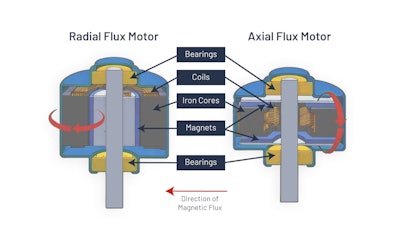
Before a recent surge, axial flux motors were used in niche applications and premium automobiles. They were more difficult to engineer, and their manufacture was not scalable. This resulted in the benefits of these motors not being worth the cost except in higher priced vehicles where space was at a premium.
As different vehicles have migrated from internal combustion engines to hybrid configurations or fully electric, the benefits of and demand for axial flux motors has increased. With some manufacturers scaling their production, the cost is decreasing, as well. But how are axial flux motors different, and what are their benefits?
Radial flux motor versus axial flux motor design
Based on the orientation of the magnetic flux, electrical machines can be classified into two categories (see Figure 1):
- Radial flux. The magnetic flux direction is radial to the axis of rotation
- Axial flux. The magnetic flux direction is parallel to the axis of rotation.
Radial flux motors are the most used motor today in vehicles and equipment. The cylindrical rotor moves inside a cylindrical stator. Because of the components (especially the coil layout) within a radial flux motor, it is much longer than an axial flux motor.
Axial flux motors are flatter, often called pancake motors. In space-constrained applications like hybrid and electric vehicles and equipment, these flatter motors are ideal.
A key determinant of torque and power delivery and electric motor efficiency is the magnetic field strength. Magnetic field strength will be higher if the magnetic flux path is shorter.
Field strength increases with diameter (D) of the rotor containing the magnetic material and reduces with the length (L) of the flux path. A higher D/L ratio provides a motor with a higher efficiency and a higher torque density.
Figure 2: Diameter-to-length ratio.Turntide Technologies
Axial flux motor physics
For radial flux motors, the torque is proportional to the square of the diameter multiplied by the length. For an axial flux machine, the torque is proportional to the cube of the diameter and has no significant influence on the length.
Because of this, a smaller axial flux machine can provide more torque than a larger radial flux machine. If the equipment design requires high torque and power delivery and low motor weight and volume are necessary, an axial flux machine is the ideal choice.
Torque, power delivery and range benefits
A lower flux path means more torque, and depending on their size, some axial flux motors can provide two to four times more power at 50% less weight. While the smaller size is important for these motors to fit into electric or hybrid configurations, the decreased weight is also a major factor. In a vehicle, a 10% weight decrease means a vehicle range increase of 13% to 14%.
The decreased weight and increased range also result in lower total cost of ownership. In addition, the high-torque, low-speed operation of axial flux motors allows for reduced gearing ratio, further boosting the weight savings.
Axial flux motor topologies
Many topologies, features and design options are available for axial flux motors (see Figure 3). Selection features include:
- D/L ratio. Short machines with large diameters
- Design modularity. This is with stacking motors.
Figure 3: Axial flux motor topologies.Turntide Technologies
Design considerations include:
- Strong axial magnetic stator-rotor attraction force
- Mechanical design and manufacturing technology for production scaling.
Several topologies available are single stator and single rotor, double stator and single rotor, and single stator and double rotor. However, a double-stator, single-rotor motor with internal permanent magnets is preferred because this configuration offers:
- Shorter machine length
- Effective winding cooling
- 96% efficiency.
Cogging torque
Cogging torque, the interaction between the permanent magnet motors and the slots in the stator, can be an issue with some axial flux motors. However, the double stator, single rotor has a low cogging torque or in many instances no cogging torque.
Design and testing
Using finite element analysis and computational fluid dynamics ensures proper operation and effective and efficient cooling. Cooling can be carried out primarily by a water-ethylene-glycol system or an oil-cooled system.
To ensure the motor has been designed using the latest technology, talk with the motor manufacturer and ask for the analysis data.
Exhaustive testing and validation to ensure performance, efficiency and durability are also important. Some test results to ask about include:
- Dynamometer tests. Evaluate torque, speed, power and efficiency under different operating conditions (also called dyno testing)
- Thermal performance tests. Assess the new motor’s ability to operate reliably within the designed temperature parameters
- Durability tests. This helps evaluate a motor’s longevity and resistance to mechanical stress, vibration and environmental factors
- Test bench. Validates the simulation results
- Climatic, vibration, EMC and material suitability tests. Evaluate their compliance with the standard to which they are built (for finished motors).
Figure 4: Exploded view of an axial flux motor.Turntide Technologies
Use cases and applications for off-highway vehicles
Axial flux motors are ideal for hybrid configurations or fully electric systems of any vehicles or equipment, especially if space is limited. This includes:
- Construction and mining equipment (excavators, wheel loaders). They can be used to improve wheel traction, track traction, and ancillary functions such as slew and swing
- Street sweepers. They can be used to improve traction and sweeping implements
- All-terrain vehicles. They can be used to improve traction.
Figure 5: This torque plot is one example of some of the testing and design that should be conducted on an axial flux motor.Turntide Technologies
The increased use of axial flux motors
Axial flux motors are superior technology when compared to radial flux motors. They provide higher performance, leading to smaller, lighter, more efficient and more powerful motors. They also perform well in diverse applications especially when space limitations are a concern.
While costs for axial flux motor may have been a deterrent to their widespread use, manufacturers are now scaling their production. This scalability will decrease their cost and make them a more viable choice for vehicle and equipment manufacturers moving forward.