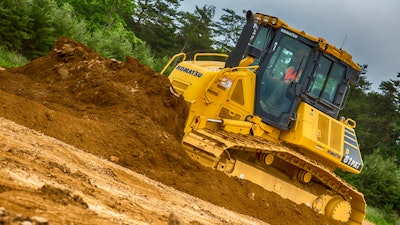
Komatsu America Corp. recently introduced its Proactive Dozing Control logic, a fully-integrated dozing control system that allows operators to perform auto-stripping, auto-spreading and high production dozing, as well as finish grading. Available on the Komatsu D51EXi-24, D51PXi-24, D61EXi-24 and D61PXi-24 dozers, Komatsu’s Proactive Dozing Control logic is built on the company’s existing intelligent machine control.
“Proactive Dozing Control logic opens up a world of application possibilities for machine control technology,” says Derek Morris, Product Marketing Manager, Intelligent Machine Control and Smart Construction for Komatsu. “Traditionally, GPS machine control focused on finish grade, which meant operators only used the technology approximately 10-20% of the time. Proactive Dozing Control logic is a game-changer because the integrated system now lets operators use automation any time, whether for general site clean-up, backfilling trenches and more.”
How does Proactive Dozing Control logic work?
The system uses Global Navigation Satellite System (GNSS) positioning in conjunction with an Inertial Measurement Unit (IMU) to calculate precise position. The two sensors work together to calculate exactly where the tracks are on the ground.
The machine control system communicates with the dozer’s hydraulic controllers, engine controllers and the machine controller. Through cylinder sensor technology, the position of the blade is calculated in relationship to the machine body. The Proactive Dozing Control logic measures the surrounding ground and determines what has been done on the area being graded, then stores that data and information. When the dozer prepares to go back over that area to cut or work it more, the system understands what it was like from its previous track and therefore, follows the existing terrain — the very terrain that was just created.
Proactive Dozing Control logic provides real-time position of the machine on the job site to create a highly accurate elevation for the system to drive the blade to the precise grade needed. Using real-time conditions, the system understands what the terrain around the machine looks like and makes calculated decisions — whether it should cut and carry material, whether it should spread or fill that material, or whether it should be finish grading.
“A key differentiator is that our system collects data at the tracks, while aftermarket solutions collect data at the blade,” Morris notes. “Because data is collected at the track, the system provides a real-time picture of the ground around the machine, allowing the system to make calculated decisions based on the current terrain.” Morris continued, “By collecting data at the track level, we’ve created machine control that is far more advanced, offering an entirely new level of efficiency, whether you’re an operator who has 20 years’ experience or someone new to the job, our Proactive Dozing Control logic provides precision work every time, making operation easier and more productive.”
Reduce owning and operating costs and boost productivity
With Komatsu’s Proactive Dozing Control logic, operators can use the dozer to its full capacity, leading to increased utilization, better ROI and better production. Owning and operating costs are also lowered because wear and tear on the machine is reduced by automating operation. By significantly minimizing track slip during operation, undercarriage wear is reduced, thereby lowering O&O costs, since 50% of the ownership cost of a dozer is the undercarriage.