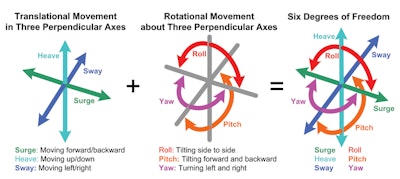
Agriculture equipment operators often face the risk of rollovers due to rolling hills and soft ground, making operator safety a key priority. At the same time, they need to optimize crop yield, which can be lessened by manual functions employed on the farm vehicles. As the need for increased safety and crop yield improvements continue to be top concerns of farm operators, the use of six degrees of freedom (6DOF) inertial measurement units (IMUs) as part of the equipment's electronic control systems are now starting to migrate from construction to agriculture equipment.
Inertial measurement units—which use several accelerometers and gyroscopes to provide accurate and precise motion, position and navigation sensing—improve motion sensing on the equipment by providing measurements for translational (up/down, left/right, forward/backward) and rotational movement (roll, pitch and yaw). These measurements provide key equipment data that enables the accurate and precise control of the vehicle's performance. The benefits translate into increased equipment accuracy, safety and stability as well as improved operator productivity.
Incorporating a 6DOF IMU into the equipment's control module in the chassis to measure the motion of the equipment—whether it's a harvester, planter, tractor or sprayer—can help automate and control manual processes. A few examples include automatically adjusting head blade levels on harvesters or adjusting planter heads on tractors to maximize crop yield and improve operator performance. Automating some of these manual processes provides more precise control than operators can achieve.
Critical safety applications
In safety applications, 6DOF IMUs can be used for stability and steering control, and rollover prevention. Sensor manufacturers can provide any type of signal conditioning required to work with sensor units.
The IMUs help provide ride/motion control to stabilize the vehicle cabin from excessive vibration and movement, particularly on uneven fields. The benefit is two-fold: improving operator safety, and extending the vehicle's life due to a reduction in vibration and mechanical stresses. It also helps reduce operator error by providing traction on uneven surfaces such as rolling hills.
IMUs assist in steering control applications by providing tipping data and preventing the vehicle from moving sideways on hills by using the yaw, pitch and roll data in combination with GPS.
These motion sensors can play a significant role in preventing vehicle rollover, particularly when travelling over rolling hills or on inclines. The IMU can provide a warning to the operator when the vehicle is approaching an angle of tilt or inclination. The data from the IMU also may trigger the fuel to shut off, or in a rollover situation, it may make adjustments to the wheels and steering, depending on the equipment manufacturer's design parameters.
Maximizing crop yield
Accurate and precise harvesting, planting and grading are among the top concerns of farm operators in order to maximize crop yield. Operators typically have to pay close attention to the field terrain. For example, if they are going up or down a hill they manually have to make adjustments to the farm machinery to accommodate for the uneven fields.
The IMU measures the movement of the farm machinery's chassis, sensing in all six directions. It measures whether the chassis is rotating left or right, the inclination of angle (up or down) and if there is any rolling or tipping. This motion sensing can aid operators in two ways. It optimizes the machine performance, and the operators are less fatigued since they no longer have to make constant tweaks and adjustments to the equipment. It also allows for less skilled operators to run the equipment.
If the operator can accurately and precisely control the height of the harvester head blade, for example, relative to the ground position or angle of the vehicle, fewer crops will be left in the field during harvesting. With the data from a 6DOF IMU, farm operators can optimize planting and harvesting tasks by ensuring a flat field for planting, and/or automate harvester blade and planter head adjustments to maximize crop yield in rolling fields.
Yield loss is often related to blades set to a single height on the harvester. An IMU can sense the rolling hills of the field or differences in terrain, automatically adjusting the blade heights accordingly when moving from flat, level ground to rolling hills.
Other critical processes affecting crop yield include seed depth and fertilizer applications. For example, there are a number of factors that could impact seed depth. These include crop residue that could cause the seedbeds to "bump" up, resulting in shallower plant depths, and loose seedbeds that often settle up to a half-inch when it rains. A "bump" effect also may occur if the last tillage pass is at an angle to the planting direction.
All these factors can result in a varied germination pattern across the field. The data from the 6DOF IMU can be used to make adjustments to the planter head to ensure that the seeds are all planted at the same depth based on the land terrain.
Selecting a motion sensor
When selecting an IMU, farm equipment manufacturers should pay attention to several design characteristics. These include durability, stability over a wide operating temperature range, ease of integration, and accurate and precise measurement.
The sensors should provide a robust package that protects it from harsh environments including dust, dirt, stones, pressure washing, humidity and chemicals. A wide operating temperature range will aid in withstanding thermal extremes, preventing device failure. The devices also should meet IP67 and IP69K ratings to provide additional environmental protection, together with electromagnetic interference (EMI) and electromagnetic compatibility (EMC) ratings to protect against radio frequencies.
The IMU should meet the CAN SAEJ1939 standard transportation protocol for communications in construction and heavy vehicles. This allows the output of the sensor to communicate with the vehicle's electronic control unit (ECU).
Although using an accelerometer or inclinometer is often a lower cost solution than using an IMU for farm equipment applications, it requires a lot of upfront design work. In general, when integrating an accelerometer or inclinometer into a vehicle's ECU, the engineer has to design a housing to protect the device, figure out a way to deal with drift over temperature, and determine the best way to incorporate it into the board and connect the sensor to the vehicle control system.
A key benefit of an IMU is its ease of integration. It can significantly reduce the time required by a designer to integrate the sensor unit into the vehicle control system by offering 6DOF motion sensing in a single robust package. It also provides more precise and accurate motion sensing data to keep equipment operators safe, while lowering the risk of equipment damage. Ultimately, equipment manufacturers need to evaluate the different solutions based on their total cost of ownership.