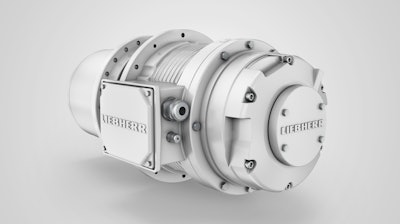
In the past year, Liebherr extended the components portfolio with its electric travel drives (FAT 325). The first drives have now been successfully put into operation for a customer in Austria. The FAT 325 was presented to the American market at MINExpo 2016 in Las Vegas.
With the launch of the new FAT 325 in 2015, Liebherr added an electric version to its hitherto hydraulically operated travel drives. On the one hand, this development takes into account the increasing demand for electrically powered crawler-tracked vehicles. On the other hand, it meets the demand for environmentally friendly technologies, since electric travel drives need neither hydraulic lines nor hydraulic oil.
In 2015, Liebherr offered a complete drivetrain – from the inverter, the motor to the travel drives – for the first time. In cooperation with the customer, SBM Mineral Processing GmbH of MFL Group, the first electric travel drives were successfully put into operation in the field of processing technology in the summer of 2016. The Austrian company is a leading and innovative supplier of complete processing and handling systems for the raw materials and recycling industries as well as concrete mixing plants for ready-mix and precast concrete.
An essential part of the cooperation with SBM is the engineering of each component. The gearboxes, electric motors and inverters are all specifically tailored to crawler-mounted mobile applications. Liebherr delivered the first individual components in June 2016 and installed them into SBM's "REMAX 1111" mobile crushing plant. During commissioning SBM was supported by Liebherr-Components' qualified staff. The component solution was successfully checked and put into operation following various tests, including turning on a 30 degree slope.
With this component solution, SBM benefits particularly from the special design of the motor's windings, as well as the rotor design with permanent magnet technology. The solution ensures a high torque from an extremely compact design. The latter enables tailor-made placement of the drivetrain in the confined space conditions of the machine. The gearboxes are further distinguished by their design, which ensures uniform load distribution across the individual stages and, thus, a high power and torque density in the transmission. The main bearing is implemented as an integral design. In this way, a long service life is achieved through a reduced number of parts.
With the IP67 protection and durable sealing systems, the entire Liebherr drive is not only protected from environmental influences, such as dust and water in normal operation. Each system is optimally adapted to its specific environmental conditions. This capability was crucial for SBM in selecting its component supplier. "Our crushers are used worldwide in extreme environmental conditions, such as high temperatures, coarse dirt and dust. That is why we like to work with companies who know from their own experience how these conditions affect the technology and components," explains Dipl.-Ing. Hermann Almer, Division Manager Mobile Applications at SBM. Based on the positive results achieved in the first project, SBM and Liebherr now have their sights on fitting Liebherr's electric travel drives into other machines.