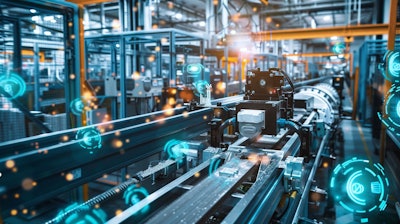
Despite years of buzz about condition monitoring and predictive maintenance, momentum for these data-driven technologies is just getting started. To date, the sensors and software that enable those capabilities have been expensive and complex, limiting deployment to all but the largest industry giants. The same hurdles have also held back offerings from some original equipment manufacturers (OEMs).
Challenges like these often inspire innovation. In this article, we’ll explore the advantages of an emerging generation of components with built-in feedback capabilities. Together, they’re helping to make predictive maintenance less expensive, less complicated, easier to integrate and more attractive to your customers and prospects.
Why Predictive Maintenance?
Most operations in the industry today do preventive maintenance because they can’t predict when something will go wrong. Parts get replaced on a regular schedule, stopping the line by default, even if nothing needs to be fixed.
Let’s say a fulfillment center is shutting the line down every six weeks to do this. Perhaps they could keep running for eight or nine weeks without stopping but have no way of knowing the condition of their system. Preventive maintenance is considered a necessary evil to minimize the risks of unscheduled downtime — even though a lot of time, money, and parts are likely being wasted.
Those resources are even more precious if scheduled maintenance falls during a peak shipping season like the fourth-quarter holidays. How much more value could your customers realize in December if they could be confident about their systems for an extra two or three weeks?
Predictive maintenance offers a more efficient strategy by continuously monitoring critical components for signs of reduced performance or potential failure. Instead of replacing parts that still have useful service life or waiting for a breakdown, you can get detailed insights about the health of a system. If anything, critical isn’t functioning normally, you can pinpoint its exact location, get details about the root cause, and make informed decisions about how quickly you’ll need to act.
Predictive maintenance optimizes repair costs by minimizing failures and avoiding high costs of reactive or preventive strategies.
This radical shift from traditional maintenance isn’t new; it’s already been tested and proven by some of the industry’s biggest players. But its key advantage and primary drawback are the same: data.
Data, Data Everywhere
The collection and analysis of equipment data has traditionally faced three major hurdles:
- Keeping track of every key component has typically required many expensive devices, such as photoeyes, accelerometers, vibration sensors and others. These devices must also be calibrated by trained process engineers, increasing workforce needs.
- Different brands or types of sensors communicate in different ways, with little commonality or standardization.
- Once in place, sensors generate vast amounts of data that are difficult to interpret and act upon, especially for floor-level workers. Too much information can be as bad as none without sophisticated software to analyze and interpret the results.
So far, these factors have placed predictive maintenance beyond the reach of many small- and medium-sized operations. Today, however, components that can “talk back” are cutting a lot of costs and complexities out of the process.
Realizing the Promise of Predictive Maintenance
Components that provide feedback are making it easier to integrate data-driven capabilities into warehouse automation systems. They’re less expensive than add-on devices or sensors, require no calibration, and provide feedback to programmable logic controllers (PLCs) through a simple wire harness. Current usage, acceleration, divert positions, and many other conditions can be monitored in real time.
Data granularity varies depending on the product. The most basic level of feedback is analog signals for conditions like normal operation, warnings, or faults.
Warnings alert you when some component of the system isn’t performing within an adjustable threshold. Although the situation isn’t critical, you’ll want to investigate at a convenient time, such as your next scheduled shutdown.
Fault signals are more serious because they indicate when a component fails, potentially impacting the entire system. Depending on the system, you can be alerted if any fault occurs or use a counter to account for isolated incidents. For example, an alert might be sent out only if a predetermined number of faults occur during a shift or 24-hour period.
Understanding the Data
Knowing what the problem is can be just as important as detecting a potential issue before it disrupts the system. Many skilled technicians are retiring, and qualified replacements are in short supply. Detailed insights from predictive maintenance systems are increasingly valuable in this environment.
Let’s say a warning occurs during a night shift when less-experienced maintenance workers are on duty. Does the problem need to be dealt with right away, or can it wait until a more experienced tech returns in the morning? If it needs to be fixed immediately, can the tech on duty handle it during a 15- to 20-minute shutdown? Does someone with more training or OEM support need to be called in? Software tools on your customer’s local network can help maintenance teams make fast, well-informed decisions based on robust data.
Preventing failures isn’t the only benefit of this technology. Users can also track performance trends to monitor throughput, identify bottlenecks, optimize scarce labor, and find opportunities to utilize equipment more efficiently.
Selling the Benefits
Components with embedded sensing and the subsystems that interpret their data come with slightly higher costs. The trade-off quickly pays for itself by enabling predictive capabilities, preventing unscheduled disruptions, and reducing the unnecessary costs required for less efficient preventive maintenance. They can also create savings from day one by reducing the number of more expensive sensors a system requires.
Although predictive maintenance is a proven and rapidly maturing field, it’s still seen as new by many customers who fear the risks of adopting it too soon. Demonstration loops offer a valuable way to overcome their concerns by showcasing and proving the value of predictive systems. Data-savvy components also give you the ability to better predict the capabilities of the systems you develop. Each customer can be shown quantifiable savings estimates calculated from their use cases, helping you build a stronger value case.