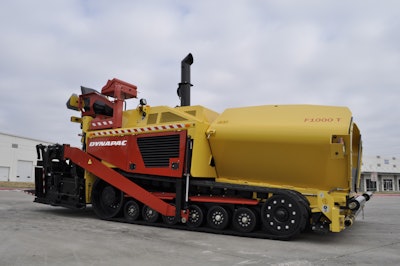
Dynapac, part of the Atlas Copco Group, has launched the next generation series of F1000 pavers to the North American market designed to meet the Tier 4 Interim emission regulations. The F1000 pavers are available in both track and wheeled options to appeal to owners, operators and service crews. Production is taking place at the Dynapac plant in Garland, TX.
To meet the new emission regulations, the upgraded paver series has been equipped with the Cummins QSB 6.7 liter Tier 4 Interim engine. The engine delivers 220 hp at 2,000 rpm or 230 hp at 1,800 rpm. The Cummins Tier 4 Interim engine also provides a direct flow air cleaner and new technology in the form of Exhaust Gas Recirculation (EGR), Diesel Oxidation Catalyst (DOC), and Diesel Particulate Filter (DPF) systems.
Dynapac adjusted the paver duty cycle so that regeneration of the DPF system occurs without disturbing the paving operation in most conditions. A high pressure fuel injection system reduces fuel consumption up to 5% over earlier engines. The Tier 4 Interim engine reduces exhaust emission of particulate matter by 90% and NOx by 45%.
The new cross-flow cooling system features a hydraulically driven, temperature-dependent cooling fan that reduces the overall noise level. The system exceeds performance requirements to deliver a 120 F capability. The cooling system has been designed to work on Tier 3, Tier 4 Interim and Tier 4 Final engines. The fan also has a reverse feature to help clear accumulated debris in the cooling system.
Dynapac’s new auger-conveyor, feed-control system ensures continuous flow of material for quality paving. The feed controller uses four independent, ultrasonic sensors to maintain the head of material precisely.
Visibility has improved with the paver’s platform height of 78 in. and a 63-inch deck height – currently the lowest deck height in the industry. The low height allows full visibility to all working areas around the paver. This low center of gravity provides balance between the paver and screed delivering accurate edge geometry and the best mat quality.
Both models in the new series are designed with a transport width of 10 ft. and a transport height of 106 in. Transport length for the F1000T is 21 ft., while the F1000W is 21 ft. 4 in. Working width is 26 ft. with a minimum working width of 8 ft.
Operation controls have been upgraded with dual swing-out operator panels that are interactive. The panels feature a functional switch layout and toggle switches to improve efficiency and productivity for the operator.
At 34 kW, the hydraulically driven generator delivers a constant 60 Hz frequency regardless of the engine speed or load. This unique capability allows full screed heating at idle, which saves fuel during daily warm up. The generator will heat screed extensions, heat end-gates and provide night lighting if needed.
The Dynapac F1000 pavers offer easy maintenance with the use of standardized components. Common parts have been used in both the track and wheeled pavers. Manual override valves, relays and illuminated DIN connectors are provided. For easy identification, the pavers are designed with group placement of components and individually marked hoses and wires.
The F1000 is also engineered with a multi-function display based on calibration so there is no need for a laptop. The direct flow air cleaner is positioned for optimum air flow and serviceability. The DPF is also ideally positioned so that it can easily be removed for regular maintenance once every 2,000 hours.