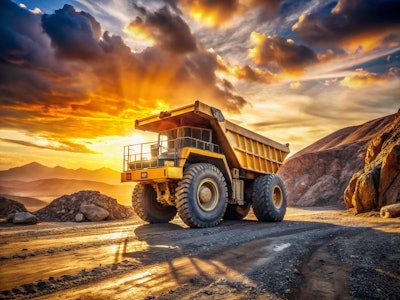
The construction industry's transition toward electrification demands careful evaluation of motor technologies, cooling systems and integration strategies. This examination of key technical considerations helps guide successful off-highway application implementation.
The rise of permanent magnet motors
Permanent magnet motors (PMMs) are becoming a preferred choice for electric construction equipment due to their high-power density, efficiency, and compact design. Compared to the more traditional induction motors, PMMs provide several advantages such as:
- High torque-to-weight ratio: This makes them Ideal for demanding applications such as construction.
- Improved efficiency: Operates efficiently across a wide speed range.
- Compact design: This enables flexible integration into existing machinery designs.
Application considerations for motors in off-highway vehicles
When selecting electric motors for off-highway vehicles, engineers must consider operating conditions. Digging a little deeper, this includes knowing about specific operational demands, application-based load profiles and requirements specific to the industry. Performance demands such as peak load management, maximum torque requirements and continuous operation parameters are also important.
Environmental factors such as environment tolerance, thermal management needs and operational capabilities also need to be addressed, particularly in construction and mining, which can have hazardous areas for workers as well as the vehicles they’re operating.
When it comes to system optimization, there are a few things to consider. Operators can ensure performance validation with an efficiency map analysis, torque curve evaluation and power delivery optimization.
Energy efficiency shouldn’t be forgotten, either. Look for ways to reduce consumption while ensuring optimal operation and system efficiency.
Choosing the right magnet motor
Permanent magnet motors can be designed with either surface-mounted or internally embedded magnets, classifying them as surface permanent magnet (SPM) or internal permanent magnet (IPM) motors. Each technology offers unique advantages and is suited for different applications:
SPM motors excel in hydraulic pump drive applications and provide consistent performance at lower speeds. They also optimize efficiency in constant torque applications and deliver superior low-speed torque characteristics.
Example of a surface permanent magnet (SPM) rotor.Bonfiglioli
IPM motors support higher power density applications and can perform efficiently at higher speeds. They also offer extended speed ranges through field weakening.
Example of an internal permanent magnet (IPM) rotor.Bonfiglioli
Two thermal management approaches
Effective thermal management is crucial for ensuring optimal performance and longevity of electric motors, especially in demanding off-highway applications. The two most common methods are natural ventilation and liquid cooling.
Natural ventilation benefits include:
- Eliminates the need for additional cooling circuits
- Reduced system complexity
- Enables more radial compact installations.
Liquid cooling benefits include:
- Enabling operation in confined spaces, which reduces motor length while keeping the output power constant
- Provides consistent performance in harsh environments
- Offers the choice between oil or glycol cooling.
Electric motor performance optimization
Efficiency maps provide crucial visual representation of motor performance across operating conditions.Bonfiglioli
Efficiency maps, for example, provide crucial visual representation of motor performance across operating conditions. These contour plots reveal:
Operating points optimization, which highlight peak efficiency regions, optimal speed-torque combinations and performance boundaries at different operating conditions.
System design benefits from these maps include energy consumption reduction strategies, a better understanding of thermal management requirements and duty cycle planning capabilities. It also gives operators a chance to optimize battery size.
Power and torque curves
Power and torque to speed curves are critical for motor selection and system integration: Characteristics include:
- Peak torque capabilities across speed ranges
- Continuous operating limits
- Power delivery characteristics
- Field weakening region behavior.
Power and torque curves are critical for motor selection and system integration.
- Enabling accurate machine performance prediction through simulation
- Reduces development time by validating designs before physical testing
- Facilitating optimal gearbox ratio selection
- Preventing system mismatches in early design phases.
Voltage selection strategy
The choice between low-voltage (LV) and high-voltage (HV) systems requires careful consideration of many different factors. While some of the situations and challenges are similar, they manifest in different ways.
When it comes to low-voltage systems (24 to 96 Vdc), they are traditionally preferred for lower applications because:
- Wide availability of LV components
- Reduced safety system requirements
- Simplified maintenance procedures
- Lower system complexity.
While high-voltage systems (400 to 800 Vdc) are historically reserved for high-power applications, they’re seeing broader adoption due to:
- Improved component availability
- Enhanced charging capabilities
- Higher system efficiency
- Reduced current requirements.
With modern applications, advancing technology has blurred traditional voltage selection criteria because high-voltage components are more viable for lower applications. System choice now depends on specific applications. Other factors to consider include available charging infrastructure, safety considerations, the system cost and the maintenance expertise available on-site.
Customization and integration considerations
The integration of electric powertrains into existing equipment designs requires operators and engineers to consider several factors. With modular motor design, consider things such as customizable internal stack lengths, scalable power and torque outputs and adaptable mounting configurations. The interface also should be flexible when it comes to power connections, mechanical interfaces and system integration.
For power connections, consider configurable cable arrangements, application-specific connectors and customizable terminal layouts to find the best possible solution. For the mechanical interface, consider its compatibility with already existing components to cuts costs and think about mounting options and adaptable output flanges.
System integration considerations include sensor integration points, choosing the right control system interface and cooling system connections.
The system also should be compatible, which can cause some challenges when it comes to system integration. For a hydraulic system, engineers should be aware of direct pump drive capabilities, mounting configurations and pressure system requirements. For a drivetrain adaption, the gearbox and traction should be top of mind as well as whether multiple shaft configurations are needed.
Battery technology challenges
Integrating electric powertrains into existing equipment designs requires careful consideration of design enabling, flexibility and system compatibility.Bonfiglioli
Electric systems must operate reliably in challenging environments. Engineers must design components that can withstand:
- Wide temperature ranges (-40 to 85°C)
- High vibration and shock loads
- Dust, moisture, and other contaminants.
Integrating electric powertrains into existing designs requires careful consideration of:
- Weight distribution
- Cooling system design
- Electromagnetic compatibility (EMC) issues
- Safety systems for high-voltage components
- Mechanical and dimensional constraints.
Future electrification technology developments
As electrification technology continues to evolve, we can expect advancements such as:
- Improved battery chemistries with higher energy density
- More efficient and compact power electronics
- Advanced motor designs with even higher power density
- Integrated systems that combine electronic, electric, and hydraulic technologies for optimal performance.
The electrification of construction equipment presents significant opportunities for improved efficiency and reduced environmental impact. Success requires careful consideration of motor technology selection, thermal management, system integration, and performance optimization. As these technologies advance, their adoption will increase across many applications, supporting productivity and sustainability goals.
Mattia Buscherini is Bonfiglioli eMobility Sales Manager, North America.