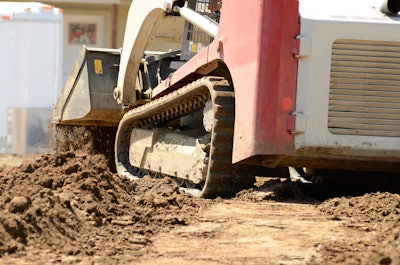
Many people doubt the potential for the electrification of off-road equipment. Indeed, many in the industry think it is impossible to realistically convert larger off-road equipment to zero emission powertrains. While it is true that shifting many categories of off-road equipment to zero emissions is a big challenge, there are strong reasons to believe that it is possible and that it will happen fast.
Perhaps the best evidence is to look at the progress that has been made so far. Even just three years ago, most off-road original equipment manufacturers (OEMs) didn’t have any electric models. Now they nearly all have at least one–especially in the construction sector. Off-road equipment users and OEMs need to properly understand the prospects, opportunities and barriers surrounding electrification. It’s also important to know that batteries aren’t the only electrification option, with hydrogen fuel cell electric powertrains providing a strong alternative.
Where Is Progress Now?
Battery electric solutions are one of the easiest ways to achieve a zero-emission powertrain because the technology is readily commercially available, but there are still major challenges such as requirements for recharging in remote areas and for very large batteries in some instances. For this reason, compact equipment is the logical place for most off-road OEMs to start, and this is where most of the progress has happened to date.
Construction Equipment
The most advanced segment in terms of recent electrification progress is compact construction equipment. There are already many electric construction equipment types available in the US, from excavators to electric skid steers, meaning that in theory it’s possible to electrify large portions of the construction equipment market right now. At CALSTART, our research shows that progress is faster than often assumed. For example, full electric mini excavators already accounted for 5% of the total US mini excavator market in 2021. By 2029 this will be 15%.
Construction equipment has had strong progress in electrification compared to some other off-road categories because it is probably the easiest off-road segment to electrify. Why? One reason is that a lot of construction is in built up areas, meaning that charging infrastructure is easier to set up. Another reason is that much construction equipment is compact. Finally, while there are general well-known benefits to using electrified equipment (such as lower fuel and maintenance costs), there is one that is specific to construction: electrified equipment is quiet meaning. It can allow for extended working hours on sites in built-up areas.
Agricultural Equipment
Like the construction equipment market, small and lightweight agricultural equipment is the area that it is feasible to electrify. California as an example. Vineyards and orchards tend to require smaller machines, which has led to good local progress with electrifying agricultural equipment.
In terms of market projections, numbers of electric tractors in the field will remain small out to 2029, but growth rates are fast. For example, out of 272,624 two wheel-drive tractors in the field in the U.S. by 2029, only 2,726 (about 1%) will be battery electric, with a further 21,810 (8%) being hybrid (mild and full) by that same year. But compare these figures to 2022 and see a high rate of growth. In 2022, there are projected to be only 51 battery-electric two wheel-drive tractors in the U.S., and only 508 hybrid (mild and full) tractors (see Table 1).Table 1. Two-wheel drive tractor growth rates in the U.S.CALSTART
Challenges of the Electrification of Large Off-Road Equipment
It’s easy to look at large off-road equipment and conclude that electrifying it is impossible. Easy, but wrong. Electrification of the largest off-road equipment is possible, and it is going to happen. While electrification can mean a battery electric or hydrogen fuel-cell electric, battery electric remains the easiest first port of call for vehicle decarbonization, and our beachhead model—developed in conjunction with the California Air Resources Board (CARB)—shows why batteries have more potential than many assume. The principle is simple: advances made in electrifying smaller equipment will spill over into larger machines. These advances can include shared components, reduced component cost and increasingly efficient supply chains.
Figure 1. The beachhead modelCALSTART
Hydrogen Fuel Cells
Battery electric technology is capable of far more than most people think, but it is likely to have its limits, especially in sectors such as agriculture where the largest equipment is very large indeed, and operating sites are often remote. Yet the existence of hydrogen fuel cell technology is what gives me confidence that, no matter where the limits of batteries lie, electrification of all off-road equipment is possible. The big advantage of fuel cell technology is its high energy density which allows it to easily drive large equipment for extended periods. While hydrogen fuel cells also require expensive infrastructure (and so face some of the same challenges as electric equipment operating in remote areas), the big difference is that it is immediately clear that fuel cells can drive the largest vehicles.
Batteries, in contrast, must still prove themselves. The other issues are that producing hydrogen is expensive, and fuel cells, while efficient with 60% efficiency (compared to 20% to 30% for internal combustion engines), are outstripped by the efficiency ratings of lithium-ion batteries which are often up to 99%. Despite these drawbacks, hydrogen fuel cells will be able to step in wherever batteries cannot go. They may cost a little more, but they can do the job.
The CORE Program
Have you heard of the CORE program? It’s a $125 million funding project providing point-of-sale discounts via vouchers of up to $500,000 each on off-road zero-emission equipment purchased in California. Any end user operating such equipment in California, or any global OEM marketing their products in California, may find this of interest. Learn more at the California CORE website.