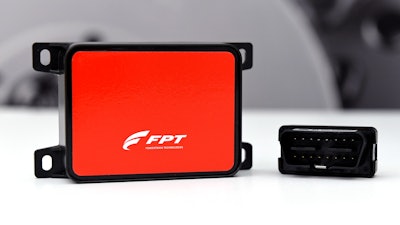
With intelligent devices becoming the new norm in today’s world, FPT Industrial is taking advantage of its technology leadership towards a future of connected engines. To this end, the company is presenting its new telematics solution at EIMA 2018 in Bologna, from November 7-11 (Hall 15, Stand B13).
In the past, fault management was carried out through component analysis only after the issue occurred. Today, connected engines enable remote monitoring and diagnosis, and make equipment tracking easier and more effective and allow engine maintenance to be better managed. As such, dealers and OEMs can provide faster service and support to their customers.
The FPT Industrial telematics kit is easily installable and collects data via the On-Board Diagnostic (OBD) port, sending all information via GSM to a centralized cloud storage. The GSM connection allows users to receive and monitor engine parameters and alerts.
End users can access a mobile app with a user-friendly dashboard that shows key engine parameters, such as load, fluid levels and working hours, the machine’s GPS position and service reminders. As a consequence, maintenance intervals can be scheduled, optimizing uptime and potential malfunctions can be detected early.
FPT Industrial has developed a web portal dedicated to fleet owners, dealers and OEMs providing additional information about the running park. In addition to a comprehensive set of engine parameters, service reminders (both maintenance alerts and fault codes) and GPS position, are used by the portal to present a complete overview of the equipment's mission and engine usage. OEMs, dealers and fleet owners can follow up specific requirements with tailored actions . Fleet monitoring enables advanced services and care, improving fleet management efficiency with a positive impact on overall Total Cost of Ownership (TCO).
FPT Industrial, through a dedicated Control Room, offers a tailor-made service to customers requiring a specific focus on TCO reduction and Uptime optimization. This is done through remote real time data analysis and a proactive activation . As such, OEMs and end users can receive a predictive diagnosis to anticipate unexpected events and enable flexible maintenance.
LIFECYCLE SERVICES FOR AN ENHANCED CUSTOMER EXPERIENCE
To guarantee its customers’ competitive edge, FPT Industrial is offering comprehensive lifecycle solutions. This encompasses not only best in class products and advanced telematics after-sales services, but pre-sales consultancy, and a wide selection of complementary service solutions.
FPT Industrial uses a Product Configurator capable of finding the best solution for each specific customer mission from the thousands of off-the-shelf solutions available. FPT Industrial also ensures correct installation and maintenance of engines by providing specific training courses with information from the latest engine features and guidelines to OEMs, dealers, mechanics and diagnostic specialists. The training programs also guarantee that FPT Industrial customers master the telematics solution to take advantage of its full capabilities. Additionally, customers can rely on FPT Industrial’s Customer Care Service open 24 hours a day, 365 days a year, supporting dealers, service points, OEMs and end-users worldwide.