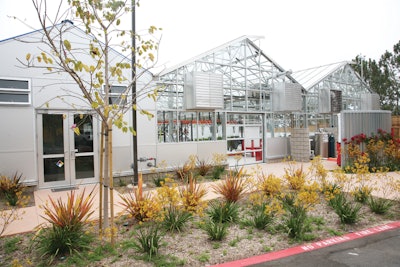
Research into the use of alternative fuel sources is nothing new, though its prevalence has increased over the last several years as fuel prices have risen and fossil fuel supplies have begun to decline. Just this year the U.S. Department of Energy (DOE) announced several funding opportunities, with over $60 million made available for alternative fuel and energy research projects (Read President Obama Announces Funding for Alternative Fuels and Obama Administration Announces New Funding Available for Advanced Biofuels to learn more).
While corn and soybeans are the most commonly known and used renewable fuel sources, research has expanded to include other crops, bacteria and even wastegases as viable options to replace—or at least supplement—the use of fossil fuels.
Turning carbon gas into fuel
Since its inception in 2005, LanzaTech, Roselle, IL, envisioned producing low-carbon fuels from renewable sources without infringing on food, water or land resources. In 2008, the company successfully proved it could produce fuel-grade ethanol from gas resources. Using a gas to liquid platform known as the LanzaTech Process, microbes produce fuels and chemicals from gases containing carbon monoxide (CO), with or without hydrogen, or gases containing carbon dioxide (CO2) and hydrogen.
“The feedstock gas can be carbon-rich waste gases generated as a manufacturing by-product in a variety of energy intensive process industries,” says Jennifer Holmgren, CEO of LanzaTech. These industries can include steel production, petroleum refining, cement manufacturing and chemical processing. She says syngas generated from biomass resources, such as agricultural waste or organic industrial waste, can also be used for the conversion process.
The process works by feeding waste gas into a reactor filled with water and LanzaTech’s proprietary microbes, which consume and ferment the carbon-containing gas into reusable products. From the reactor the waste gas by-product is fed into a hybrid separation system which separates the usable product and co-products, and sends them further down the process line for additional refining or immediate use. Water is also recovered in the hybrid separation system and recycled back into the reactor, helping to increase efficiency and minimize water discharge.
LanzaTech’s proprietary microbes are designed to be flexible to the amount of hydrogen contained in the waste gas. If necessary, the microbes can produce hydrogen from carbon and water. “This ability to operate in the absence of added hydrogen enables LanzaTech to utilize a broad range of feedstocks,” says Holmgren. “And, more importantly, reduces hydrogen demand in the overall fuels production process.” Holmgren also notes that the microbes are tolerant to the extreme levels of contaminants often found in waste gases, enabling the company to use the lowest cost, most readily available waste resources for the process as well as capture, sequester and reuse large amounts of greenhouse gases (GHG).
Products derived from the LanzaTech process include fuel grade ethanol, acetic acid and butanol, which can either be used immediately or with a partner technology to convert it into diesel, jet fuel or other products.
“We estimate that roughly 65% of steel mills worldwide use technology that could be retrofitted with the LanzaTech Process,” says Holmgren. “We have completed GHG impact assessments of our gas to liquid technology with two external parties and both have shown between 40 to 60% reduction in CO2 emissions compared to gasoline.”
Switchgrass-eating E. coli
In late 2011, researchers at the DOE’s Joint BioEnergy Institute (JBEI), Emeryville, CA, engineered strains of Escherichia coli (E. coli) bacteria to digest switchgrass and produce fuel. Greg Bokinsky, a researcher at JBEI involved with the project, says the E. coli was engineered in two separate ways that were then combined together. “First, we genetically programmed the cells to have the ability to consume plant biomass by making plant-degrading enzymes,” says Bokinsky. “Second, we constructed groups of genes, called pathways, which perform sequential chemical transformations that turn the chemical building blocks of cells into compounds that resemble fuel.” Three different pathways were then put together to make three different compounds—fatty acid ethylesters, butanol and pinene—which can be used as biodiesel, a gasoline substitute and a precursor to jet fuel. After engineering the E. coli, switchgrass was treated with ionic liquids to loosen its structure, enabling the E. coli to easily to break it down into its component sugars and turn the switchgrass directly into biodiesel, butanol or pinene.
According to Bokinsky, E. coli was chosen because the basics of genetically programming the bacteria had been worked out over decades of research, and there was already an established knowledge of how genes installed into it will behave. He says JBEI’s system could potentially work in other bacterial species as well, as long as it’s a species that researchers already know how to genetically manipulate.
Switchgrass is easy to grow in large amounts without much need for fertilizer or other inputs, which is why JBEI chose it as the plant biomass for its research. JBEI also found other biomass plants, such as eucalyptus and yard waste, could be consumed by the engineered E. coli when treated with ionic liquids. “It’s important to be able to use as many types of plants as possible for biofuel production as switchgrass probably won’t grow well everywhere you might want to have a biofuel crop,” says Bokinsky.
JBEI’s newly developed process offers the benefit of producing fuel from plants in one step, whereas traditionally three steps are necessary to make biofuels. Other biofuel production methods require harvesting large quantities of plant-degrading enzymes from a fungus, mixing the enzymes with biomass plants to convert them into sugars and finally feeding those sugars to a bacteria or yeast which ferments them into a biofuel. Bokinsky says doing these three steps separately requires three processes, several vats and a lot of capital investment. “[Our process] could allow someone to take their harvested plants and put them into a single vat where all three processes can happen at once—the enzymes are made by the bacteria, the plants turn into sugars, and the sugars are turned into fuel,” says Bokinsky. “[Biofuel production process] consolidation is expected to lower costs, hopefully to the point where biofuels can become economical.”
While JBEI sees many opportunities with its new method for producing biofuel, there are still some challenges to overcome. Bokinsky says the traditional three-step process for biofuels has the advantage of being able to harvest much larger amounts of enzymes from fungus than the engineered E. coli can. There is also still an issue with engineering bacteria that can eat plants as quickly as natural bacteria, which has learned how to after millions of years of evolution. “One obstacle we constantly encounter is that we’re trying to manipulate living bacteria, not electrical circuits or computer software,” says Bokinsky. “We haven’t quite found the hang of engineering them to the point where we can reliably produce tons of fuel.”
The ionic liquid pretreatment used on the switchgrass is relatively expensive, though research is being done to find ways to bring down costs. “There are lots of ways to improve the technology,” Bokinsky says, “from tweaking the plant-eating enzymes our E. coli is making to using an entirely different species of bacteria that can handle the modifications we engineered better than our E coli.
“I think that advancements will accumulate, our engineering intuition will develop, and as a result, the costs of production will inch down steadily over the years. I’m not sure if there will be a single breakthrough, but certainly the potential is there for us to have a homegrown, fully renewable, carbon-neutral source of liquid energy.”
Algal biofuels
Various companies and organizations, such as the Department of Defense (DOD), have been investigating the use of algae to produce biofuels over the last several years. In 2009, ExxonMobil, Irving, TX, began working with Synthetic Genomics Inc. (SGI) of La Jolla, CA, to research and develop biofuel from photosynthetic algae. The two companies built a large greenhouse in which they would be able to grow algae in real-world conditions to study whether large-scale development of algal biofuels is possible. Both natural and engineered strains of algae are being studied under varying temperatures, light levels and nutrient concentrations.
The University of Illinois at Urbana-Champaign has also been researching the use of algal biofuels (search 10743443). Led by Lance Shideman and Yuanhui Zhang, professors in the Department of Agricultural and Biological Engineering (ABE), the research is focused on converting swine manure, as well as algae, into crude oil. Shideman and Zhang’s system consists of first converting the swine manure into crude oil, then using the resulting wastewater (which contains nutrients like nitrogen and phosphorus) to grow algae. Along with producing a viable biofuel, the algae treat and purify the wastewater, recycling nutrients and capturing carbon dioxide.
One of the benefits to using algae for biofuel is its ability to grow quickly in a variety of environments, including wastelands unsuitable for growing other crops. It also requires very little input to grow; all that is necessary is sunlight, or another form of energy, water, carbon dioxide and a few inorganic nutrients. Not much land is needed to grow algae, either, adding further benefits to its use as a biofuel.
Research has shown that algae has the ability to produce a lot of fuel. According to the Algal Biomass Organization, algae can produce 2,000 to 5,000 gallons of biofuels per acre per year. However, producing algal biofuels is expensive – approximately $100 per barrel, which is equivalent to $2.41 per gallon at the gas pump. Further research is being conducted to find ways to bring these costs down, though, and make algae an affordable biofuel option.
Water is also an issue with algal biofuel production. Growing algae takes a lot of water, and disposing of it once the algae are done growing is a challenge. Some researchers say a possible solution to this is harvesting natural algal blooms already growing in water sources.
While more research into the applicability and sustainability of alternative fuels is necessary, current advancements demonstrate their potential to help alleviate the burden placed on fossil fuels being the sole fuel source for the world.