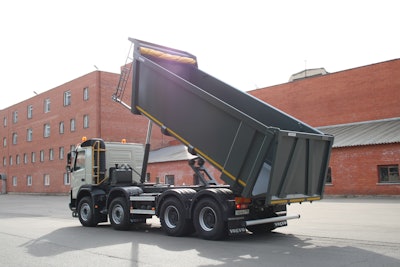
At this year’s CONEXPO-CON/AGG 2011 in Las Vegas from March 22 – 26 SSAB will be presenting innovative applications of high strength steel and wear plate (booth 10808, South Hall Level 1).
- Highlights include revolutionary dumper and trailer designs, and special software tools for optimizing material selection and production processes.
- Exhibits will include an Arc Design dumper body (Hardox wear plate), a lightweight truck trailer/chassis model (Domex high strength steel), and a Hardox Wearparts display showcasing wear parts for the construction, aggregates and yellow goods industries.
- Customers can Meet the Experts for one-on-one consultations by previous appointment or as available, ensuring customers are making the best use of SSAB’s new and expanded range of Domex and Hardox products, including – for the first time – Hardox with a thickness of only 3 mm.
Arc Design means lighter, stronger dumper bodies
Arc Design is an SSAB-patented innovative convex dumper design that cuts tare weight while increasing service life of dumper bodies. It combines the flexibility of the conventional dumper with the light weight of the half-pipe dumper. The key feature is a convex floor to the dumper tray. This is made of Hardox wear plate which absorbs impacts, increasing durability and preventing cracking. The design – which is particularly suitable for dumpers that transport sand, gravel, rocks and scrap – combines the benefits of the heavier but more flexible conventional dumper with those of the half-pipe dumper which utilizes the strength of steel plate and can therefore be built lighter. The new design allows side and backward tipping, has a low center of gravity, and has almost the same volume as a conventional dumper. The convex bottom is made by roll-forming Hardox 450 wear plate. This design protects the dumper’s underlying structure from damage, such as dents from large rocks. Compared to half-pipe dumpers, the new design allows increased volume, while being lighter and stronger than conventional box dumpers. The reduced weight means the Arc Design dumper can carry heavier loads, which means fewer trips.
Volvo Trucks is currently testing the Arc Design on its new Volvo FMX truck, built for heavy construction activities. As part of the testing process, Volvo Trucks is providing customers with Arc Design prototypes in various Russian regions for two-week trials. So far customer feedback on performance has been very positive, with Volvo hoping to achieve its target of increasing dumper body payload by 500 kilograms. As an added bonus, Arc Design also allows hot engine exhaust to be passed through the space below the convex floor to prevent materials adhering.
A 1/3 scale model of the dumper will be on display at the booth.
Design concept lowers cost and weight
An all-new lightweight chassis design for trailers increases payload capacity, simplifies production and improves torsional rigidity.
The design is based on the idea that trailer construction should take full advantage of the properties of high-strength structural steel to offer significantly improved performance. SSAB engineers have built a trailer without a conventional frame comprising two sturdy I-beams and cross beams. Instead, they focused on optimizing the benefits offered by Domex 960 – SSAB's 4 mm hot-rolled high-strength structural steel – by designing a self-supporting monocoque chassis. The new chassis consists basically of two halves. Plates are laser cut before bending. Longitudinal profiles can be used at the top and bottom of the trailer to handle forces resulting, for example, from tipping a trailer full of gravel.
In addition to clear benefits for users, the design also cuts production time and cost: There are only two longitudinal joints, which means greatly reduced welding work and far fewer components while facilitating the economical use of using robotic welding and laser hybrid welding. Processing time is much shorter as there is no need for cross members.
A standard chassis on a trailer weighs about 1,500 kg (3,307 lbs), while the new design is almost 500 kg (1,102 lbs) lighter, a reduction of some 33%. While this design is only at the concept stage, SSAB is confident that weight can be reduced even further without compromising safety.
WearCalc 2.0 finds the optimum Hardox for the job
After five years of development, last year SSAB announced WearCalc2.0, an application which allows quick and easy calculation of the relative service life of abrasion-resistant spare parts. Combined with a comparison of material and production costs, the application allows quick selection of the optimum materials for the job. WearCalc 2.0 predicts erosive and impact wear as well as sliding wear for all types of Hardox wear plate.
The erosion model is based on published research as well as on SSAB research with aggregate and large rocks. At macro level, WearCalc 2.0 predicts whether makeup of the abrasive materials will cause edges to penetrate the steel surface or to break. At micro level, the model uses mineral hardness to calculate erosion on different types of wear plate.
WeldCalc 2.0 – Optimized welding at your fingertips
WeldCalc makes decades of welding experience available in a web-based application, helping users optimize both welding procedures and the result. WeldCalc 2.0 includes recommendations for Hardox, Domex and Weldox steels and combinations of different grades. The intuitive user interface and the new export function mean even easier calculation and application of results.
The user enters the desired mechanical properties, welding process and plate materials involved. The software calculates a tolerance envelope showing the permissible heat input, and both working and interpass temperatures.
The new version of this well-established software allows users to save or export results. Logs can be opened, edited and saved again. WeldCalc 2.0 is web-based, ensuring that users are always using the latest version. More information and contacts to access the new WeldCalc 2.0 can be found at www.ssab.com.
Meet the experts
Whether you are trying to meet new fuel-emissions guidelines, increase the strength, wear-resistance or service life of your equipment, or reduce the tare weight of vehicles to increase payload, our experts have the answers. SSAB offers you the opportunity to book a free consultation with our technical managers, wear or design experts to ensure that you take full advantage of the potential of advanced high-strength steel and abrasion-resistant wear plate.