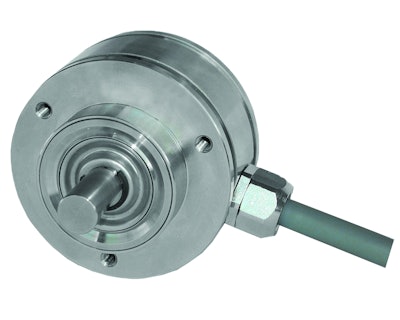
With the increasing demand for efficiency gains and improved throughput in off-highway vehicles, manufacturers must delve into the automation world of controllers, HMIs, and sensors in order to meet performance objectives. The choices facing the design engineer are staggering, and in many cases product overlap can make the decision difficult when choosing one product over another, particularly in the area of sensor feedback where a variety of technologies exist, and choosing the right one for the job is critical for optimum system performance.
In many higher-end mobile hydraulic applications, speed and/or position feedback of moving parts is essential. Knowing the speed of a hydraulic motor or the exact angle of an articulated joint is necessary information if a machine is to operate efficiently and safely. Oftentimes, this is accomplished through the use of a magnetic pickup and gear arrangement, potentiometer, hall-effect sensor, or proximity sensor. However, in instances when these devices don’t fit, encoders and resolvers can be alternatives.
A rotary encoder is an electro-mechanical device that translates rotational motion into an electrical signal, usually digital in nature. This is normally accomplished through the use of an optical or magnetic sensor to detect shaft rotation, along with associated signal conditioning and processing electronics mounted inside the housing. An external shaft with bearing arrangement provides the mechanical mounting point (see figure-drawing). Due to the nature of the sensing technology used, resolutions as high as 12-bit (4,096 pulses per revolution) and even higher are possible with encoders.
A resolver, like an encoder, translates rotary motion into an electrical signal but has an analog output that oscillates at a certain frequency. Unlike the encoder, the resolver does this through use of a rotor that interacts with stator windings and laminations, either through inductive or reluctance principles. As a result, the resolver does not require the associated conditioning electronics on-board—they are integrated into the controls or drive electronics. In a resolver-based system, the analog-to-digital conversion electronics determine resolution. A resolver can be housed like the encoder, or frameless to be integrated with an existing bearing structure as in a motor application (see figure-frameless).
Unlike resolvers, encoders have previously been considered too fragile and costly to be considered for use in many off-highway and specialty vehicle applications. However, developments in sensing technology and manufacturing processes have made encoders more rugged, more reliable, and more cost effective than previously attainable. These developments now make encoders a suitable option for the off-highway design engineer to consider.
The question then becomes apparent: Why would one use an encoder or resolver over a potentiometer, hall-effect sensor, proximity sensor or the like? The answer lies in the details of the application at hand and usually involves system accuracy. Essentially, when positional or speed accuracy is critical to machine performance, an encoder is often a suitable solution due to its higher resolution capability. It should be noted that increased encoder resolution does not equal increased encoder accuracy, although these characteristics generally go hand-in-hand. However, increased encoder resolution can improve overall system accuracy.
Higher resolution output from an encoder provides more data for the controller or ECU to process, allowing for more precise control of movement. This can be especially important when performing electro-hydraulic control functions like loader bucket position, lift arm height, or articulated steering feedback. However, more data typically requires more computing power to process and modern controllers are usually up to the task. In addition, many encoders have a higher level of communication ability than point-level devices such as proximity sensors. It is quite common to find encoders that operate on bus networks such as CAN, which make integration into vehicle-based controls easier and make wiring chores less cumbersome.
Crane booms and aerials are good examples of off-highway encoder applications. Absolute encoders (see figure-AR62) are commonly used to measure boom length and swivel (slew) position in aerial platforms. For obvious safety reasons, it is imperative that these systems operate within a certain performance envelope and therefore positional accuracy is essential to acceptable performance. A higher-resolution encoder that provides absolute position without the need for a home reference switch or sensor is well suited to this application. Although potentiometers can also be used in these areas, they are prone to electrical interference and their contacting “wiper” component causes wear and can create maintenance issues down the road.
In the agricultural side of the off-highway industry, rate indication of various processes is fundamental to efficient farming. In planting and seeding applications, knowing the exact rate of the planting process is crucial for plant spacing and proper growth. A hollow-shafted encoder (see figure) can be mounted directly to a hydraulic motor or machine shaft and provides a digital pulse train to the controls, where the frequency is proportional to the speed. Unlike traditional shafted rate indicators, hollow-shaft encoders eliminate couplings that can corrode and cause maintenance issues in the field. Additionally, encoders can provide a second “channel” or output to determine direction of rotation, typically not possible with simple rate indicators. This is especially helpful in reversing systems. In harvesting applications, encoders provide accurate bale length measurement with their increased resolution capability. Uniformity in length between square bales is important when transporting in sea containers where maximizing available space is a must.
Larger construction and mining equipment employing AC induction or permanent-magnet AC motors for hoists, shovels, and draglines, encoders and resolvers are required for proper motor control. Without this feedback, the drives would not be able to control the motors as accurately. In the case with permanent-magnet AC motors, resolver feedback is a necessity for proper commutation of the motor. These applications typically do not function as well with lower resolution devices.
Efficiency gains and Tier 4 emissions compliance is on nearly every manufacturer’s mind these days, so it’s no surprise that hybrid and electric vehicle system development is on the rise. In both hybrid electric and pure electric drive systems, drive (controller) feedback is mandatory to maintain proper control of the torque vector of the electric motor. In addition, accurate feedback provides tight speed regulation and therefore can improve motor efficiency. In these applications, frameless-wound or variable-reluctance resolvers are commonly used as the sensor of choice. As discussed earlier, the lack of on-board conditioning electronics makes resolvers more rugged by nature, and their simple construction, resistance to moisture & fluids, and high temperature capability make them well-suited for hybrid electric motor use.
In summary, there are numerous choices for speed & position sensors in off-highway vehicle applications. Reliability, accuracy, wiring, and of course cost all contribute to the design engineer’s checklist of needs. Many sensors are up to this task, but if resolution, accuracy, and reliability are high on the list, look no further than an encoder or resolver.