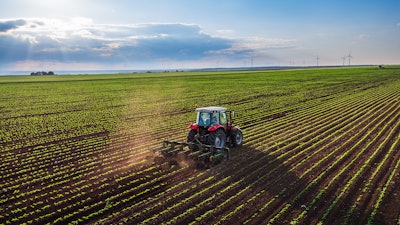
The emergence of hybrid and electric systems in off-highway applications has represented a significant leap in sustainability and efficiency. As both equipment manufacturers and operators seek to reduce emissions and operating costs while complying with stringent environmental regulations, the importance of selecting the right system for an application requires careful consideration of various factors and components. While it may be tempting to identify a one-size-fits-all solution, it’s better to consult a trusted provider that can offer insights into the critical factors influencing system integration.
Understanding the Core Components
Hybrid and electric systems comprise a complex network of components, each contributing to the system's functionality and performance in unique ways. The heart of any hybrid or electric system is its power source, which stores and/or delivers energy to drive the equipment’s propulsion and auxiliary systems. Options including batteries, fuel cells, internal combustion engine (ICE) generators, diesel engines, the local electric grid, and even wind and solar are all viable. The selection of an appropriate power solution depends on factors such as application type and usage profile (e.g., range), weight and space constraints, regulations, safety considerations, redundancy needs, maintenance requirements, cost, available infrastructure (e.g., charging and fuel availability), and environmental impact (e.g., emissions, noise). Further considerations within each option are influenced by available and emerging technologies (e.g., energy density, battery chemistry, battery charge and discharge rates, alternate fuels).
Electric motors serve as the workhorses of hybrid and electric propulsion, translating electrical energy into mechanical power to drive the primary equipment or auxiliary functionality. There are many variations in electric motors based on the operating principals selected, such as operating current type (AC or DC), direction of flux (radial, axial, or transverse), and how the electromagnetic field is generated (induction, or permanent magnets). Control of the motor is done by inverters or a VFD. Selection depends on the type of motor being used, the source voltage, the equipment power architecture, and cooling, among other considerations. Additionally, factors like cooling methods, voltage compatibility and weight and size constraints must be carefully evaluated to ensure optimal performance and longevity.
Efficient power distribution and management systems are essential for optimizing energy usage and ensuring seamless operation of the overall system. Advanced control algorithms, integrated with sophisticated sensors and monitoring devices, enable real-time adjustments to power flow, maximizing efficiency and minimizing waste. Additionally, intelligent power management systems facilitate seamless transitions between different power sources, such as batteries, generators and engines, based on operational demands, physical location and environmental conditions.
Supplementary components such as generators, and various power electronics such as inverters, converters and battery chargers complement the primary propulsion system, providing backup power, charging capability and sources for auxiliary loads. Generators, powered by diesel or alternative fuels, besides being a primary power source, can provide power for auxiliary systems and recharge batteries as needed. Inverters and chargers convert DC power from batteries into AC power for onboard equipment and systems; and convert AC power from grid power to DC for charging batteries. Converters change voltage levels as appropriate to ensure motor and battery compatibility and can provide DC power for low voltage house loads or traditional 12/24 VDC battery charging. Proper selection ensures seamless integration with existing vehicle and/or equipment infrastructure.
Control systems play a crucial role in monitoring and regulating the performance of the overall system. Integrated with user-friendly interfaces and intuitive software, modern control systems enable operators to monitor key parameters such as battery state-of-charge, component health and equipment status in real-time. Additionally, advanced diagnostic features and predictive maintenance algorithms can help identify potential issues before they escalate, ensuring maximum uptime and reliability. When the control system is properly engineered, the user can operate the system without needing to know or care about all the power generation, transmission, conversion and management happening around them.
When selecting a hybrid or electric propulsion system, various factors must be considered to determine the components needed for your system. The appropriate power source, electric motors, power distribution and management system, supplementary components and control systems must all be identified on a case-by-case basis.Twin Disc Inc.
Key Considerations for Off-Highway Equipment
Pure fossil fuel systems have sufficient energy density to allow for generous overpowering of the system. Hybrid and electric systems do not have this luxury. Many factors require careful consideration, each influencing the system's performance, cost and environmental impact. To ensure seamless integration of a hybrid or electric propulsion system into off-highway equipment, stakeholders must provide comprehensive information to system designers and engineers. A detailed project narrative provides essential context and insights into the equipment type, equipment design, drivetrain configuration, intended use, operational requirements and performance expectations. By understanding the project's scope and objectives, system designers can tailor solutions to meet specific needs and challenges effectively, while providing components that work seamlessly as a single system.
Understanding the equipment's power and energy requirements at various speeds, operating conditions and usage profile are also critical for selecting the appropriate drivetrain components and configurations. Factors such as operating range, speed profile, power requirements, efficiency, auxiliary loads and maneuverability dictate type of power source, the size and capacity of energy storage systems, as well as the selection of complementary components such as motors and generators. Additionally, considerations like power regeneration (even from auxiliary onboard systems), grid power capability and alternative fuel availability can further influence efficiency and overall operating costs over the system's lifespan and thus must be carefully evaluated to achieve optimal performance and fuel savings.
Finally, analyzing the equipment duty cycle or operation profile, including operating hours, power demand profiles and energy consumption patterns, provides valuable data for sizing onboard energy storage systems and auxiliary power sources. By matching system capacity to actual usage patterns, designers can optimize energy management strategies and maximize operational efficiency.
The initial investment in a hybrid or electric system is usually more substantial than an equivalent fossil fuel system. Beyond the upfront costs of equipment and installation, factors such as maintenance, training and infrastructure upgrades must be factored into the total cost of ownership. That said, it's essential to consider the quality-of-life benefits stemming from emissions and noise reduction, as well as financial benefits, from savings in fuel costs to potential incentives or rebates available for adopting eco-friendly technologies. This is especially true in regions with requirements such as emissions standards and environmental regulations, which play a significant role in shaping the adoption of hybrid and electric vehicle and equipment drivetrain systems.
The Role of Suppliers in Electrification
The adoption of hybrid and electric drivetrain systems represents a transformative shift in the off-highway industry, driven by the need to reduce emissions, enhance efficiency and comply with evolving regulatory standards. However, despite these new waves of considerations, both equipment manufacturers and operators still prioritize safety, reliability, efficiency, maneuverability, system redundancy and comfort. By partnering with trusted suppliers and leveraging innovative solutions, stakeholders can address these needs while reducing environmental impact and operating costs.