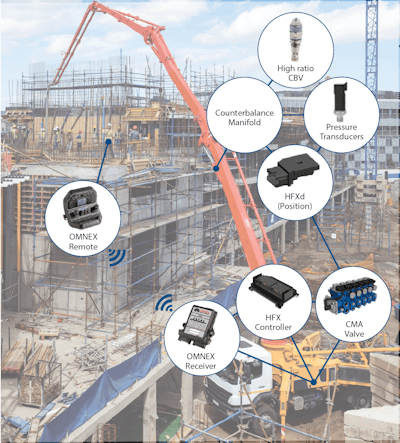
Power management company Eaton announces the launch of its boom stability control technology, a new system that reduces hydraulic boom oscillation up to 75% and boom settling time up to 90%. The technology improves the performance, productivity and safety of boom-equipped machinery, such as concrete pump trucks, fire rescue vehicles, aerial work platforms, hydraulically controlled cranes and agricultural sprayers, and enables active ride control for various construction equipment.
Enabled by a proprietary control algorithm and the Eaton CMA advanced mobile valve, the active damping technology uses the valve’s onboard sensing and independent metering capabilities to detect vibration and automatically stabilize the entire boom structure. Benefits include:
- Faster boom deployment and point-to-point movement
- Enhanced placement accuracy
- A safer environment for those working from or around the boom
- Overall increased productivity for faster project completion
“Our boom stability technology delivers a whole new level of control, which we believe will be standard on next-generation boom-equipped platforms,” says Mike Rannow, Engineering Specialist, Hydraulics, Eaton. “In addition to performance and productivity gains, this technology has the potential to reduce labor costs, decrease component wear and maintenance downtime and enable the use of lighter, less costly boom structures.”
Eaton’s boom stability control is highly applicable for off-highway equipment such as wheel loaders, excavators, backhoes and telehandlers. Utilizing the same active damping technology, the algorithm can predict and smooth roading disturbances, which improves operator comfort, enables increased driving speeds and minimizes loss of material.
Boom stability control requires minimal hardware and wiring on the boom. It integrates with Eaton or original equipment sensors and controllers, maintains machine safety and manual override features and is fully configurable and tunable to the desired feel and performance.