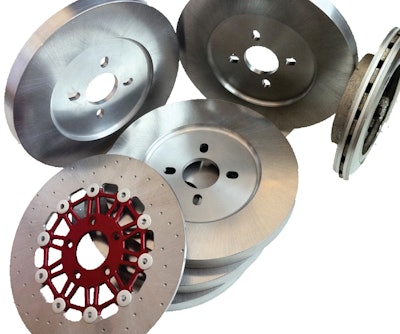
Losing weight seems to be on everyone’s mind. But while light weighting is at the top of most OEMs' lists, Michael Gilbert of SABIC’s Innovative Plastics business says system cost reduction through the consolidation of parts is also important, as is sustainability. “We’re doing a lot of work towards providing more sustainable solutions for our customers,” says Gilbert, General Manager within the Engineering Resins Group at SABIC, Pittsfield, MA. A big part of this has been replacing thermosets, a non-recyclable form of plastic, with thermoplastics, which are recyclable. Gilbert says thermoplastics are inherently more processable, enabling engineers to create unique shapes and more easily consolidate the number of parts in their systems.
OEMs will continue to try to design lighter weight vehicles to provide increased fuel efficiency and meet reduced stopping distance regulations. “We have found that 46% of the commercial trucking market considers light weighting extremely important or very important,” says Jim McManus, Business Development Manager at Century 3/Plus LLC (Century), Traverse City, MI.
And rising fuel prices will continue to drive the need for fuel efficiency, and thus light weighting, as well as future government regulations. Dominic Hill, Customer Technical Services, Lifting & Excavating Lead at Tata Steel Europe, London, United Kingdom, says future legislation will begin focusing on the vehicle itself. “The next generation of legislation which will come out in the next three or four years is likely to look at how much CO2 you generate when you’re actually using the vehicle.”
To meet their varied requirements, OEMs and component manufacturers turn to materials providers to help them create parts and systems that will meet all of their needs. Being pulled in so many directions to meet a variety of sometimes opposing requirements has been challenging for materials providers, but it has also led to some unique and innovative solutions, and an expanded offering of materials which manufacturers hadn’t considered using before.
High-strength steels
Due to their strength and durability, high-strength steels work well for structural or supporting applications in which they will be bearing weight or lifting objects, as well as impact and wear applications, such as for a truck bed. Jeff Moskaluk, Chief Commercial Officer at SSAB Americas, Lisle, IL, says the steel’s application is generally determined by how it’s alloyed. “It’s a combination of the chemistry that is put into the steel and the manufacturing process for the material,” says Moskaluk. “It’s as much about how you bake it as it is about the recipe itself.”
Creating steel with the right combination of strength, durability and reduced weight isn’t easy though. “The main challenge with material development is people wanting different things at the same time,” says Tata Steel’s Hill. “The challenge is to go in five different directions at the same time.” He says if all a customer wanted were a higher strength steel, then it would be easy enough to add more alloys to get the desired effect. But, because they also want improved weldability and toughness, developing the steel becomes more of a challenge. “The thing you’d add in metallurgically to create increased strength naturally starts making a compromise in terms of weldability, formability, ductility and toughness,” Hill says.
Traditionally, carbon was added to steel in order to make it stronger but this makes the steel less weldable, as well as diminishes its toughness. Mixing different alloying systems is one way steel manufacturers can create a product that will meet customers’ varied needs. Hill says Tata Steel also looks at chrome levels and different types of steels, such as boron steels. Like Moskaluk, Hill notes the importance of finding the right combination of chemistry and material processing to create a product for customers’ application needs. The temperature and speed at which the steel is cooled can be a crucial factor in determining how it will perform. “Steel is fundamentally more flexible than other metals because it’s got a large number of phases, each with different properties,” says Hill. “If you cool steel at different speeds, you get completely different products.”
The cost of high-strength steel is often a concern for manufacturers who might consider using it. Moskaluk says that while high-strength steels appear to be more expensive than mild carbon steels, it’s important to look at what the total maintenance cost and life-cycle expectancy is for the application the steel will be used in. High-strength steel can actually be more cost effective in the long run because customers don’t need to buy as much as they would carbon steels in order to get the same stiffness and strength. It is also better able to withstand rigorous, abrasive or harsh operating environments, reducing maintenance time and costs. “If you have something that can be operated for 2,000 hours instead of 800 hours before being replaced, that’s a big deal,” says Moskaluk. “And if you can build it strong enough to where it can run four or five years instead of two or three, [that’s important] to the total lifecycle of a piece of equipment.”
Metal matrix composites
Though metal matrix composites (MMCs) have been in existence since the 1950s, they have yet to find a foothold in the heavy-duty vehicle industry. The increased interest in light weighting over the past several years, however, has started to bring more attention to this material. MMCs are typically a combination of ceramic and aluminum, although there are also ceramic and magnesium MMCs. Aluminum is used because it is light weight, featuring a density two and half times lower than iron, and it is able to extract heat three times better than iron, which is important when making a part such as a disc brake. Because aluminum is a lower density material with low hardness, silicon carbide ceramic is added for wear resistance; it also helps maintain high performance at elevated temperatures. “When a brake gets hot, the ceramic addition into the aluminum improves the material strength and dimensional stability,” says REL’s Halonen.
There are numerous ways MMC parts can be made. REL uses a functional gradient method which places a higher ceramic concentration on a brake’s friction interface and reduces the ceramic concentration in areas where it is not needed. For a brake rotor, a higher concentration of ceramic is used on the outer perimeter of the rotor with less ceramic towards the center. On a brake disc, where the outer perimeter is spinning the fastest and is the hottest, this helps provide stability during long braking events and eliminates brake jutter and warping of the rotor. The functional gradient eliminates the sharp contrast in stiffness and the coefficient of thermal expansion (CTE) between the MMC and the unreinforced aluminum alloy.
Century, on the other hand, uses a method called selective reinforcement in which the MMC is put where it’s needed. “This technology we have is all about taking the properties that you might find in cast iron and steel and inserting them to where you need them in the part,” says McManus. On a brake drum, for example, Century will create a ceramic hoop which is infiltrated by aluminum; the sponge-like pores of the ceramic soak up the aluminum to create the metal matrix. This MMC hoop will become the inner wear surface of the drum, while the rest of it will be made from just aluminum. “You end up with a wear surface area of the brake drum that is really wear resistant, stiff and strong,” says McManus. “It has properties of cast iron.” Making the entire brake drum out of MMC, known as a 100% reinforced MMC part, would not work either. McManus says for this particular application the machining cost would be prohibitively high and being completely MMC would eliminate the advantages of having ductile aluminum surrounding the high stiffness aluminum MMC.
MMCs can be used for various types of parts, “essentially any part that an engineer would want to light weight without losing stiffness, wear resistance and strength,” says McManus. Halonen adds that for heavy trucks, MMC parts are best suited for trucks that get heavy before they get full, such as bulk haulers. Both REL and Century have focused their MMC work on brake parts due to OEMs’ strong interest in saving weight on the wheel-end of their vehicles because of the concepts of sprung and unsprung mass. “When you save weight on the wheel end (unsprung mass), it has a quantifying effect as how it relates to the rest of the vehicle (sprung mass),” says McManus. “For every pound you can typically save on the wheel end, quantitatively it means up to another four pounds of weight savings for the vehicle.” He says this is why so many vehicles have aluminum rims and hubs, as well as plastic parts.
The weight savings can really start to add up when OEMs use MMC parts. Century has prototyped a 16 1/2 inch x 7 inch drum for use on the rear axle of Class 7 to 8 trucks. The MMC brake drum weighs 62.5 pounds, while a cast iron drum of the same size for the same application typically weighs 113 pounds. “It’s 50 pounds of weight savings per wheel end, which equates to 100 pounds [per] axle,” says McManus.
Plastics
Plastics have been making their way into vehicle designs more and more over the past several years as their strength and reduced weight characteristics have improved. “We continue to work to manufacture plastic materials that improve the strength to weight ratio,” says SABIC's Gilbert. To achieve this, SABIC has been expanding its portfolio to include LEXAN polycarbonate resin and co-polymers which offer better weatherability, improved impact resistance and higher flow.
Flow is an important aspect to the makeup of a plastic because a higher flow provides greater design flexibility for the customer. “Improving the flow of plastic materials allows the molten material to go over longer spaces before it cools so [manufacturers] can make bigger parts,” says Gilbert. SABIC provides customers with plastic pellets which are heated until the pellets become a molten material that is pushed into a mold to create a particular shape or geometry. “You can get into some really unique geometries and shapes to create the style that a particular customer is looking to achieve,” says Gilbert. This is especially helpful for OEMs looking to consolidate the number of parts in their vehicle or in a particular system.
Gilbert says SABIC is continually looking at what types of fillers it can put into plastics to improve stiffness and strength while still meeting light weighting requirements. Carbon fiber filled plastics is one area Gilbert sees as an area of promise because they provide “incredible strength properties.”
With sustainability being such an important aspect to SABIC and its customers, the company has been working to develop more “green” products as well, such as its Valox iQ resin, a polybutylene terephthalate (PBT) resin made from up-cycled plastic bottles. Used as a feedstock to create the plastic material, SABIC’s proprietary process enables the company to use up to 65% post-consumer plastic waste, “[which] can significantly reduce the carbon footprint somewhere between 50 and 85% lower than other engineered resins,” says Gilbert. Through this process a plastic bottle’s life can be increased from weeks or months to decades depending on the application it goes into.
Volvo Trucks recently began incorporating Valox iQ resin into its 2012 heavy truck platform. (Visit oemoffhighway.com/10688832 to read more about Volvo's use of Valox iQ.) The company replaced metal brackets on the side air deflection system of its truck with brackets made from Valox iQ resin. Besides the sustainability advantage, Gilbert says Volvo was able to reduce weight by using the PBT resin instead of metal, as well as the number of steps required to make the brackets and assemble the system. “There were cost advantages, manufacturing advantages and consolidation of parts,” says Gilbert. “That made it a win all around.”
Additional sustainability efforts SABIC has been working on include the development of molding color into a plastic in order to eliminate secondary coating steps. This helps to eliminate or reduce the amount of painting a component needs, as well as the volatile organic compounds (VOCs) associated with it.
Iron
SiboDur—‘Si’ for silicon, ‘bo’ for boron and ‘Dur’ for durability—is an ultra-high strength cast ductile iron material that helps manufacturers reduce weight by casting only the exact amount of material where it’s needed. Developed by Georg Fischer AG, Grede Holdings LLC, Southfield, MI, is exclusively licensed to produce SiboDur in North America. “Where there is high stress concentration on a given part with a given load path, then we can leverage SiboDur to its fullest strength and cost value,” says Jeff Nichols, Director of Business Development at Grede. “It’s going to be of specific value to our customers where there is interest to reduce cost and mass with high stress, high toque, high load applications.”
A truck bracket rear axle produced from SiboDur, for example, provided an 18% weight savings; the original steel welded version weighed 26 kilograms while the SiboDur axle weighed 21.3 kilograms. This represents 4.7 kilograms of weight reduction by placing the material only where it was necessary, and still maintaining strength properties that were necessary for such a safety-critical component. Often times to reduce weight manufacturers are forced to make tradeoffs. With aluminum for example, it provides the mass savings OEMs are looking for, but forces them to give up tensile strength, design envelope space and can add cost. SiboDur, on the other hand, is not only three times stronger than aluminum, but it also offers a good balance of ductility, tensile strength and elongation up to 20%. “You can’t take weight out and reduce strength at the same time,” says Nichols. “Our objective is to maintain or increase component strength and decrease mass through design optimization efficiencies, and that’s exactly what the SiboDur material properties allow us to do.” He also notes that because SiboDur is a cast material process, it provides more design freedom. “[It’s] opening up doors for new creativity and design.”
SiboDur also has its environmental benefits. Nichols says Grede’s iron process for the material has the lowest CO2 footprint in comparison to steel, aluminum or magnesium, and it’s a 100% recyclable material. Grede also reuses the scraps it produces when processing SiboDur. The casting gates and risers that are required to produce the casting are re-melted to then be utilized to produce the next batch of material. “Much of our base material that we use for raw alloys comes from recycled products,” says Nichols.
When choosing which material to use, OEMs must keep a number of factors in mind, most importantly the application in which the material will be used. All of the materials providers agree that working with customers up front is the best way to determine which material will best suit their needs. “It’s [about] working smarter and more cohesively with our customers in the early design conceptualization phases,” says Grede’s Nichols. “The sooner we can get involved, the more mass [savings] and design optimization we can achieve together as customer and supplier partners.”