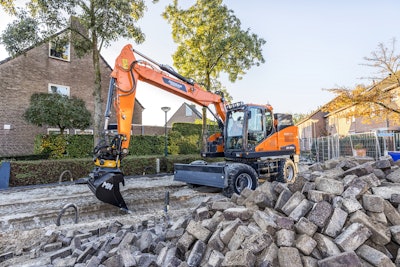
Electrification has always been a major aspect of off-highway vehicles and technology and recent trends have made it even moreso. The mining, agriculture and construction industries are grappling with changes and challenges to the power grid and how their vehicles are powered. This is even more acute with the tide shifting towards alternative energy and fuels as a viable source in certain applications.
These industry experts on the off-highway industry offered their insights on electrification in a roundtable format:
- Eric Azeroual, vice president, sales development and portfolio, Danfoss
- Lloyd Gomm, global director marketing, ZAPI GROUP
- Brady Lewis, P.E., manager, emerging products & technology, CASE Construction Equipment
- Athan Tsokolas, product manager - commercial Lithium-ion batteries, Vanguard
Question: What role does sustainability play in electrification, and how are companies leveraging it to gain a competitive edge?
Eric Azeroual: Sustainability was one of the first factors driving buyers to electric machines. By lowering energy consumption and reducing or eliminating carbon dioxide and small particle emissions, EVs improved early adopters’ sustainability credentials. While electrification drivers are changing, environmental protection and sustainability agendas still play an important role. For example, many major OEMs have a 2030 target for CO2 reduction, and there’s greater focus on the environmental impact of a machine throughout its lifecycle. Furthermore, our customers are asking us to improve the carbon footprint of our products, challenging our materials and their reusability/recyclability. This will influence the advancement of electrification in the years to come.
Lloyd Gomm: Sustainability is the core catalyst for electrification, aligning with carbon neutrality targets and ESG (environmental, social, and governance) commitments. Forward-thinking OEMs leverage this shift by:
- Expanding electrified machinery offerings to attract sustainablity-conscious consumers
- Securing government grants and incentives to accelerate R&D
- Ingraining sustainable practices into product supply chains to optimize costs.
Brady Lewis: Sustainability goals are definitely helping to drive demand for electrification. In states like California where there are robust incentive programs to boost sustainable construction, we're seeing more and more companies leveraging EV technology. But it goes beyond incentives and regulations from state and local governments. The number of projects that prioritize green credentials, such as LEED-certified projects, is increasing every year. Contractors who adopt electric machines can gain a competitive edge for winning these types of projects.
Question: How do you see emissions regulations influencing the pace of electrification in the off-highway industry?
Eric Azeroual: Emissions regulations and legislation play a significant role in the pace of electrification. Regulations create market demand for zero-emission vehicles, especially in construction. Some cities in Europe and Japan, for example, are mandating low- or zero-emission vehicles within city limits. Noise pollution is also an increasing target of legislation. In these cases, electrically powered machinery may be the only viable solution. With the change of administration in the U.S., we may see the pace of electrification slow. Passenger and light-duty commercial vehicles are more likely to feel the impact. In off-highway, the impact may be more nuanced.
Lloyd Gomm: Regulatory pressure is a key accelerator of electrification. EU Stage V and US EPA Tier 4 enforce near-zero NOx and PM emissions, driving demand for electrified alternatives. Carbon taxes further penalize diesel equipment, while restrictions such as London’s Ultra Low Emission Zone actively restrict fossil fuel usage. Together, these combined initiatives promise to significantly accelerate the pacing of electrification across off-highway segments.
Brady Lewis: Emissions regulations can vary region to region, but generally we see greater demand for EV machines in places with more stringent regulations. However, there are many advantages to electrification that go far beyond regulatory compliance. No matter which way regulations evolve, we expect increased adoption as more contractors realize the benefits and opportunities EVs have to offer.
Question: What strategies are being employed to maximize the energy efficiency of electric off-highway vehicles?
Eric Azeroual: Many first-generation electric machines are unable to operate for a full day on a single charge, and that’s primarily due to inefficient hydraulics. Hydraulic systems within excavators, for example, waste as much as 70% of useful power. Selecting more efficient components can help, but the bigger lever is at the systems level.
Optimizing hydraulics will improve machine runtime and could reduce the size of batteries, which are considerable benefits to upfront cost and operational efficiency. Hydraulic optimization levers include alternative architectures and technologies such as gravity lowering, independent metering, and zonal systems, which focus on driving out inefficiencies. More complex strategies add energy recuperation. Outside of hydraulics, autonomous functionality can increase efficiency as the machine is programmed to perform a task in the most efficient manner.
Lloyd Gomm: There are four strategies to consider:
- Regenerative braking systems capture energy otherwise wasted as heat, achieving a 60.1% efficiency increase over traditional brakes.
- Battery management systems (BMS) and charging algorithms boost charging efficiency from under 90% to 97%.
- Component integration and optimization reduce energy losses by streamlining system design and minimizing reliance on discrete parts.
- Telematics and IoT functionality deliver valuable duty cycle data to identify and address areas of inefficiency.
Brady Lewis: If you want an energy-efficient electric machine, it's critical to purpose-build that machine from top to bottom for electrification, rather than simply retrofitting an existing diesel machine. For example, with the CASE 580EV electric backhoe loader, we took a comprehensive approach and considered every aspect of the machine that might impact energy efficiency. And, throughout the validation process, we continued to refine systems across the unit to optimize efficiency without sacrificing lifting, digging and driving performance.
We designed the 580EV with two independent electric motors to reduce energy consumption and improve performance, with a traction motor that’s connected through the transmission to the drivetrain, and an implement motor connected to the hydraulic pumps that feed the loader, backhoe and steering systems. In loading applications, the loader hydraulics are controlled separately from the ground drive, maintaining the operator’s ability to load materials from a pile without de-clutching and still get fast loader speeds. We also looked closely at thermal management by using separate cooling circuits for different systems in the machine to better regulate temperatures for various climate conditions.
Question: How does the performance of electric powertrains compare with traditional diesel engines in heavy-duty environments?
Eric Azeroual: We’re well past the days of questionable electronic reliability in harsh environments. Three decades ago, we might have installed a sensor and hoped for the best, but electronics and electric components today are much more robust. Many components have high ingress protection and vibration ratings designed for the rigors of off-highway environments. Electric drivetrain components are more rugged and durable than their on-highway counterparts. They’re designed to handle the higher weights, loads and g-force we see. From a reliability standpoint, an electric powertrain should match or even outperform a diesel engine, even in harsh environments.
Lloyd Gomm: Contrary to common assumptions, electric powertrains can match or even exceed diesel engine performance. Comparative studies of compact electric excavators demonstrated nearly identical continuous power output and a higher peak power output versus ICE. While sufficiently high-voltage and power-dense battery systems can theoretically allow electric machines to compete with diesel equivalents, practical challenges such as battery weight, thermal management, and energy storage capacity remain key considerations.
Brady Lewis: Our electric machines deliver comparable performance as their diesel counterparts. For example, the four-wheel-drive 580EV backhoe loader offers the same breakout forces and includes the same loading and digging dimensional specs as our proven 97-horsepower 580SN model, which is its diesel equivalent.
Electrification also comes with some performance opportunities that internal combustion engines simply can’t match, such as instantaneous torque response and peak torque at any RPM. That means no waiting for a diesel engine to ramp up to meet load demands, and, essentially, no wasted energy when the machine is not at work.
Athan Tsokolas: Electric powertrains are rapidly transforming heavy-duty environments with a quiet, efficient alternative to diesel and gas engines. One of the most significant advantages is the elimination of operating emissions. This makes electric equipment ideal for indoor use, where air quality is a critical concern, and contributes to a safer work environment for operators.
Beyond these benefits, electric powertrains offer compelling performance advantages. Electric motors provide smooth, instant power delivery. This enhances responsiveness and control, which is valuable in tasks requiring precise movements. The quieter operation reduces noise pollution, which minimizes disruption in surrounding areas and improves operator comfort on the jobsite. With fewer moving parts than traditional engines, battery power from Vanguard also requires zero maintenance: reducing downtime and keeping equipment running smoothly.
Question: How are electronics helping to optimize energy usage and manage power distribution in hybrid and electric off-highway vehicles?
Eric Azeroual: The sophisticated software behind the Editron system controls and optimizes each individual component of an electric or hybrid drivetrain, leading to more intelligent management of power distribution.
Lloyd Gomm: As the industry trends toward higher voltages, electronic control modules (ECM) emerge as critical junctions for power distribution and efficiency management. Materials such as gallium nitride (GaN) outperform traditional silicon, with 10x faster electron mobility and 50% higher efficiency.
Athan Tsokolas: Electronics play a crucial role in optimizing energy usage and managing power distribution in hybrid and electric off-highway vehicles, and our integrated Vanguard Battery Management System (BMS) is a prime example of this technology. Our BMS is constantly monitoring and controlling the battery pack's operation for safety and efficiency. It monitors voltage and temperature to prevent overcharging and overheating: ensuring safety, longevity and optimal performance. Our BMS optimizes power delivery based on real-time demands, ensuring efficient energy use and extending the vehicle's operating range.
Question: What innovations are emerging in thermal management systems for electronics in extreme conditions?
Lloyd Gomm: There are three innovations that are standing out:
- Liquid-cooled battery packs for enhanced heat dissipation in high-temperature, heavy-duty applications
- Phase-change materials (PCM) that maintain optimal temperatures, regardless of climate, by absorbing and releasing thermal energy
- Graphene-based heat spreaders, which significantly improve cooling efficiency for high-power electronics.
Question: What role do you envision alternative power sources, such as hydrogen or hybrid systems, playing alongside electrification in the off-highway industry?
Eric Azeroual: I’m an electrical engineer, so I’m not a huge fan of hybrid systems. They have a place in some applications today, particularly larger machinery. But as we solve the barriers to electrification through more advanced battery technology and well-developed charging infrastructure, I think fully electric machinery will win. With hybrid machinery, you have a lot of complexity in the interface and controls of the engine and battery. It’s quite complicated to make a hybrid system work, and you still have the maintenance, emissions, and noise associated with the diesel engine. Fully electric machines are much easier to engineer, and they’re much more comfortable to operate or work around. Once you go electric, you won’t go back.
Lloyd Gomm: While numerous alternative sustainable solutions exist, to us, it’s clear that electrification remains the optimal “end-game” solution:
- Hybrid drivetrains provide an excellent transitory platform for OEMs (and thus indirectly contribute to adoption). However, they ultimately rely on fossil fuels.
- Hydrogen fuel cells remain cost-prohibitive and lack research, refueling infrastructure, and widespread adoption. While promising for specific applications, hydrogen lacks the scalability to compete with battery-electric solutions.
Brady Lewis: In this early stage of the off-highway EV industry, we are still evaluating different technologies to meet the needs of our customers. While battery powered electric vehicles are having real-world success on the small end the scale, we know that on larger equipment, it becomes increasingly difficult to manage the size and weight of a battery. The future may very well involve a mixture of technologies based on the size of the vehicle and the application demands. There are also opportunities for BEVs and other alternative powertrains to contribute to each other's successes. An improvement in drivetrain efficiency that helps a BEV can also improve performance on a series hybrid or hydrogen fuel cell vehicle.
Question: Are there any advancements in charging infrastructure specifically tailored for off-highway equipment?
Eric Azeroual: DC fast charging is the gold standard to maximize charging speed and minimize machine downtime. To enable high-power dc charging, a megawatt charging system (MCS) has been developed to allow for 3,000 A and 1,250 Vdc, eventually 1,500 Vdc enabling 4.5 MW of power. This is a game changer for large off-highway applications such as mining. But many segments of the off-highway industry will struggle to access dc fast chargers — construction and forestry are two examples.
While DC charging fills a machine’s batteries quicker, the infrastructure is much more costly. Procurement and installation of DC fast chargers can cost up to 10 times more than AC chargers. To make electrification attainable, off-highway segments that rely on AC charging need to maximize charging speed.
Lloyd Gomm: Three advances stand out:
- Mobile charging – Development of off-board, portable mobile charging solutions delivers greater operational flexibility in remote worksites.
- Wireless charging – Ideal for autonomous mobile robots (AMRs) with preprogrammed routes and industrial applications where corrosion or dirt might interfere with charging.
- Megawatt charging systems (MCS) – Seeing early development as a means to drastically reduce charge time for high-power equipment.
Brady Lewis: Charging and infrastructure concerns in the automotive space have been one of the hurdles to adoption. However, in recent years, we’ve seen the automotive industry make significant investments and improvements to charging infrastructure. Rather than trying to clear the same hurdles, CASE takes advantage of the automotive infrastructure by using the same automotive standard, a level 2 SAE J1772 connector, which is used by the majority of U.S. automakers today. This allows our machines, like the 580EV backhoe loader, to charge at the same charging stations as most on-highway vehicles. It also allows contractors and fleet operators to take advantage of a wide variety of charging solutions and supplies available in the automotive world, beyond the offering directly from CASE.
Following the automotive standard also opens more opportunities for leveraging emerging technologies like remote charging solutions. We’ve seen many companies, from start-ups to established players, innovate in this space with a variety of solutions. From large battery packs on wheels to hydrogen-powered gensets to ammonia-powered fuel cells — the common denominator with all of them is the automotive standard connector.