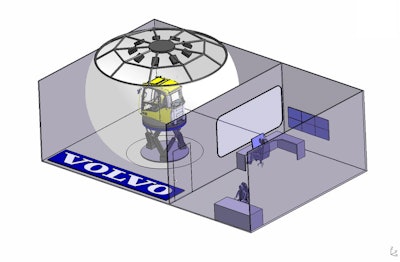
As technology gets ever more complex, it’s becoming more expensive to build prototype machines. Not only that; building prototypes takes a long time and commits a lot of resources. And what if the prototype isn’t effective? You have to start all over again. Because of this it’s becoming increasingly important to shorten the development cycle and use computers to carry out as much virtual testing and simulations as possible. To do this, Volvo Construction Equipment (Volvo CE) is creating a system that is set to revolutionize the product development process and enable technology that doesn’t even exist today to be accurately simulated in real-time – thanks to a human in the loop system.
The latest innovation from the company’s Technology function will provide the operator with the exact experience he or she would get from an actual machine – allowing engineers to assess operability and test crucial factors such as performance and responsiveness before an expensive prototype is built. Through thorough simulation and optimization, the real-time simulator will determine the feasibility of future technology as well as reduce the number of prototypes and ensure that models are built much closer to the final product and at a lower cost.
“Traditionally simulators are used for operator training and they copy an existing machine,” says Lennarth Zander, manager at the Technology function’s Virtual Product Development (VPD) team. “However, what we are doing is creating a real-time simulator for research and development purposes that is able to behave as the next generation of machines will. One important purpose of this project is to understand the experience the operator gets from future generation machines – something that is very hard to do with mathematical models. With this new technology we will increase efficiency and enhance the product development process – ultimately helping to provide the best possible experience for our customers.”
Humans in the loop
“Creating a real-time simulator with a human in the loop is very complicated, but at Volvo we have the expertise and capabilities to do this,” says Lennarth. “It's like building something between a computer simulation model and a real machine. One of the biggest challenges (which has prevented this work being done before now) has been simulating the hydraulic system in real-time. When an operator is involved in the simulation their actions need to be performed accurately and immediately – attention to detail is very important otherwise you're not providing them with a true representation of the machine.”
“We have successfully achieved real-time simulation without compromising accuracy and that's a big breakthrough,” says Jae Lee, chief engineer, VPD/Advanced Engineering. “We've started by programming the engine and hydraulics of an excavator (the most challenging machine) into the simulator and once this project is complete we will continue the work with other Volvo machines. The simulator will feel 100% lifelike and the operator will experience the exact same visual, audible and tactile feedback as if they were in a real machine on a job site. The normal vehicle characteristics for that specific machine – such as hydraulic power, engine sound and the way it maneuvers over uneven ground – are all faithfully reproduced and different applications can be selected. As the operator sits in the simulator cab they will see the machine perform the commands on a spherical projection screen in real-time with no delay – just as they would if they were looking through the windscreen of their machine on a job site.”
Predicting machine behavior
“If someone presents us with an innovation, as long as we're able to describe it in terms of mathematics, we can use a real-time simulator to predict how a machine will behave with that technology and get operator feedback regarding how the machine feels to use,” says Lennarth. “The possibilities are exciting and endless – we can use this advanced technology to test future concepts like heads-up displays, new transmission technology and intelligent machine features. But it will also help us to optimize our current technology and make it as fuel efficient as possible.”
“Testing potential new technology in this way will allow us to see how operators respond to it and their reactions will help to guide the organization before prototypes are built,” continues Lennarth. “For example, if we look at heads-up displays which can inform operators of their production per hour, fuel consumption, vehicle speed, etc., it would be interesting to see whether they found this information useful and if we had got the format right – all before any money is spent on building prototypes. It is also much easier and less costly to make adjustments like this – if an operator doesn't like the performance from one hydraulic system we can simply program another into the simulator until we achieve maximum performance.”
The simulator is being built in Changwon, Korea, and will be completed by the end of 2013.