were cleaner, quieter and less costly to maintain, install, and operate, dominated the simulator market. Today, the flight simulator market is all-electric.