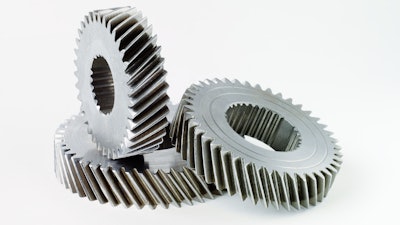
Mechanical designers of powertrains are under pressure to improve the power density and extend the lifetime of their systems. Elias Löthman, Application Engineer at steel manufacturer Ovako, explains why clean steel has the potential to achieve this and how engineers can use advanced software to evaluate the design impact.
Steel fatigue is one of the limiting factors in high-cycling applications such as gears, bearings and shafts. Under these circumstances, highly stressed components can eventually initiate microscopic cracks which during each revolution will slowly propagate and finally result in a fatigue failure.
Good design can reduce the peak stresses in critical areas of the component that are traditional crack initiation sites. However, it is only part of the solution. Fatigue can also initiate due to inclusions, which are microscopic non-metallic particles that exist in all types of steel.
In a loaded powertrain component, these imperfections will increase the stresses in microscopic areas within the material. Over time with many load cycles, these small areas will initiate small cracks that will eventually propagate and lead to failure.
These inclusions themselves are common knowledge, and many design guidelines consider them, although the effect of removing the harmful inclusions and reducing their size is not as well known.
That is why steel manufacturer Ovako recently partnered with GWJ Technology. The companies wanted to determine a way of evaluating the impact of steel performance in an actual powertrain component during the design phase. This includes evaluation of steel types, particularly clean steel, which can have positive impacts on component and overall system performance.
Good design can reduce the peak stresses in critical areas of the component that are traditional crack initiation sites.Ovako
Integrating clean steel performance into gear design software
Powertrain design is complex. Engineers face the challenge of making many iterative calculations to design-optimize gears and integrate them with the rest of the system. Any small change could have an impact on how loads are transferred into gears and shafts and effect the lifetime and performance of the powertrain system.
To change steel grade or switch to a higher performing version of the current steel grade requires a lot of testing and validation before you get an idea of how much more torque you can put through your system or how small you can make the components. This is generally done in dedicated test rigs and the performance is not always easy to translate into your own designs. Not all OEMs have the capacity or resources for this, even if they are keen to evaluate the potential for clean steel.
Therefore, recognizing the opportunity for engineers to better understand how this improves powertrain performance, software provider GWJ has incorporated two clean steels into its gear design software, eAssistant, TBK and GeearEngineer. As a result, mechanical design engineers are now able to compare high-performance clean steel with standard materials.
The software covers multiple types of gears, bearings and shafts and can be applied to design anything from a tiny component in a medical device to an entire gearbox in a multi-megawatt wind turbine. The packages can interface with a 3D CAD package to generate the code to produce components on a multi-axis machining center.
The algorithms in the software are based on engineering equations for gear design and cover different types of gears, mechanical design, materials science, CAD and machining, as well as the relevant international standards and design guidelines for design of gearboxes and power transmission systems.
Ovako’s recently implemented 159X (BQ-Steel) and 159Q (IQ-Steel) clean steel grades are two of the many materials built into the software. In terms of their chemical composition, both are identical to the case-hardening steel grade of DIN 18CrNiMo7-6. The significant difference is the increased contact fatigue strength and bending fatigue strength.
Comparison of 18CrNiMo7-6 and 159Q steel.Ovako
Comparing cost and performance
When sourcing materials, it is easy to focus on the cost per kilogram or other easy-to-measure values. As you’d expect from a high-performance material, the clean steel has a slightly higher price per kilogram. However, due to its higher fatigue strength it can withstand significantly higher stress throughout its life. If you instead compare cost per megapascal (MPa) or even more interesting, the total cost of the system per newton-meter (Nm), the real benefits start to appear.
By optimizing the design together with the material performance, the total cost at the component level will be similar or lower, and even more so if you look at the whole system. As a result, you will have significantly higher power density in the system, using less material.
Clean steel
Clean steels are produced under carefully controlled conditions that limit the size and number of harmful inclusions. They have the same chemical composition and yield strength as a standard steel but have significantly higher fatigue strength.
OEMs can use the higher fatigue strength of clean steel to transform their systems to an extent that has not been possible before. Whether the goal is to extend lifetime, reduce size, increase efficiency, or a combination of the three. The material performance can increase the power density in different ways.
Different types of clean steel denominations are out there and unfortunately some not-very-clean steels are still marketed as such. There is also a seamless transition ranging from standard steel to ultra-clean steels, making it hard to define where you need to be based on a certain design goal. Clean steels are produced under carefully controlled conditions that limit the size and number of harmful inclusions.Ovako
To facilitate the selection, Ovako has set two levels along the ladder. BQ-steel (bearing quality) is a clean steel which brings bearing cleanliness performance to case hardening grades, resulting in significantly better fatigue strength both in terms of contact fatigue strength and bending fatigue strength.
However, IQ-steel (isotropic quality) provides a major step change in both types of fatigue strength. It is produced under strictly controlled conditions in the steel mill to ensure that inclusions are small and spherical. The spherical shape means that the steel provides the same high performance regardless of stress direction, resulting in isotropic properties.
This improved fatigue performance opens up new design opportunities for powertrains.
Evolving standard specifications
There are a few reasons to explain why standard steels are still dominant for rotating parts in powertrains. First, the advancement in simulation and production technology has been increasing the power density on its own. Second, advancements in post-processing such as shot peening have been increasing power density even further. Material performance can provide further leverage alone or in combination with post processes.
Steel cleanness is often not included in a relevant way in standards and material specifications, and therefore its effect is often neglected. These documents are then used by OEMs when they develop new systems and often integrated in the internal material libraries of “allowed materials.”
However, unless they are reviewed regularly, these documents may not reflect modern steelmaking technologies and available material performance. Ovako has found that some companies have been working from standard procedures that are based on allowable stress levels established in the 1930s.
There have been significant developments in metallurgy over time, and OEMs might miss out on a competitive edge by not keeping their material libraries up to today’s standards.
Physical testing
Theoretical calculations are helpful but engineers want practical proof. While calculations give a very good understanding of what the material is capable of, there are still some steps that needs to be further verified and identified.
Ovako is currently conducting additional testing of bending fatigue performance in gears made from different levels of clean steel and comparing the impact of different manufacturing and post processes. The goal is to assist in finding the most cost-effective combination of material cleanness, manufacturing methods and post-processing.
In parallel, Ovako has been cooperating with institutes such as WZL at RWTH Aachen and FZG at the Technical University of Munich over many years to further understand the full potential of clean steel in powertrain components. OEMs can use the higher fatigue strength of clean steel to transform their system designs.Ovako
Metallurgical developments such as that of clean steel highlight how important it is for OEMs to review their lists of approved materials every few years to allow themselves to make use of the constant improvements in available material performance.
This article was contributed by Ovako, a European manufacturer of engineering steel for customers in the bearing, transportation and manufacturing industries.